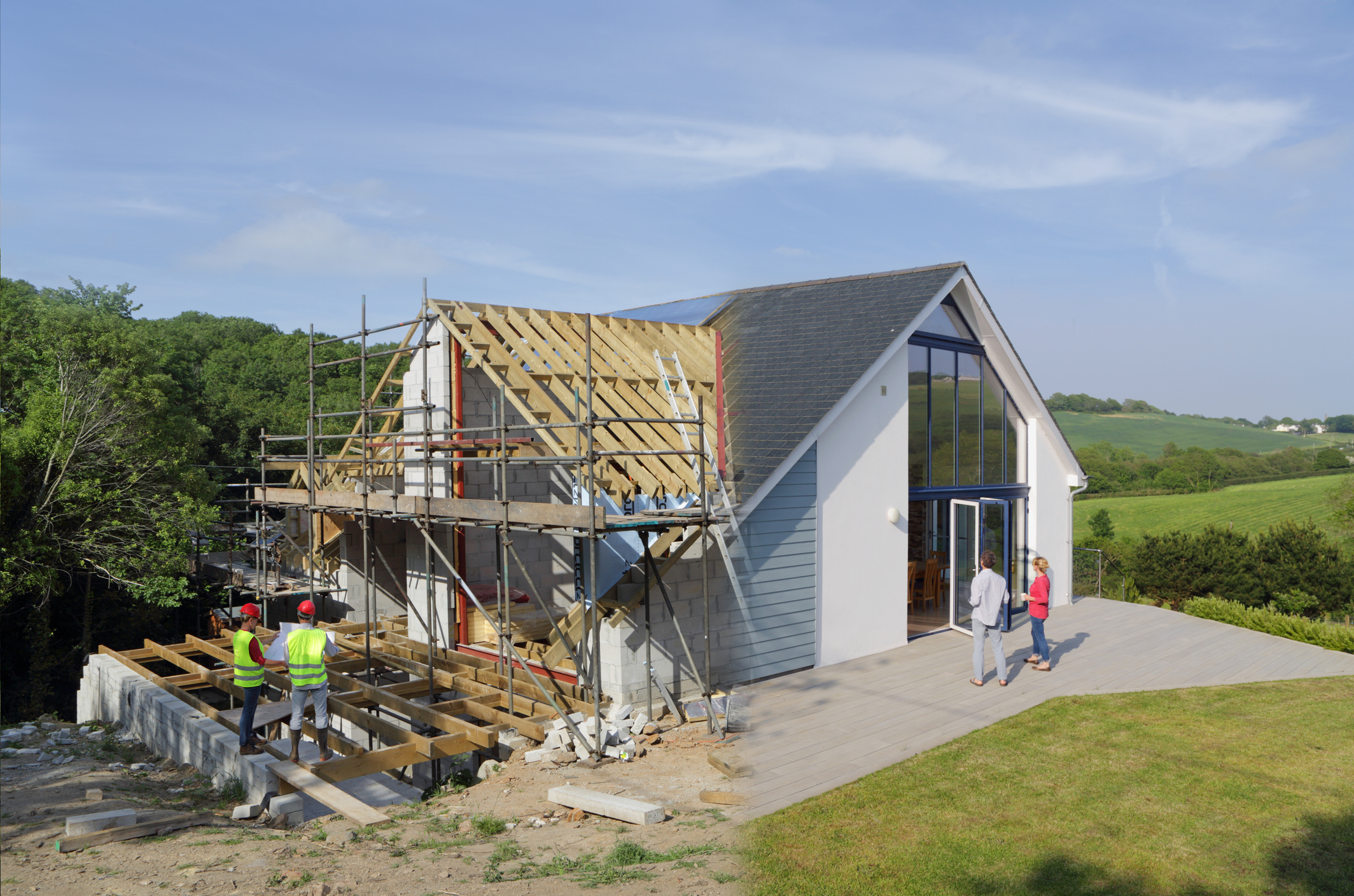
Matt Castles technical manager at Cedral looks at the differences between warm and cold roof insulation and its implications for contractors.
While we all know that about a quarter of all heat energy in homes escapes through the roof, the number of poorly insulated houses in the UK is less well understood. In 2019 the UK government introduced a legally binding target to reduce greenhouse gas emissions to net zero by 2050. Making houses less energy intensive is all part of this.
Warm and cold roofs
There are two ways to categorise how a roof has been set up to manage heat – a warm roof or a cold roof. It’s a simple concept, but amazing how many builders get it wrong when constructing a house or extension – especially where condensation is concerned.
‘Cold roof’ insulation is usually positioned between the ceiling joists and is often used when planning dictates a lower roof. As the roof rafters and remaining roof structure are not directly insulated, the loft remains ‘cold.’ This is why careful consideration of condensation is needed to ensure the roof system works correctly.
If the installation is not correct – through either poor fitting or low-quality products – the temperature of the house can also be significantly affected through thermal bridging, with the cooler temperature of the roof rafters transferring to the structure below or heat escaping into the loft.
When it comes to meeting the criteria for the Future Homes Standard, correctly installed continuous insulation takes less time to fit and costs less. Insulation usually takes place during the initial building construction as it can be a significant task to retrofit later in the building’s life. Installation of insulation layers within the roof structure can be accessed more readily without expensive retrofit costs, especially the insulations at the eaves.
A ‘warm’ roof is usually a lot easier to build – in the case of extensions, for example – and involves putting insulation on the ‘top’ of the roof – ie. directly beneath the roof tiles and breather membrane panel.
Installing a warm roof with insulation sheets and a vapour control layer is important to prevent the build-up of condensation, as the increased overall temperature of the roof usually combats the creation of unwanted ‘dew points’.
When a roof pitch is made higher to accommodate a warm roof system – and hence has longer rafters – fibre cement slates are a good option as they are lighter than natural slates, and last just as long on the roof when installed correctly.
Coping with condensation
The Building Regulation Part C sets out that “roofs should be designed and constructed so that their structural and thermal performance are not adversely affected by interstitial condensation.”
The key for roofers is to ensure that the ventilation in the roof space is well considered and delivered when installing a roof. There are a wide range of products designed to assist roofers with any ventilation challenge – from specially designed eaves, concealed tile options, ridge and top abutment ventilators. Which device to choose will be dictated by the dimensions and pitch of the required roof design. It is recommended that a ventilation system within the roof is installed to create a circulatory air flow and crossflow ventilation. There is a lot of industry guidance on this issue, and Cedral Roofs cites BS 5250 which provides the minimum requirements for roof ventilation.
Another important aspect of managing condensation in the roof is the installation of underlay. Here in the UK there are three main types of product on the market.
Non-breathable underlay is a more traditional solution and needs to be installed with appropriate ventilation systems to be as effective as required.
Vapour permeable underlay is very popular in the UK and is designed to let moisture out without letting moisture back in. It is BBA certified for use in tiled ventilated cold roof constructions but needs to be secured and draped correctly so following the manufacturer guidance during installation is essential.
Thirdly, air permeable underlay systems are a relatively new entrant to the market. They can release more moisture than vapour permeable underlay. However, there are two key notes of caution: 1) they are not yet acknowledged by British Standard BS 5250 which means they should be selected carefully depending on the project and 2) they are more expensive and if a strong ventilation system is in place the impact of the air permeable underlay is no better than other underlay solutions.
The best way to control condensation within a roof space is to not cut corners. Use and install the best underlay solution for the project at hand and install a suitable ventilation system to ensure the long-term performance of the finished roof.
For further information on the range of solutions from Cedral visit https://www.cedral.world/en-gb/