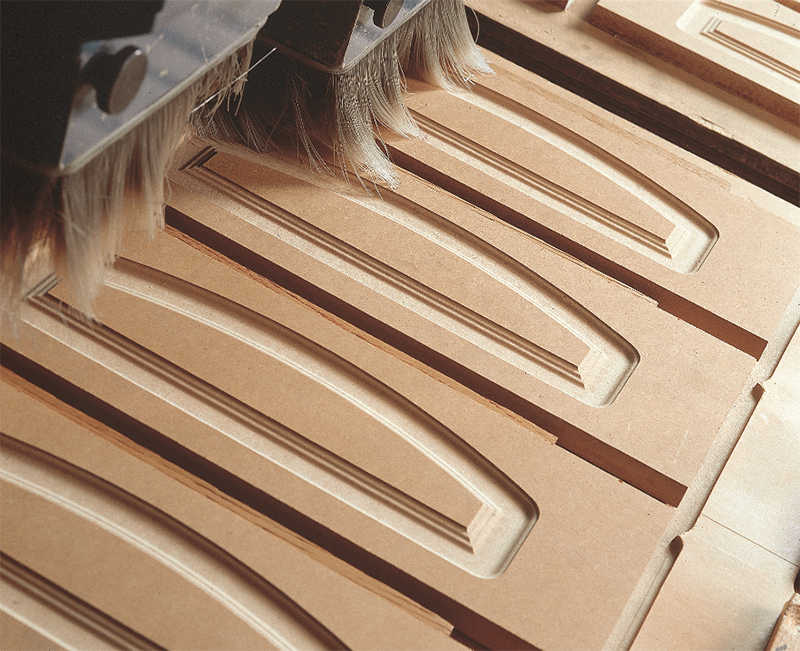
A handy guide to CaberWood MDF installation.
CaberWood MDF has a consistent density and a smooth surface that is ideal for machining, profiling, painting, or the application of paper foils and veneers. In many respects, the material can be treated as a high quality timber; without the inherent defects of knots and grains.
Machining
As a homogeneous wood fibre material, it is ideally suited to modern machine tooling. It can be worked easily with all conventional woodworking machines and hand tools; it saws cleanly and drills easily and shapes and routs exceptionally well without splintering or chipping.
Profiling
Profiled edges require no edge banding or lipping. Sculptured or textured effects can be machined or embossed, and narrow or small door frames can be produced from a single piece of board. A major advantage is the relative ease of finishing perpendicular and moulded edges without the need for elaborate filling or the application of adhesive bonded edging materials. This characteristic derives from its uniform density of and the absence of core voids, which would require filling.
Sanding
Sanding after moulding or routing produces a much smoother finish. The moulded edges can be sanded with any number of different profile sanders. Various polyurethane based abrasive wheels are available to fit to spindle moulders or in line with a double end tenoner. These wheels can be shaped to the cutter profile using an abrasive paper glued to the desired edge profile. 80/100 grit should be used for the removal of cutter marks. 120/150 grit is usually used for finish sanding with finer grades available, if required.
Sawing
Saw blades and tools should have increased clearance angles to reduce resin build up and reduce the life between sharpening.
Follow these tips to ensure best results, minimum breakout and a longer tool life:
- Tungsten carbide saws are recommended for general use
- Saw blades should have higher clearance angles and increased tool angles compared with normal wood-working saws
- Clearance angles should be maintained when the saw is serviced. Reduced angles will increase the amount of resin build up. Increased angles will reduce the life between sharpening
- Chipload – which is the thickness of chip cut by each tooth – should be
in the range of 0.15 to 0.25mm. The feed rate required to produce this
is calculated as follows- Feed rate (mm/min) = Chipload x r.p.m. x no. of teeth
Norbord has produced a whole range of video guides for its products. To view these visit norbord.co.uk/resources/help-advice/video-guides/