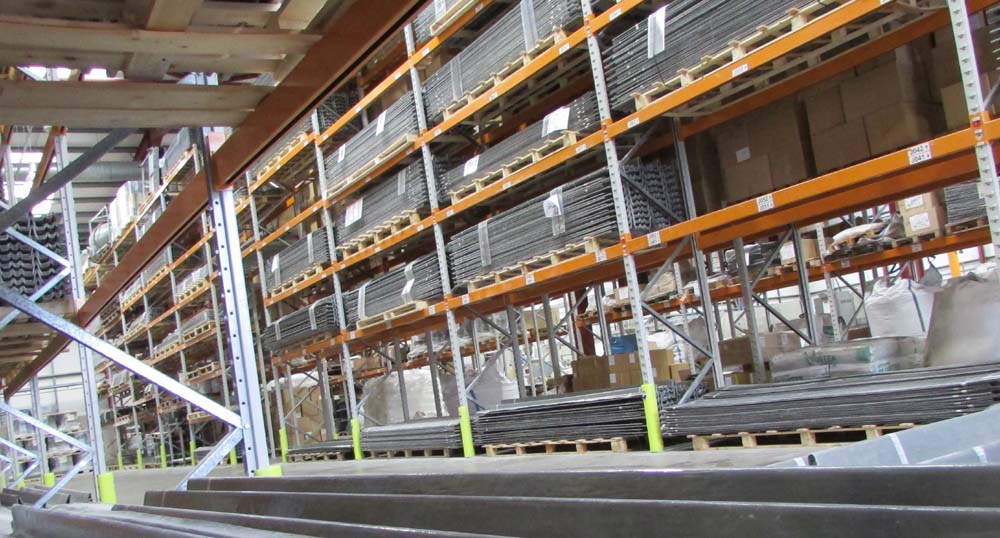
Professional Builder travels to Daventry to hear about the latest chapter in the page-turning story of the Hambleside Danelaw Group.
“You could write a book about this,” we enthused, on hearing the remarkable and fascinating forty year plus history of the Hambleside Danelaw Group.
“Funny you should say that,” replied MD Chris Avery as he handed us a glossy hardback of 80 plus pages crammed full of people, places and products which have all played a part in taking a humble publishing company formed in Nigeria across three continents. Goods as diverse as magazines, china mugs, tea caddies, wallets, handbags and glass fibre roofing components have rolled off its production lines.
The early pages of “From Out of Africa” give a tantalising insight into the trials and tribulations of establishing a business in newly independent Nigeria in the early sixties. Instrumental were four founding fathers, one of which, David Yellop, is still heavily associated with the current business, stretching every sinew of their entrepreneurial spirit to establish the ultimately highly successful EDCON publishing business.
However, it was in 1973 that the iconic brand name, now so familiar with the UK building industry, was first established following a meeting of the principal directors in a hotel in Winchester. Looking for a new and more encompassing company name, they hit upon the nearby Hamble river.
That trickle of a concept soon became a flow in 1975 when the partners were offered an investment opportunity in a company with a patent for a roofing product known as Tricom. It was a combined fascia, soffit and gutter unit for domestic housing manufactured by the traditional bucket and brush method in GRP.
Hambleside Manufacturing for the building industry was born and by 1978, thanks to another twist of fate, and much burning of the midnight oil, the company had developed a way of automating the process by continual profiling involving pulling a resin mix along a conveyor belt through a simple profile to give some shape.
Remarkably, the heat to trigger the thermostatic reaction in those early trials was provided by a single, strategically placed light bulb, and would subsequently provide the basis for a massive new investment in a fully automated factory near Inverness, Scotland.
Little did they know then, of course, that a major global economic recession was just around the corner and the embryonic Hambleside company was very much under threat as the UK housing market, and in particular the previously lucrative public sector, took a nosedive.
As a result the company quickly looked to expand the product offering and embraced the manufacture of profiled translucent sheeting roof lights for industrial buildings. Today, the Zenon rooflights product range remains an important part of the company’s offering, although the product which started it all, Tricom, did not survive the downturn.
