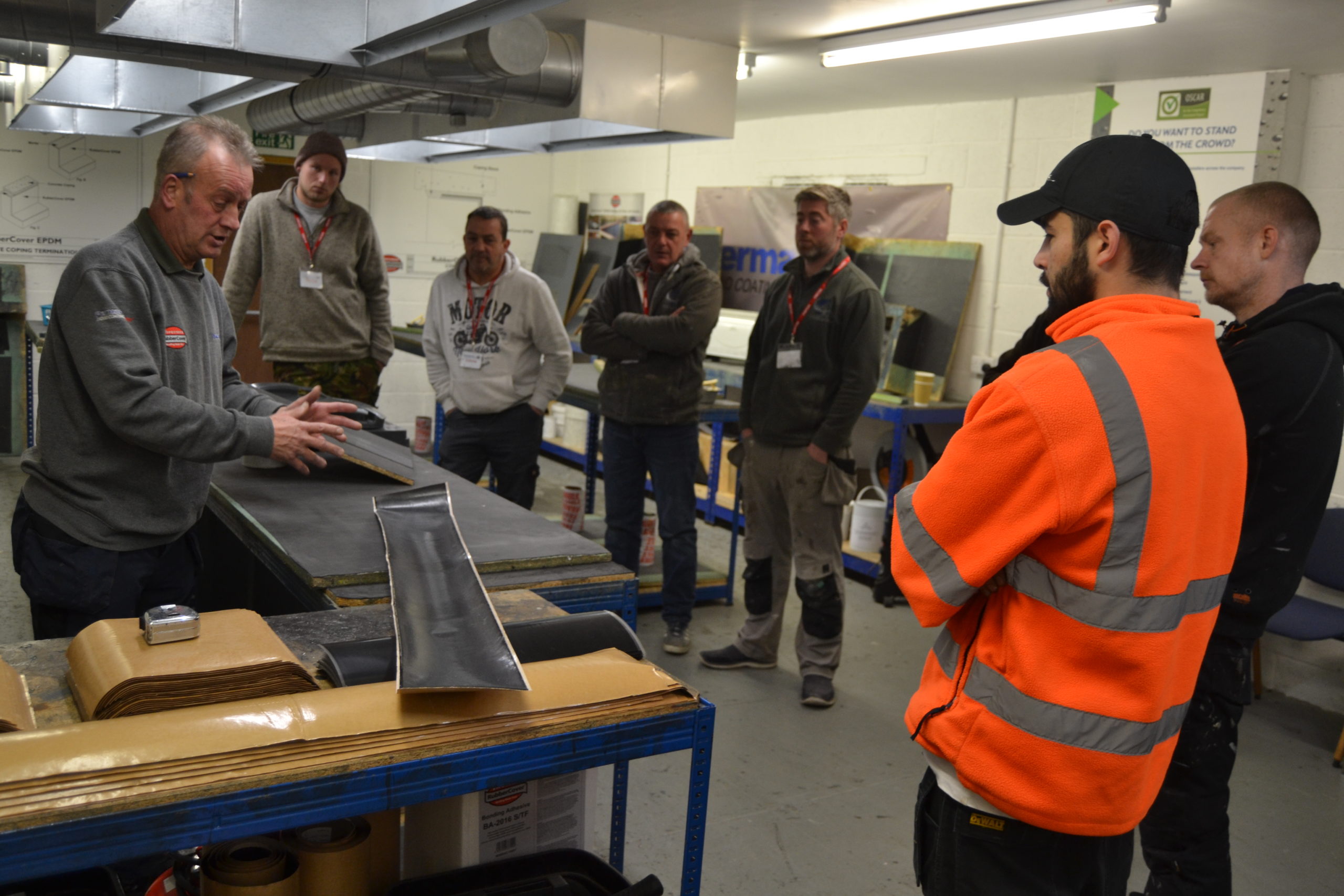
Adrian Buttress, managing director of EPDM rubber roofing specialists Permaroof, and John McMullan, general manager at Firestone Building Products UK & Ireland, discuss what makes rubber roofing so long lasting
EPDM, a product that is manufactured from synthetic rubber compounds and is rolled to different weights under pressure, has a proven track record around the world for longevity, waterproofing and weather-ability in both domestic and commercial situations. When a complete system, which includes a membrane, adhesive, tape, and primer from the same brand is used, contractors can expect the material to withstand the elements for more than 50 years.
