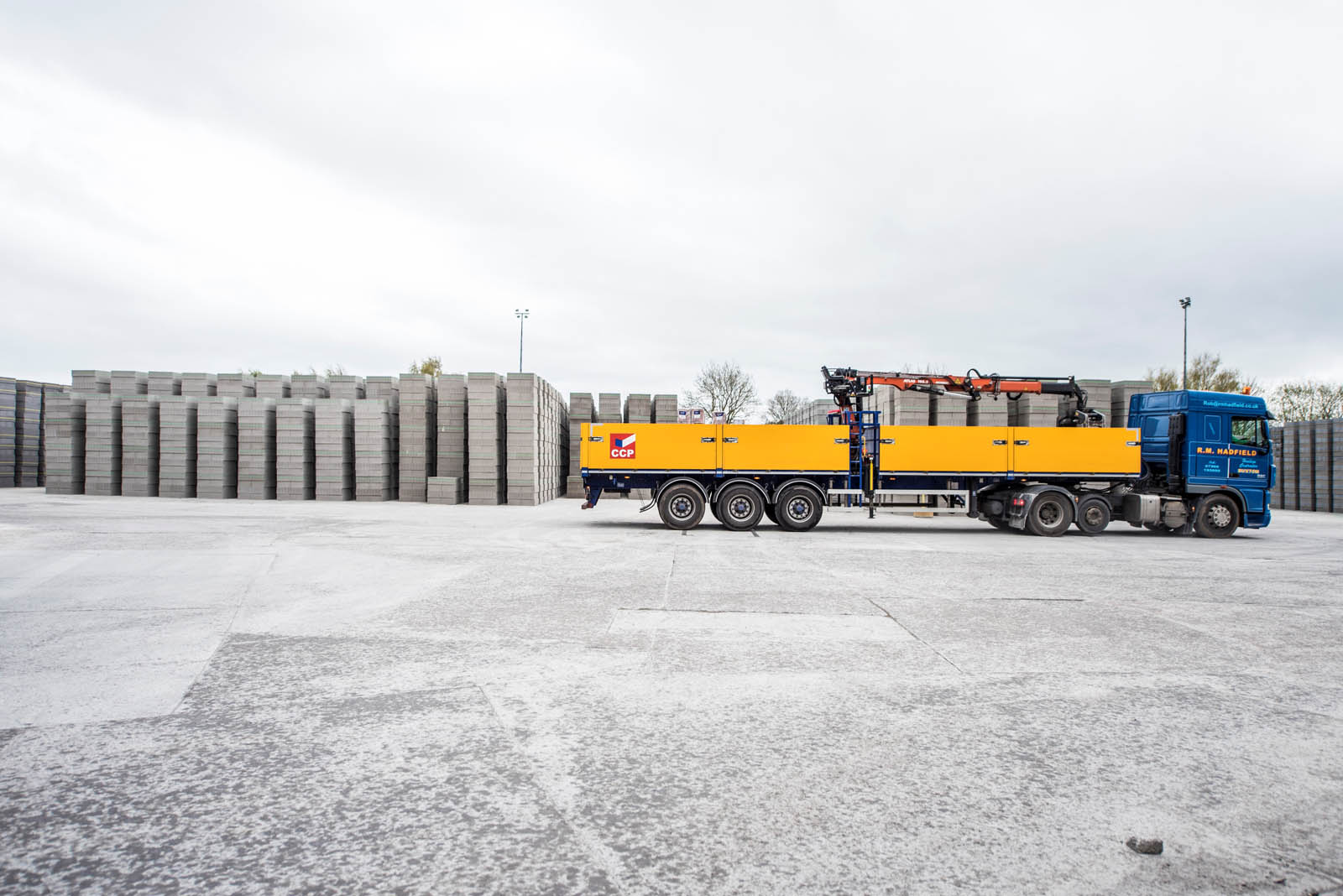
A new cement-free concrete block has the potential to make significant CO2 savings on projects. Professional Builders Lee Jones talks to its developers at CCP Building Products.
When it comes to addressing sustainability in construction the most noise has often been made around post-build measures, such as renewable energy generation or insulation, with less attention placed on the structural elements. Concrete is the most abundant man-made material in the world but its key ingredient, cement is a CO2 hungry solution. Indeed, it is currently responsible for around 8 per cent of the carbon dioxide emissions on the planet.
Of course, its versatility, and myriad builder-friendly properties, means it’s certainly not going anywhere any time soon, and that has placed the onus on the industry to tread with a lighter carbon footprint in their manufacturing processes, and it is a challenge that one block manufacturer has eagerly taken up.
CCP Building Products already supplies a full range of traditional concrete blocks and aggregates from its north west base and has now added to that portfolio with its own contribution to our collective low carbon future. Described as a UK first, Greenbloc is an alternative to traditional cement-based blocks that promises CO2 savings of up to 73 per cent, whilst at the same time retaining all the essential attributes of a high density, load bearing concrete block.
“The building materials market has traditionally been a conservative one but the demands of reducing our carbon footprint are shifting mindsets,” enthuses Michael Roddy, Managing Director at CCP. “By making some fundamental changes to the humble concrete block we’re playing our part and offering the industry the opportunity to address carbon emissions at the front end of a build. The beauty of Greenbloc is that it is, in essence, exactly the same as a standard concrete block. In fact, if you stood the two next to each other you wouldn’t be able to tell the difference.”
“In terms of manufacture there’s all the traditional components of Class 1 aggregate, a binder and water, which is then compacted into a mould, and cured in an oven” adds CCP General Manager, Martin Bains. “It conforms to BS EN 771 – 3: (2011), complies with Part E of the Building Regulations for Walls and Floors and satisfies all the same thermal and strength characteristics of a conventional load bearing concrete block. Not only does it not look any different, but builders won’t have to store or use it any differently from the cement-based products to which they’re accustomed.”
It is that property which the boots on the ground with their hands on the blocks will welcome. It has hitherto been the case that solutions that make any significant difference in terms of sustainability have invariably required design changes in buildings, or alterations to working practices, but that’s simply not the case with Greenbloc. Whether in foundations, internal leaves of cavity or party walls – or load bearing walls – it is suitable for all current applications, exhibiting all the same characteristics, including dimensions and weight, as its Ordinary Portland Cement (OPC) counterpart. Its impressive carbon off-setting potential is simply derived from eliminating cement as the binder element in favour of Ground-Granulated Blast-furnace Slag (GGBS), a recycled by-product of the steel industry.
“We already produce a high-quality concrete block and that’s something we were never going to compromise on,” concludes Michael Roddy. “That’s why it has taken us eighteen months to go through all the testing in order to make sure that the market can have complete confidence in the performance of this product. Up until now sustainability has all-too-often been focused on operating carbon emissions post-build, rather than the carbon generated during the build schedule and in the manufacture of building materials, but Greenbloc can redress that balance.”
Although there is a cost implication in using this cement-free alternative that’s pale in comparison to the potential carbon reductions. CCP’s own figures suggest that, for an average three-bedroom house, OPC blocks account for almost 3.7 tonnes of CO2. By contrast, Greenbloc accounts for just 981kg of CO2 for the same house, achieved through a saving of 1kg of CO2 per block and adding up to a total saving of 2.7 tonnes of CO2 per house. Data from the National Energy Foundations suggests that switching to Greenbloc is the equivalent of offsetting the electricity emissions on an average three-bedroom house for almost four years.
For more information on Greenbloc from CCP Building Products Ltd visit www.ccp.ltd/blocks/greenbloc