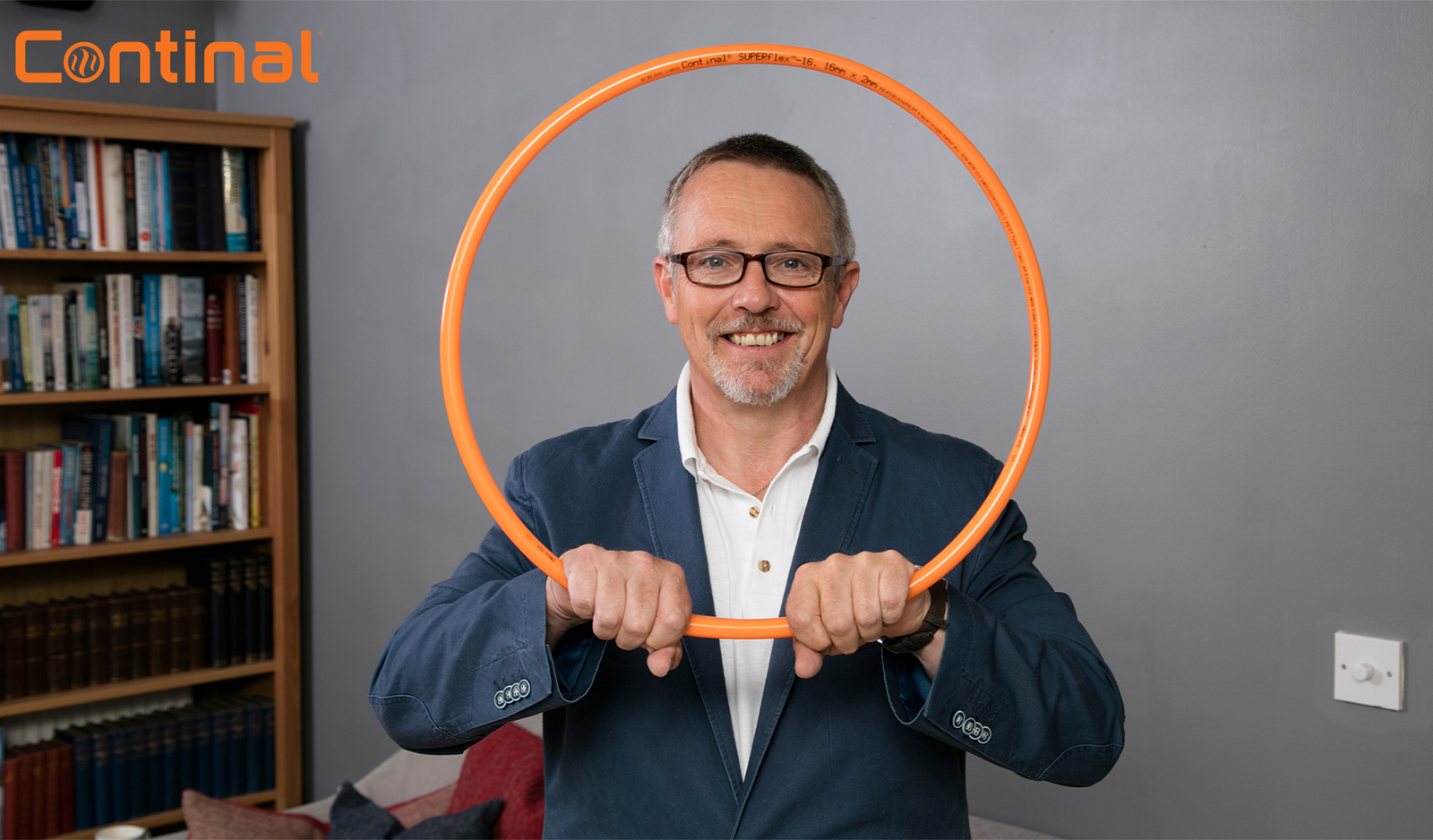
Chris Ingram, founder of Continal Underfloor Heating – and nine-times Chairman of the UK underfloor heating trade association – offers some top tips to ensure a problem-free underfloor heating installation in extension and conversion projects.
