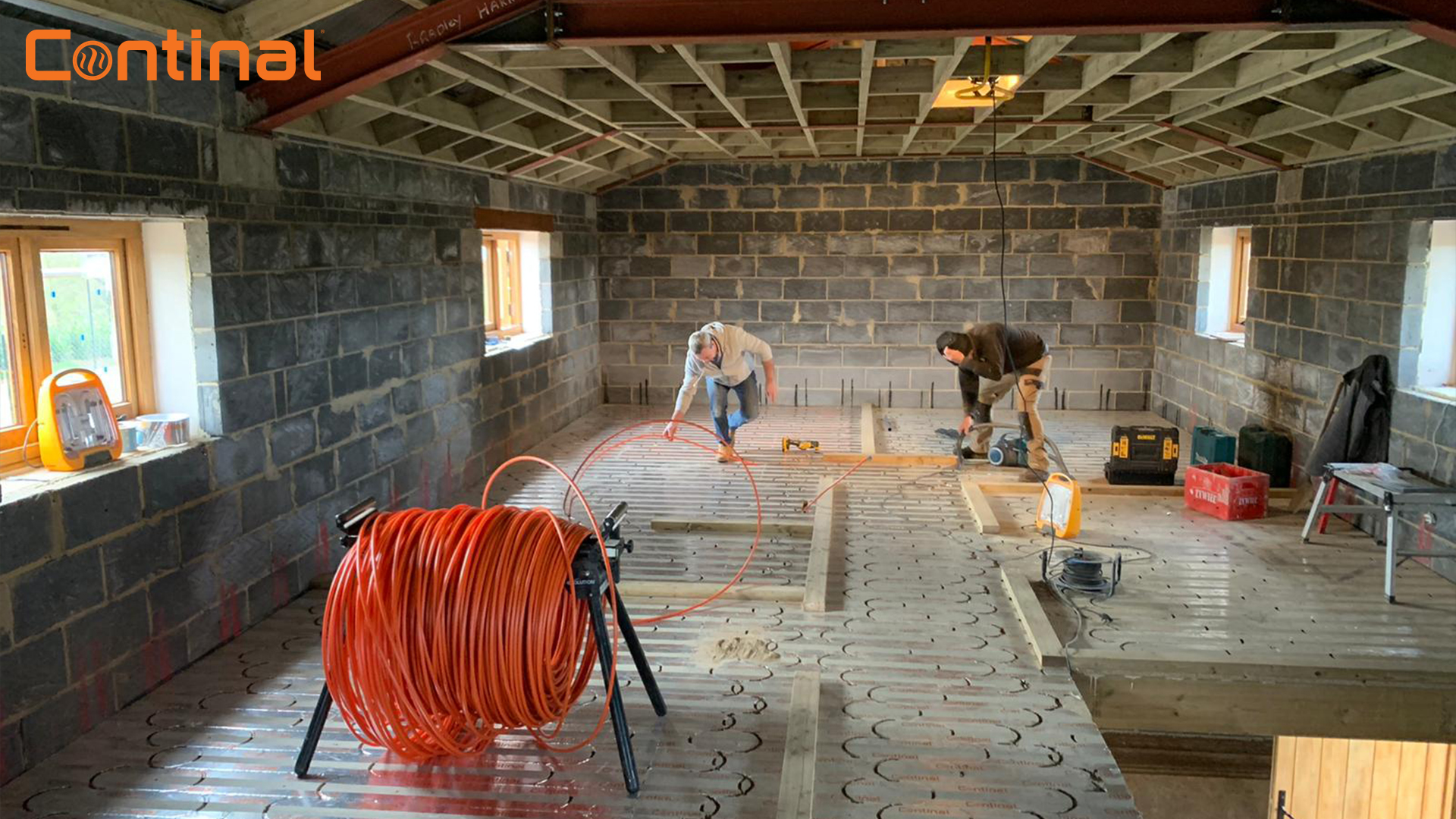
Chris Ingram, founder of Continal Underfloor Heating, offers some top tips on how builders can use underfloor heating in any home extension.
