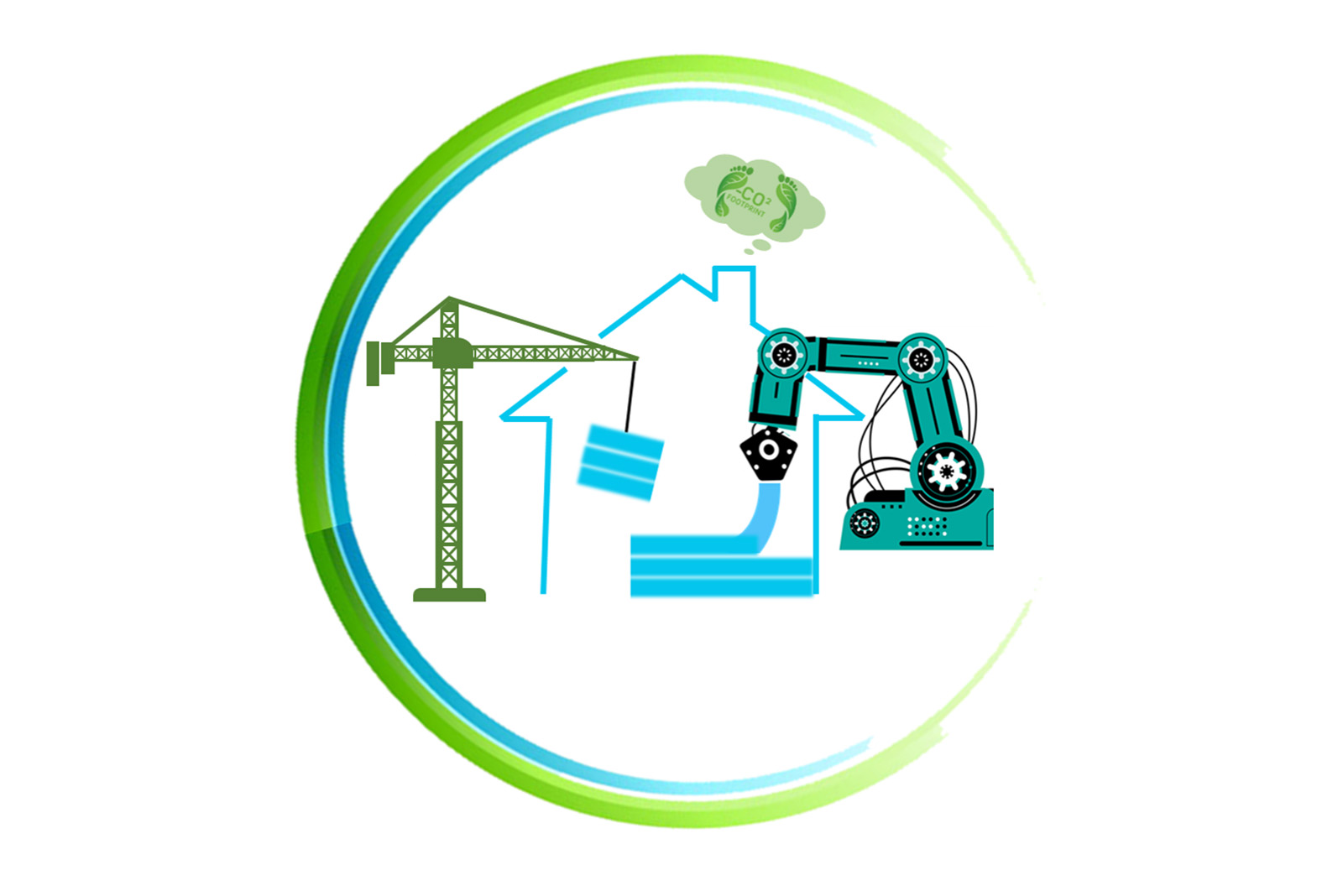
In the first of a three-part series, Professional Builder explores some of the advances that are being made in materials and what tradespeople could be routinely using on site in the future.
There has in the past been a perception with some environmentally friendly building products that there is an inevitable trade off with performance. Whether it’s in paints, plasters or masonry materials, reduce CO2 and pollution they may well do but they’re never quite up to the mark of their predecessors. Funded by the European Commission, Brunel University’s three-year DigiMat project has ambitions to change all that with a ‘lego-style’ brick that champions recycled raw materials, and is 3D printed into interlocking blocks that eliminate the need for mortar on site. Not only that, but in many crucial respects its developers have improved upon the properties of what they are seeking to replace.
In his research, project lead, Dr Seyed Ghaffar is utilising his materials science expertise and combing it with innovative manufacturing technologies. It is that synthesis which allows the transition from theory and the lab right through to the factory floor and finished product. “Any technology needs a suitable material if it is to become useful, and vice versa,” explains the Associate Professor in the department of Civil & Environmental Engineering at Brunel University London. “By bringing together waste material with 3D printing techniques we’re hoping to introduce an alternative to traditional brick that is not only more sustainable but is actually an upgrade on the cement and sand-based products currently available.”

The cement constituent of concrete is extremely energy intensive, and a major contributor to global CO2 emissions. Seyed and his team have replaced ordinary Portland cement, with recycled by-products from industry by-products. Fly ash is a waste product from coal-fired power stations, for example, whilst steel foundries are the source for Ground Granulated Blast-furnace Slag (GGBS). “Both of these materials have cementitious properties, and can be used as a binder, but are comparatively weak when set against Portland cement. What we have done is introduced chemical agents which act as an accelerants and/or activator. Essentially, the mix we have perfected speeds up the hydration process, which means the concrete dries quicker and can achieve an even higher technical specification than Portland cement.”
The negative environmental impact of Portland is, therefore, eliminated but in a higher strength concrete with significantly improved sustainability credentials, but the ambitions don’t stop there. “We want to be making use of secondary raw materials wherever possible,” continues Seyed. “Rather than using river sand for the bricks, for instance, our goal is to replace as much of that virgin material with recovered demolition waste. As a result, we’ve been able to reduce the amount of sand used compared to a conventional brick by up to 30 per cent. Moreover, in non-structural load bearing applications it may well be possible to eliminate the use of river sand in concrete completely.”
There is, in fact, three waste streams used in the finished brick. Firstly, crushed concrete is utilised as an aggregate, the second is the aforementioned fly ash and GGBS and, thirdly, further reinforcing agents – sourced from both the plastics and agricultural sectors – are introduced. Concrete is a material that has built much of the modern world and its benefits are many, varied and well known, but like any building material it has limits. As an illustration, it scores highly in compressive strength but exhibits relatively poor levels of tensile strength – in other words, it’s difficult to squash but it can be pulled apart, which makes that third waste source a crucial component of the developed building blocks by Seyed and his research group. Here, wheat straw and plastic waste is added in very small amounts, introducing a fibrous element which increases the product’s tensile properties.
Those components come together in a 3D printing process that Seyed believes could transform the industry by improving productivity levels and reducing energy usage. “It’s something that sounds very futuristic but essentially you’re talking about a computer-controlled hopper and a nozzle with the right mix of ingredients extruded from it. The beauty of that method is that complex geometries can be achieved relatively easily. If you’re utilising a material that has been chemically modified to set quickly, there’s no need for complex moulds or formwork. That’s what we’ve achieved and how the material science comes together with the manufacturing technique.”
“It’s been a process of trialling different additives to determine how we could actually improve on Portland cement,” concludes Seyed, “and there is still much work to be done but we believe it has the potential to provide a clean and affordable solution.”
For further information on civil engineering at Brunel visit https://www.brunel.ac.uk/people/seyed-ghaffar