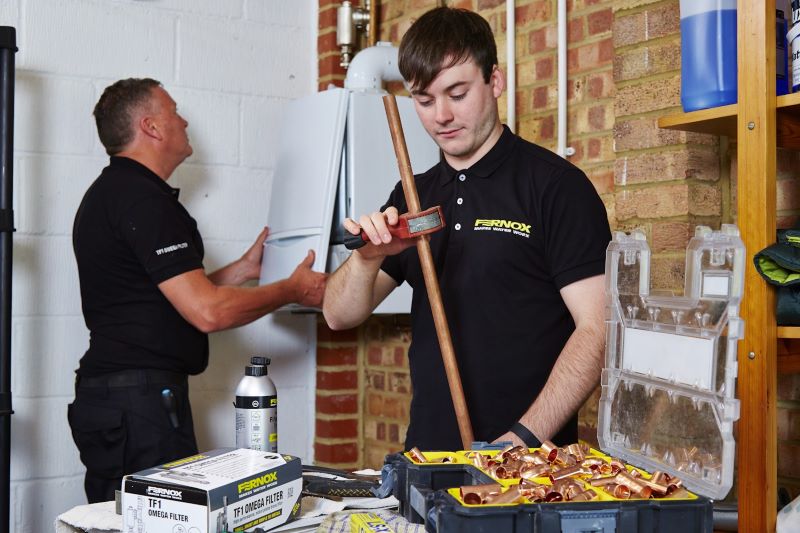
Richard Crisp, Head of Chemistry at Fernox, looks at the importance of ensuring high quality system water
Contamination in the heating system can significantly impact the efficiency, performance and lifespan of the boiler and other key system components. It can be caused by iron oxide sludge caused by the corrosion of steel in the system as well as other metal oxide debris from non-ferrous metals (e.g. copper, brass, aluminium). These contaminants block heating pipes and prevent radiators warming up correctly, causing far more energy to be used. In addition, aluminium components are vulnerable to pitting, which leads to pressure loss and ultimately system failure.
Limescale, especially in hard water areas, forms on surfaces within the system, including vital components such as the heat exchanger and pump. British Water estimates that just a 1.6 mm coating of limescale on a heating element can reduce boiler efficiency by up to 12%.
Efficiency and longevity
Since June 2022, the BS 7593:2019 British Standard for the installation, commissioning and maintenance of domestic heating systems forms part of the legal requirements of Part L of the Building Regulations in England. This means that all new homes, or new heating installations in existing properties, must comply with this guidance.
Part L now requires the system to be cleaned fully, dosed with a high-quality inhibitor to prevent the formation of sludge and limescale, and the boiler further protected from circulating debris with an inline system filter. This must then be maintained with regular servicing and maintenance, including tests of the system water to check inhibitor levels.
Cleaning
A high-quality chemical cleaning solution will effectively remove sludge, scale and debris. For heavily contaminated installations, it may also be advisable to carry out a powerflush to ensure the system is cleaned thoroughly. New systems should also be cleaned as part of the mandatory Part L prescribed commissioning process to remove any installation debris and other contaminants.
Guard and Protect
Once cleaned, dosing the system with a high-quality inhibitor will prevent the formation of sludge and limescale build up by chemically protecting metal surfaces. Some inhibitors, such as Fernox Protector F1, feature enhanced pH buffering to ensure the pH level remains between 6.5 and 8.5, which is the optimum range to prevent corrosion in mixed metal systems.
An inline system filter should also be fitted – and this is now a mandatory requirement of Part L of the Building Regulations for England. An inline filter will protect and guard the boiler and heating system by capturing sludge and debris for simple removal. Choosing a high quality filter that is designed to capture both metallic and non-metallic debris will ensure more effective protection of the system. This will help deliver both improved energy performance and system longevity. For example, the Fernox TF1 Sigma Filter and TF1 Omega Filter achieve this with a unique combination of a powerful neodymium magnet and Hydronic Particle Separation (HPS) technology.
In addition, for systems with a lower flow temperature, such as those with a heat pump, microbiological protection is also required. At these temperatures, typically between 35°C 55°C, microorganisms such as bacteria and fungi will thrive. This not only poses a health risk but can also cause accelerated degradation through Microbiologically Influenced Corrosion (MIC) and reductions in system performance due to the formation of biofilms. On these lower temperature systems, a biocide should be added to the heating system water. The biocide will kill the microbes by altering the cell wall permeability and interfering with biological processes.
Maintenance
A heating system should be serviced and maintained at least every 12 months, to ensure it remains contaminant free and continues to function as efficiently as possible. This should include cleaning of the filter to remove the captured sludge and debris as well as a check of the inhibitor levels using an on-site test, which is required by Part L. The Fernox Express Inhibitor Test, for example, provides a quick and easy method of checking the concentrations whilst on site, with a simple dip test on a sample of the water. If the levels are not sufficient, inhibitor can be added, and the system retested to check the concentration with no return visit needed.
In addition, every five years the system should be either re-dosed with inhibitor or a full laboratory analysis of the system water conducted. This can be completed relatively simply with test kits such as the Fernox Water Quality Test. Installers simply collect a sample of the system water and send it to the laboratory for a full analysis and report of key system water parameters. With the Fernox kit, results are returned within 48 hours and all samples and results can be managed through an intuitive mobile app.
For further information about Fernox and its range of products, click here.