Underfloor heating (UFH) can be fitted as part of any conversion or extension, whether that is as part of a conservatory, or combined with an existing radiator system as part of the wider renovation of an older building.
During my 20 years in the heating industry, fitting UFH in renovation projects is probably the area I’ve heard the most problems about, usually as the result of poor advice from a manufacturer, poor system choice, or a failure to adequately insulate the system – or all three.
In fact, fitting UFH in a conversion or extension can be pretty straightforward, provided you do your research before you choose the system, and you make sure the system is designed correctly to suit the building.
Not all UFH systems are the same, and they should never be sold as a one-size-fits-all product. Overfloor systems will suit certain types of property better than joisted or solid floor systems, for example, and once you have that knowledge and understand how to specify a system properly, it is easy to avoid a lot of the common design pitfalls.
Know your building
Fitting UFH in a renovation project can actually be easier than a new build, because so many of the decisions have already been made for you. You know how the existing building has been constructed, and the heat source is usually already in situ, which gives you a lot of the information you need to design your system.
A 15th Century barn renovation, for example, will likely have solid floors and little insulation, unless it has been added during previous works, and so you would install a different type of UFH system there than if you are simply adding a conservatory or single-storey extension onto the back of a 1950s property.
Whether your building has a heat pump or a gas boiler will also tell you a lot about the type of pipe spacing and flow temperatures you need, as will whether the conversion includes a kitchen, bathroom, or merely additional living space.
There are, of course, areas where fitting UFH in a renovation is harder than a new build. You are more likely to find issues coming up around matching floor heights between the old and new property, and there are additional issues to consider if you’re adding UFH to an existing heating circuit or radiator system. This is where it’s best to seek advice from a trusted, reputable manufacturer, such as Continal, who can help you iron out all these potential pitfalls at the design stage.
Pipe layouts
A lot of myths have started circulating in recent years about the best pipe layouts for a UFH system. One of these – that pipes must always be spaced at 150mm or 100mm regardless of the build or flow temperature – is utter nonsense, but it does sell a lot of pipe.
In a typical CAD plan, the pipework runs around in what is called a snail pattern. Many people believe this prevents hot and cold spots, but in a modern, well-insulated home, the temperature difference across the floor in even the largest room would be just a quarter of a degree at the surface – the occupants simply won’t feel it. Instead, a straight back-and-forth laying pattern works perfectly in almost all situations and is much easier to install, though you may need to run the pipes closer together by the windows, to ensure a higher heat output.
You may also need to close up the pipe spacing if you’re working in a bathroom or en-suite, as the baths and showers reduce the available floor area. The closer the pipe spacing, the higher the heat output, though be aware that closer spacing also means you’ll use more pipe, and so may need a bigger manifold.
Snail patterns may still be the better choice if you’re working in an older property with very high heat losses – seek advice from a reputable manufacturer.
People often ask what type of heat emitter is most efficient. There’s a simple rule of thumb – electric UFH is 30 per cent less efficient than radiators, while warm water UFH is 30 per cent more efficient than radiators.
There is still a place for electric UFH, however, particularly if you’re working on a small, isolated area like a kitchen or a bathroom. Unless your WC or en-suite is unusually large, however, you can simply run the UFH off the adjoining bedroom.
Insulation
Regardless of the system you choose, you must fit enough insulation, otherwise you’ll lose too much heat into the ground, and end up just paying to heat the worms.
Beware those salespeople who we know are telling builders that the insulation that comes as part of an overfloor system panel is sufficient – it isn’t. You need to add at least 50mm of insulation below the pipe system, and possibly more depending on the type of insulation itself. If in doubt, ask your manufacturer or consider contacting Building Control, as they will be able to offer advice.
Continal has been one of the UK’s leading design and supply specialists for energy-efficient warm-water UFH for 20 years. The company’s full range of UFH systems for solid floors, overfloor applications and joist floors, as well as a full portfolio of controls and accessories, can be found at https://www.ufh.co.uk/