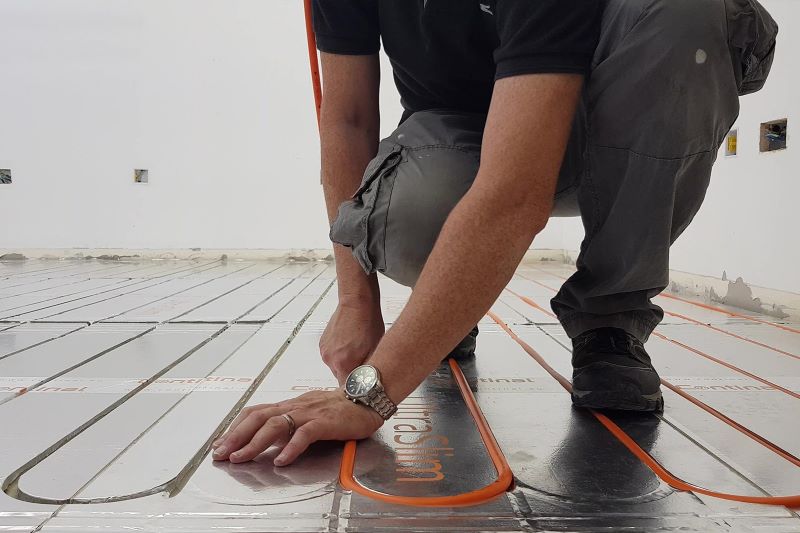
Building Regulation requirements for heating systems have changed, bringing low-flow temperatures to the mainstream. Chris Ingram, Founder of Continal Underfloor Heating, explains why this will inevitably lead to more underfloor heating systems being installed.
Just 12 months ago the Government introduced its latest update to Building Regulation Part L, bringing with it one of the most far-reaching changes to heating systems we have seen since condensing boilers were made mandatory back in 2005.
This latest change to Part L was introduced to help drive the modernisation of the UK’s housing stock, requiring a 31% reduction in the carbon emissions of newbuild properties. This means a maximum flow temperature of 55°C for all new heating systems in England and Wales – a significant reduction from the 80°C flow temperatures that you are likely used to working with.
Low flow temperature heating systems were brought in as a step towards the introduction of the Future Homes and Building Standard which, in 2025, is expected to require carbon dioxide (CO2) emissions produced by new homes to be around 75 to 80% lower than current levels, as well as potentially banning the use of gas boilers in newbuild properties.
What does this mean for builders?
These Part L changes present a challenge for those builders used to installing more traditional radiator-led systems, and who may lack the resources to thoroughly investigate all the available alternatives, such as underfloor heating (UFH). That’s why Continal has a dedicated team of experts available to help explain all the options that now exist, to ensure that the right solution can be achieved both for the builder and their customer.
We regularly talk our customers through how to make sure they are compliant with the new regulations, as well as how to choose an appropriate UFH system for the building that will also work with the end-user’s budgetary constraints. For more complex floor solutions that may require acoustic insulation or fire protection, for example, we can provide a complete specification package that meets all these requirements, making the specification and installation of the heating system simple and straightforward.
Although these regulations have already been in place for a year, it’s possible that you haven’t yet needed to design a low-temperature heating system, since the Government said these requirements would not apply to any development that had begun construction before June 2023. And the Part L changes don’t yet cover systems in existing buildings, unless the entire heating system is being ripped out and replaced. But now we have reached that 12-month deadline, you are likely to start encountering these low-temperature systems more often and so it’s important to fully understand how they work, and why they’re different from what you may be used to.
Low flow temperature systems need larger heat emitters with a much greater surface area to provide the heat outputs people are used to enjoying from 80°C flow temperatures. This makes it more challenging to use radiators as heat emitters without having to fit additional or larger radiators in each room.
Alternatively, when you combine a gas boiler with UFH you are turning the entire floor of a property into a giant heat emitter, creating a more efficient, low-temperature system and maximising the living space inside the home since there is no need for radiators.
UFH has been installed in UK homes for decades. It is a proven heating technology that homeowners have embraced thanks to its luxurious comfort, warmth and efficiency. UFH is also significantly more efficient than radiator-led systems, giving customers much-needed savings on energy bills with the cost of living currently so high.
At Continal Underfloor Heating we’re used to designing low-flow temperature systems that work with a wide range of fuel sources including gas boilers, heat pumps and solar panels. This means you can install UFH in a property with a gas boiler today and be helping to futureproof the property from whatever fuel source ultimately replaces gas boilers after they are banned from use over the coming years.
Get the most efficient system
To make UFH systems as efficient as possible, builders must consider every aspect of a property before finalising the design. UFH systems can work with any type of building, floor construction and covering, but it’s important to consider the heating right from the start of the building project and to develop the system in conjunction with the design of the building itself, to ensure the homeowner will receive the warmth, comfort and cost savings they are looking for.
This includes considering the fuel source being used, the controls, the floor area, the property’s insulation levels and the fabric of the building itself. Low-temperature systems also generally need narrower pipe spacings to achieve the desired heat outputs. Even the finished floor coverings will have an effect, since different materials such as wood, vinyl or carpet will have an impact on the heat transfer levels through the floors and into the room above.
If you are in any doubt about how to create an efficient UFH system, always seek advice from a trusted manufacturer. Continal supplies every different kind of UFH solution, so we will always offer completely unbiased advice. We also provide full CAD designs for every type of property and system, and can liaise directly with tradespeople on site at any stage of a project.
Continal has been one of the UK’s leading design and supply specialists for energy-efficient warm-water UFH for more than 20 years. The company’s full range of UFH systems for solid floors, overfloor applications and joisted floors, as well as a full portfolio of controls, accessories and resources for developers and architects, can be found online at www.continal.co.uk