Further diversification into the building sector came in 1983 with the first manufacturing of GRP valley gutters and roof trims for a new customer Danelaw Laminates based in Daventry. The arrangement worked well for a few years but by 1987 the relationship was becoming more fractious as Danelaw struggled with management and cash flow issues.
It was around the same time that accountant Chris Avery joined Danelaw and quickly determined that Danelaw needed their urgent assistance. As Chris recalls: “There was obviously an advantage to joining forces at that time. Hambleside clearly possessed the manufacturing capabilities but were weak on sales structure whilst, although struggling, Danelaw had a clearly defined sales strategy and a widely spread customer base with both contractors and merchants.
“It would take another four years of concerted wooing before we even got close to an official engagement, however, but finally in January 1992 the marriage was finally sealed with the forming of Danelaw Hambleside. Unfortunately, the honeymoon period did not last long, and within a further three months the company changed its name again but this time with Hambleside taking top billing over Danelaw.”
Continues Chris: “It would be nice to report that we all lived happily ever after but of course anyone who is involved in the construction industry knows it never works out quite like that. One of the most devastating setbacks came in 2003 when a fire all but destroyed the Scottish factory and production line. The business moved into a larger site and production was up and running within nine ‘hard’ weeks.
“It obviously didn’t seem like it at the time but out of the ashes a new more efficient factory emerged,” explains Chris, “and was perfectly timed to meet the increasing demand from a buoyant housing market. The business continued to innovate and seized an opportunity to install two new production lines, to develop a patented honeycomb insulation core for insulating GRP Rooflights whilst still allowing excellent light transmission.
The product won a Queen’s Award for Innovation in 2006 and, later that year, agreement was reached with the local council to build a new 50,000 sq. ft. factory two miles from the original site to house all the production facilities for injection moulding, honeycomb manufacture, roof light assembly and a comprehensive warehousing facility.
“By 2008, we were congratulating ourselves on a job extremely well done”, remembers Chris, but of course it wouldn’t be Hambleside without a twist in the tale. We all know what happened next with the greatest economic crash in living memory, and with it a drastic decline in building activity and orders for roofing products.
“There’s no disguising the fact that it was a very difficult period for the business and we had to make some very difficult decisions regarding the workforce although, unlike many, we were fortunate not to have all our eggs in one big construction basket. Other areas of the Hambleside business continued to perform strongly, especially the original printing arm, and that helped us to ride out of the storm.
“It took us until 2015, our 40th anniversary, to really get back to the levels we enjoyed in 2007, but everything is now in place to move forward with an exciting range of products to meet the rapidly changing needs of the construction industry,” enthuses Chris.
The iconic Danelaw brand has become a market-leading name know for quality and innovation and comprises an extensive pitched roofing range of GRP flashing products, self-adhesive flexible flashing, individual and continuous soakers, slate and tile ventilators, patented dry fix ridge and hip systems, eaves, soffit, cavity and underfloor ventilation products.
As the new stricter regulations come into effect and associated health risks with lead, and the vulnerability of both lead and copper to theft, the company report growing sales momentum year on year, particularly with the dry fix mortarless valley and bonding gutters.
“More recently, following end user feedback, we have also introduced a range of high-performing breathable roof tile underlays. Where appropriate, all products are backed with industry standards and BBA approvals for peace of mind for the contractors as a well as fully trained technical back up helpline,” states Chris.
Continuing to be at the forefront of Hambleside Danelaw’s offering is the unique waterproofing membrane system, Dryseal.
It is a pre-formed GRP component system for flat and low-pitched roofs. Ideal for domestic, commercial, green roof and heritage roof applications.
Sales and Marketing Director, Ian Weakford, adds: “Quality is at the forefront of everything we produce, and contractors are increasingly taking into account total installed costs as opposed to going cheap and facing costly callbacks at a later date.
“Dry fix roofing solutions are a classic case of the industry coming together to solve longstanding mortar problems, which have been inherent in the roofing business forever, and there are sure to be more innovations in the coming years to benefit both the builder and the homeowner.”
It’s fair to say that Hambleside Danelaw has always had a rather “novel” way of doing business in more ways than one!