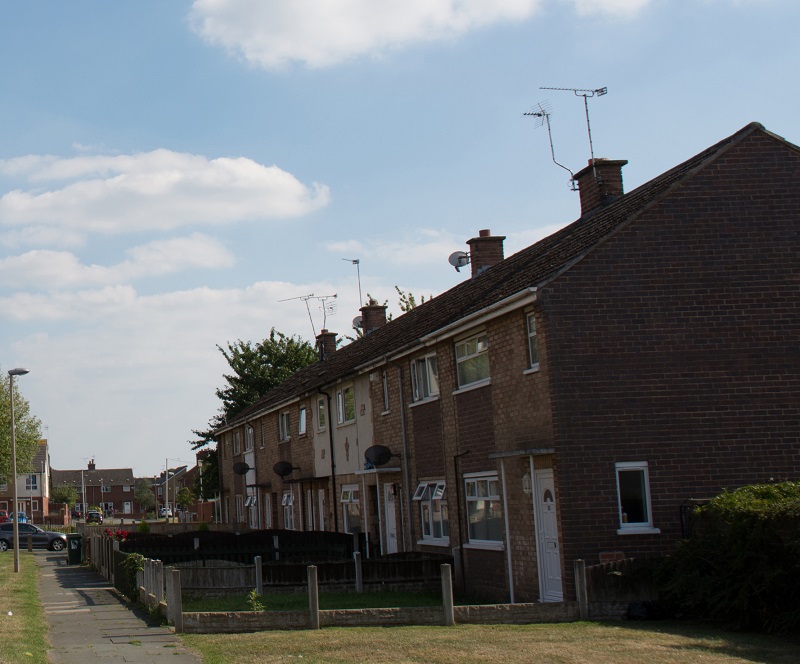
In the fourth and final instalment of our series, Hudson Lambert of Safeguard looks at houses built from 1960s onwards to about 1980.
The 1960s were obviously a time of great social change – indeed revolution. The period was one of flux as musical, political, sexual and economic behaviours went through epochal shifts.
Unhappily for us, sections of housebuilding were subject to the same hippy-trippy upheavals as the mop-topped loons haunting Carnaby Street – with local authorities throwing up large numbers of brutalist blocks which, even if well designed, were often poorly built, ‘slums in the skies’.

This in part triggered the rationalisation of local building by-laws into what we know now as the Building Regulations – first in Scotland in 1964, then England and Wales in 1965.
They were a timely introduction as, beyond the ‘technology’ failure of non-traditional housing, the volume of building was just phenomenal: 425,000 new dwellings in 1968 alone!
Tower blocks aside, traditional housebuilding again evolved from that of the post-war types. Cavity walls were standard, yet now with blockwork, rather than brick, as the inner.
While wall ties were generally galvanized against corrosion since 1945, it is now estimated that nearly all installed prior to 1981 are at risk of failure.
This is because of a gross underestimate of the life expectancy of the coating – notionally thought to be around 60 years, the BRE asserted in 1979 that it was significantly less than this. In 1981, the British Standard (BS 1243) was amended to triple the coating thickness.
Floor detailing changed too and, while less susceptible to damp than some of its predecessors, is still at some risk from damp.
Cavity walls
As has been said many times in this series before, cavity walls were introduced primarily as a means of defending homes from penetrating damp caused by heavy rainfall. The thermal performance benefits of cavity walls, though, are hard to establish and cavity wall insulation (CWI) has been widely installed to improve it.
CWI itself is a very effective means of improving energy efficiency of walls, yet to be effective and not cause other problems, external walls need to be in good order – without cracks or mortar losses – prior to installation.
Where it has become wet through damp penetrating cracks or poor pointing, it can be saved – if it hasn’t failed completely – by re-pointing and crack-stitching, then applying a masonry protection cream, such as Stormdry, to the exterior brickwork.
This allows the wall to breathe and the CWI to dry out, albeit slowly, while preventing further moisture ingress.
Masonry cracking
The 1960s saw two main popular window styles fitted – single-glazed timber casement, or horizontal sliding aluminium (although it could be noted here that PVCu windows put in their first appearance in the UK in around 1965.
As in previous eras, cracking is often a result of window replacement – wildly popular in the 80s and 90s – and caused by over-sized and unsupported apertures, missing lintels and inferior materials.
Where steel windows had been installed at the time of build, lintels are also often missing as the perception was that they would not be necessary.
In this context, once the window and/ or opening has been reinforced, a crack-stitching system – such as BrickFix – can be used to fix cracks and reinforce mortar beds. Brickfix Helical Bars can also be used to create a replacement lintel, with each bar effectively forming the corner of a virtual lintel.
Floor construction
Concrete strip footings – as first seen pre-war – remained in use, and the ground behind them dug out and infilled with hardcore.
A damp-proof membrane (DPM), seen for the first time in housebuilding instead of asphalt, was then laid on top of the hardcore and it is onto this that concrete floor slabs were poured.
So far so good, yet without a sand barrier – not commonly in use until the Noughties – on top of the hardcore, these DPMs are prone to puncturing and failure.
After that, it is in the sixties that we then see screeds poured onto floor slabs, and then the final floor layer – often herringbone parquet, as in the 40s and 50s – laid.
Where the DPM has failed, it is probably not practical to excavate the floor back to it. However, it is possible to dig out the screed layer, back to the floor slab, and brush apply a new DPM – such as Safeguard’s Drybase Liquid Applied DPM.
The DPM is a liquid, polymer-based barrier coating that can be used to resist penetration of water, gases – such as methane and Radon – salts and other liquids through masonry, stone and concrete. The screed can then be re-poured, and the floor re-laid.
In modern houses, which may be expected to be more ‘reliable’ in the context of damp, the main awareness needs to be about not creating problems through new works.
Consequently, care needs to be be taken to avoid compromising ventilation in walls and floors by not blocking airbricks etc; ensuring window openings are structurally sound and reinforced where necessary; (PVCu) In addition, window frames themselves should be properly reinforced, and, most importantly, DPCs should not be bridged by raising external levels over them.
For further information on Safeguard Europe click here.