The current ‘race for space’ in our homes is fuelling the private RMI market as people look for ingenious ways to add much-needed space to their homes. Whether homeowners need permanent office space for their new hybrid working lives, or want extra living rooms or bedrooms as their families grow, they are increasingly turning to skilled and experienced builders to help them find the most creative ways to improve their properties.
Many people think extending a heating system will be a challenging process, but it doesn’t have to be, and modern underfloor heating (UFH) systems are making it easier than ever before. UFH is one of the most efficient heating system types on the market, which is more important than ever given the extremely high costs of gas and electricity. UFH also provides comfortable heat through the extension without heat emitters taking up valuable wall space. The importance of this benefit cannot be overestimated, considering the extension is being built specifically to maximise every inch of space in your customer’s home!
You may have been asked to add UFH to a ground floor extension at the rear of a property, or you might be going up into the loft and need to combine UFH with an existing radiator system – either way, with proper planning and the right technical support, fitting UFH as part of your renovation project can be quick and easy.
Do your research
UFH is not a one-size-fits-all solution, so you can’t buy the same product for every project you work on. Overfloor systems will be better suited for projects where there is an existing subfloor that needs to be covered with UFH, such as on a first-floor extension, whereas solid floor systems are usually installed on ground floors when a new screed floor is being laid.
The single most important thing you can do before you begin an extension project is to make sure you understand the building you’re working on. Is there insulation in the walls and floors already? Does the existing heating system run on a boiler or heat pump? Does the homeowner plan to switch to a low-temperature heating system in future? The answers to all these questions will affect the building’s heat losses and will help determine which type of UFH system is best for you to use, and which pipe spacings will give your customers the most efficient results.
How do you lay your pipe?
Another important consideration is the type of living space being created, and how much of the floor area is available for use as a heat emitter. A ground-floor kitchen extension that has a large island in the middle of the room may need a different UFH pipe layout than a ground-floor conservatory, or a first-floor extension that adds a new bathroom.
The simplest layout for pipes in a modern, well-insulated home is a straight, back-and-forth pattern from one side of the floor area to the other. Some tradespeople prefer a snail pattern, and these work well in certain buildings, but a straight pattern is almost always easier to install, and will provide solid heat transfers and great efficiencies.
If you are laying UFH by external windows or next to large expanses of glass you may wish to close up the pipe spacings to provide a higher heat output – much of this depends on the type of glass and what the expected heat losses are. When building a bathroom or en-suite you may need to lay the pipes closer together to achieve the desired heat outputs, because you won’t be laying any pipe beneath baths or showers in the room, reducing the available floor area.
But remember that if you’re using closer pipe spacings across a large floor area you’ll be laying more pipe, so you might need to consider fitting a bigger manifold. If you’re unsure, contact your UFH manufacturer, who should have technical advisers who can help you create the best design – or even do it for you.
Check floor and ceiling heights
One of the biggest things that will determine the type of UFH system you choose concerns the floor and ceiling heights. If you’re extending a property then you may find a mismatch between the floor height of the existing building and the new extension. Alternatively, if you’re building a loft extension, you need to check the roof height (particularly around the stairs) and consider whether an ultra-slim system such as Continal’s OneBoard® structural panel will give you those precious extra inches of headroom that could make all the difference to the finished product.
Our OneBoard® composite chipboard panel can be installed directly onto timber joists without the need for a sub-base, replacing the normal chipboard or plywood layer and helping to reduce floor build-up heights. Even taking into account the required coverboard, by using OneBoard® your floor depth will increase by just 6mm. Pipe channels are pre-routed into the panel at 150mm centres so that pipes can be laid quickly and easily.
If you’re in any doubt over which system to choose, or you would like help designing the most efficient pipe layout for your project, it’s always best to seek advice from a trusted manufacturer such as Continal Underfloor Heating. Our expert Technical Sales Advisers are always on hand at every stage of a project, and we can provide full CAD designs as standard, with technical support whenever you need it. And, because Continal sells a full range of solid, suspended and overfloor system solutions, we can always provide you with exactly what you need, no matter how complex your project may be.
Continal has been one of the UK’s leading design and supply specialists for energy-efficient warm-water UFH for more than 20 years. The company has a full range of UFH systems, as well as a full portfolio of controls and accessories.
For more information on Continal visit https://www.continal.co.uk/