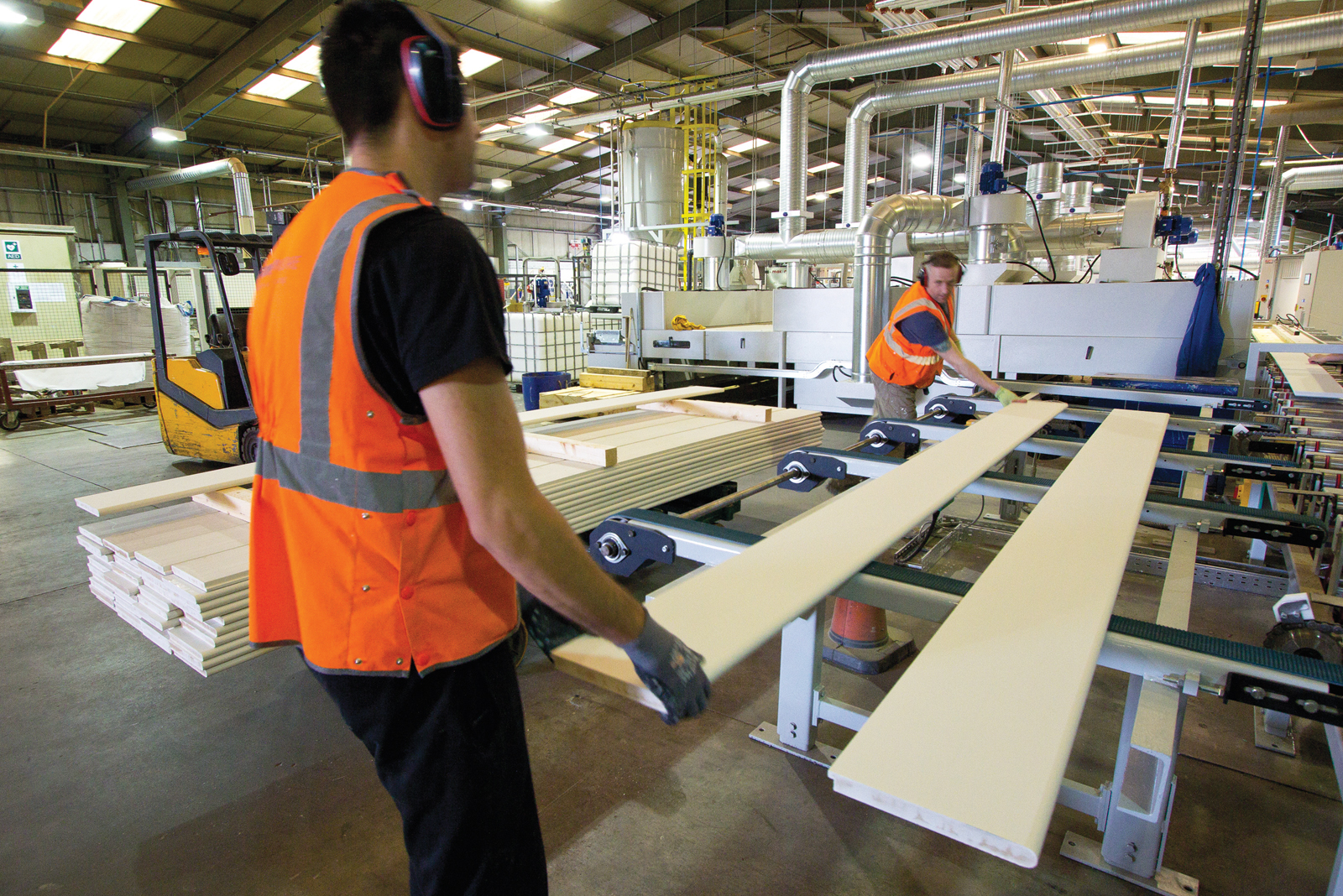
Jake Cintra, National Account Manager at W.Howard, explains how primed and fully finished MDF products can make a builder’s life easier.
The construction sector has seen a massive upsurge in builders choosing materials that are easy to install and require less time on site. Whether it’s for modular building, off-site construction, or simply the need to get traditional buildings constructed and sold as quickly as possible, every builder is under pressure to get projects finished to help meet increasing demand.
Manufacturers, in turn, are looking to create high-tech products that cut down on installation times, often supplied pre-finished to reduce the time that the wet trades need to spend on site.
At W.Howard Group, we have seen a huge uptake in the specification of MDF profiles across the entire industry, ranging from new-build projects with national housebuilders, right through to modular buildings and apartment blocks. MDF is even being specified in renovation projects and for period properties, as it can be supplied in any profile, and is easily painted and finished to match any colour or décor style from Edwardian, to Georgian or Art Deco.
Take door frames and door linings, for example. Once, these products would have been manufactured out of softwood and fitted on site as part of the first fix. Then, during second fix, builders would return to site to sand, prime and paint them as needed. This traditional method is very labour intensive and, with labour costs being the most expensive part of any project build, housebuilders have long been looking for a more cost-effective alternative to minimise the amount of time spent on site and the number of site visits.
Over the past 10 years, there has been a steady move away from traditional softwood door linings, as the sector embraced the convenience of MDF products. Unlike softwood, MDF is a dimensionally stable material that doesn’t warp or bend and comes without the knots and varying grains that are found frequently on natural timbers.
These knots are a feature of softwoods and natural timbers, rather than a defect, but frequently cause problems for builders who try to use them for doorlinings, as they need a clean, straight piece of wood that can be easily painted and finished. The different grains and knots in natural timber can result in a lot of wastage during the creation of a single door set, whereas any part of an MDF profile can be used.
MDF door linings are supplied to site pre-primed, pre-trenched and ready to fit, making it by far the easiest and best option for builders looking for a quality product that still saves time on site. Despite the price increases seen across the MDF sector over the past nine months, MDF has remained the number one choice specifically because it is an easy material to work with, and can be installed quickly.
This stable material is already primed and ready to paint, minimising preparation times and resulting in fewer site visits to apply the finish as the project draws to a close.
Reduce finishing times
Suppliers such as W.Howard Group have taken the time benefits MDF can offer one stage further, by offering a wide range of fully finished, wrapped door linings, door frames and architraves. These profiles can be installed either on site or in a factory setting, and require no painting or finishing on site, increasing the speed of the build.
W.Howard Group’s fully finished profiles are available as veneered, laminate or foil wrapped, so they can match any paint colour or offer the same look and feel as solid timber, depending on the builder’s specification.
The company’s newly launched hardwearing PVC wrap options offer a massive range of wood grains, as well as solid colour options to replicate the top-class paint finish that many homeowners ask for. Profiles can also be supplied finished with modern, printed designs to match melamine or laminate finishes, enabling the doorlinings and architraves to match the style of a high-end fitted kitchen or bathroom furniture, for example.
Also available for use in high-traffic buildings such as hospitals, schools or retail units, for example, are tough, impact-resistant laminate finishes, as well as a range of fully lacquered veneers such as oak and walnut, and to match designer veneers like Tabu and Alpi. Together, these fully finished profiles offer a quick-fit solution for almost any domestic or commercial building.
W.Howard Group is a leading UK supplier of quality MDF profiles, including skirtings, architraves, window boards, door linings and bespoke products. We have one of the largest profile product ranges in Europe, with more than 200 profiles and sizes. Our customers comprise of builders’ merchants and specialist trade manufacturers.
For more information on W.Howard’s product range, visit https://whoward.eu/