Proof of this is already in action; Firestone’s first EPDM installation at Albo Manufacturing in Wisconsin is marking its fortieth year with no reported issues even despite tornadoes, snow, and extreme sun hitting the area over the past four decades. In the UK, both John and Adrian can attest to installations they know have surpassed the 30-year mark.
The history behind EPDM rubber roofing
The Occupational Safety and Health Act (OSHA) became law in the 1970s as well as the Passage of the Clean Air Amendment Act, changing the roofing industry by negatively impacting asphalt which was the commonly used flat roofing material at that time. The Arab oil embargo subsequently drove the price of asphalt up even further and meaning what was available, was often poor quality. This created a sudden and strong demand for an alternative to enter the market.
John comments: “Despite demand being strong and the product proving popular, it was still incredibly difficult to source EPDM and waiting lists were long as a result. At this point, Firestone spotted the opportunity and decided to leverage its knowledge and experience of rubber manufacturing to enter the market, launching its own EPDM rubber roofing product in 1980.”
Why is EPDM so long lasting?
Field testing and proven installations, such as the very first Firestone project in Wisconsin, are behind the expected EPDM lifespan of over 50 years. There are a few reasons for this longevity as Adrian explains:
“Firstly, when looking at alternative flat roofing options, they often degrade due to loss of mechanical properties caused by exposure to UV. Temperature fluctuations: even those that are normal for the changing UK seasons cause stress in materials with low degrees of flexibility and elasticity. This results in cracks and tearing – particularly at any joints or details.
“EPDM rubber roofs, when applied correctly to adequately prepared roof decks, far outperform other types of roofing. As well as the excellent waterproofing, EPDM is resistant to UV radiation as well as ozone and temperature fluctuations which would otherwise age the product significantly. EPDM membranes have elasticity of over 300 per cent to accommodate building movement and extremes in temperature. Furthermore, flexibility and elasticity are retained down to temperatures as low as -45oC.
“EPDM membranes can be manufactured in very large sizes up to 15.25m x 30.5m, meaning many small flat roofs can be installed with a single sheet of membrane. The need for site-fabricated joints is significantly reduced, improving the productivity of the roof waterproofing installation. Furthermore, if the membrane ever becomes damaged – for example, due to vandalism or other mechanical damage – then an effective long-term repair of the EPDM rubber is a simple process.”
John concludes: “Ultimately, these benefits speak for themselves, but it must be remembered that this longevity is only assured by fully trained contractors. A high standard of installation is essential to secure the positive reputation of the wider industry as well as the individual installer and their business. Even the most qualified and experienced roofers should keep on top of continuing professional development (CPD) to enhance their skills in an ever-changing sector and, in turn, help to raise industry standards. CPD is something that Firestone and Permaroof champion as a critical part of their success. Permaroof operate their RubberCover Training Centre and have trained nearly 5,000 people from across the country over the past 16 years.
“The natural characteristics of EPDM – resistance to UV and temperature fluctuations – and how it is supplied – in large sheets with no seams – are the key reasons for its outstanding longevity. While this not only offers an attractive offer to the end-user and therefore the contractor, EPDM represents an eco-friendly waterproofing option. The inert nature of EPDM combined with its long service life results in an extremely low environmental impact. Not only does the manufacturing process take relatively little energy but with the possibility of renovation to extend the service life, and ultimate recyclability, EPDM is a truly green roof waterproofing solution.”
For further information on Permaroof UK visit permaroof.co.uk
For more information on Firestone Building Products visit firestonebpe.co.uk