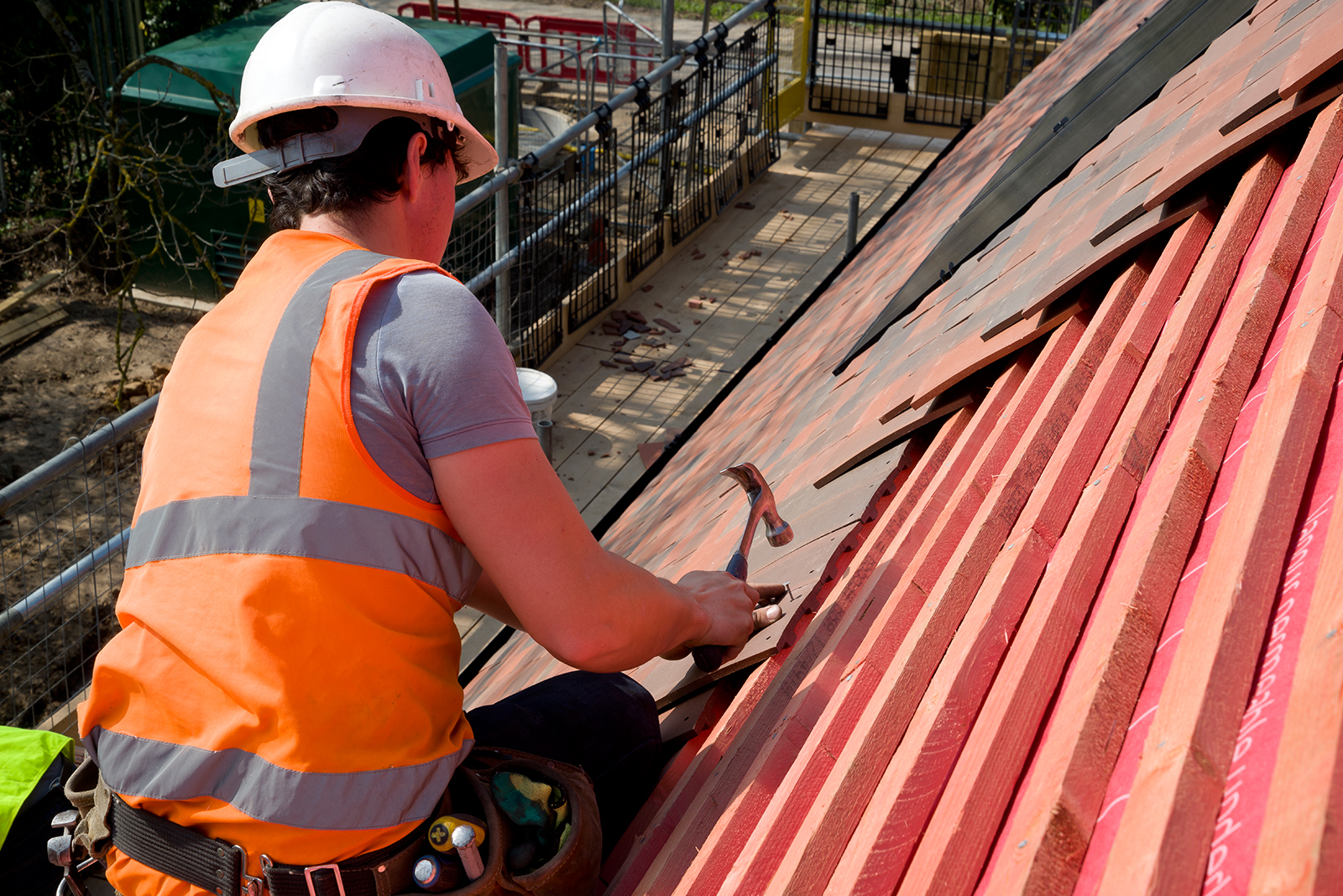
Stuart Nicholson, roof systems director at Marley, says updated guidance will help contractors reduce the risk of moisture damage in pitched roofing projects.
Excess moisture within properties is a significant cause of damage to the fabric of the building and to the health of the occupants. Over time, too much moisture can lead to decay, damp and mould, with poor ventilation also associated with the spread of infections, such as Covid-19.
Improved energy efficiency and climate changes are putting buildings under increasing stress from moisture, which is a particular risk for pitched roofing. Moisture laden air, in the form of vapour, is likely to ascend to the roof space, so there is a risk of condensation build up without adequate ventilation. In fact, damage caused by this interstitial condensation is one of the most common call- backs for costly pitched roofing repairs or warranty claims.
At the end of July, a fully revised British Standard, BS 5250:2021, was launched and this highlights the importance of reducing moisture risk and ensuring correct ventilation levels in pitched roofs. The Standard has been re-named ‘Management of Moisture in Buildings – Code of Practice’ to reflect the fact it no longer just focuses on condensation, but now takes a whole building approach. It has been broadened to include other moisture risks in buildings, such as rain penetration and roof leaks, humidity and high levels of ground water. It also recognises that there are differences between a building when it is designed and how it performs when it is built and in-use.
These updates to BS 5250 are a reminder of the critical role that roof ventilation plays as part of a whole building approach to reducing moisture risk. Anyone undertaking roofing work should familiarise themselves with the new guidance, which gives more clarity on some key issues. This includes the use of breathable (LR) and non-breathable (HR) underlays, with recommendations and figures which illustrate the different ventilation requirements for specific roof types and roof coverings (air permeable and air impermeable).
So, what should builders and roofers do to minimise moisture risk in pitched roofs and reduce their risk of costly call- backs?
- Follow the new BS 5250 guidance at whatever stage you become involved in the roof design and installation. Liaise with other specification and construction stakeholders to ensure the roof design and proposed selection of materials satisfy current Building Regulations and the recommendations of BS 5250.
- Consider the impact of any roofing work on the rest of the building fabric in terms of moisture risk assessment, see table 4 in BS 5250:2021.
- If you are working on a refurbishment project, check the different requirements – e.g., change of use of building, structural changes.
- Also ensure you install the roof covering and its fittings and accessories in line with the latest BS 5534 ‘Slating and tiling for pitched roofs and vertical cladding-Code of practice’ and the BS 8612 ‘Dry-fixed, ridge, hip, and verge systems for slating and tiling – Specification’ Standards, which will ensure the roof is secure against increasingly volatile weather and prevent water ingress.
- As a minimum, get a new fixing specification for every project and ensure it is followed. Marley can also provide full roof system and NBS specification, which will ensure correct ventilation levels via their approved roof underlays and ventilation products.
- Don’t rely on a breathable (LR) underlay as the sole means of ventilation. BS 5250 continues to recommend ventilation of the loft space and sometimes the batten space, and so our recommendation is that roofs will always require some form of supplementary low, high or both, levels of ventilation, regardless of what underlay is used.
- Consult the roof covering manufacturer for their recommended package of materials. Consider using a full roof system from one manufacturer to ensure compatibility of roof components for an efficient, well-ventilated roof.
- For new and existing buildings, increased loft insulation can produce a condensation problem. Take steps to minimise thermal bridging, by using eaves ventilation, a well fitted rafter roll to stop any insulation blocking the ventilation and underlay support trays to maintain clear ventilation routes.
For further information on Marley visit www.marley.co.uk
For more information on the new BS 5250:2021 Standard, visit www.bsigroup.com