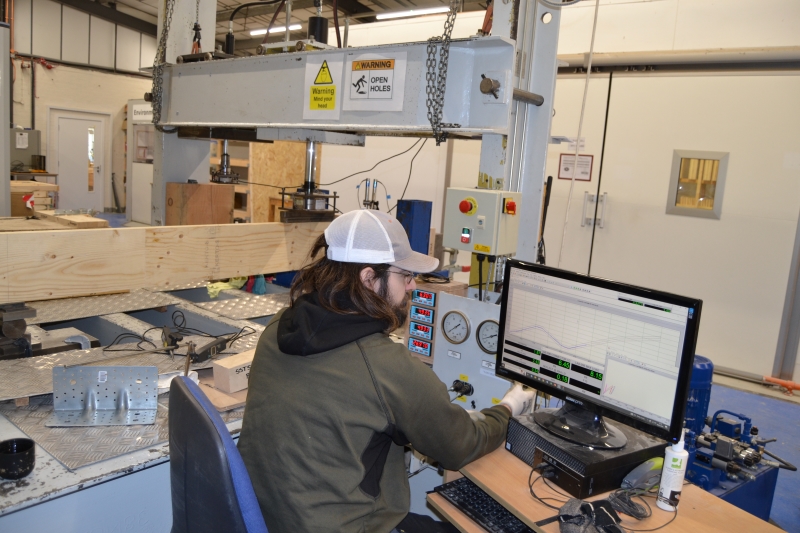
If you’re assuming that there’s not much to choose between the wood connectors, fixings and fasteners you’re familiar with then think again, because one manufacturer is putting that opinion to the test. Professional Builder visits a unique Simpson Strong-Tie facility to find out more
There’s a reason that professional builders will come to instinctively trust a product, especially when it’s a load bearing component and failure is not an option. What won’t be apparent to the trades is the huge amount of work that goes on behind the scenes into making sure that Simpson Strong-Tie’s solutions perform.
The manufacturer’s testing facility is unique in its sector in that it is United Kingdom Accreditation Service (UKAS) accredited and audited. It’s a status that eloquently testifies to the quality of the range – and a significant level of ongoing investment. At the same time, it’s a lesson to every builder that if you trust in a supplier with a meticulous attention to detail then quality will always count.
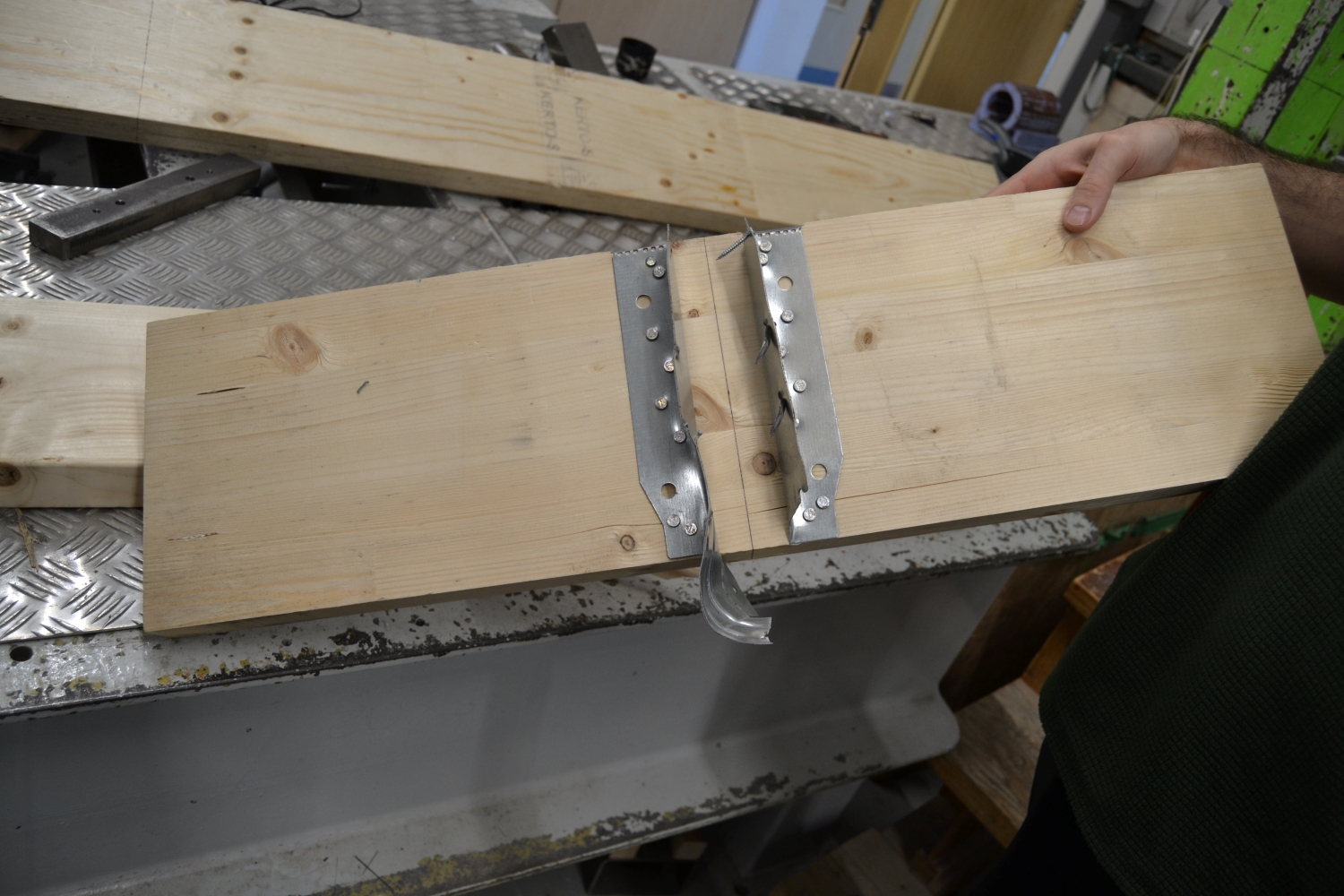
The standards for all the tests that are carried out at the centre are accredited by UKAS, for some products this is an EU Market product approval requirement. Moreover, all the work that the six-strong Simpson Strong-Tie team carries out needs to reflect real world scenarios and a full range of applications. I-beams, laminated veneer lumbers (LVLs), glulam and cross laminated timber (CLT) products from leading manufacturers are held in stock. The timbers themselves have to be very carefully selected and prepared with Simpson Strong-Tie technicians visiting merchants themselves to select timbers based on density, moisture and visual inspection quality as the selection standard requires a range of timber densities to be used.
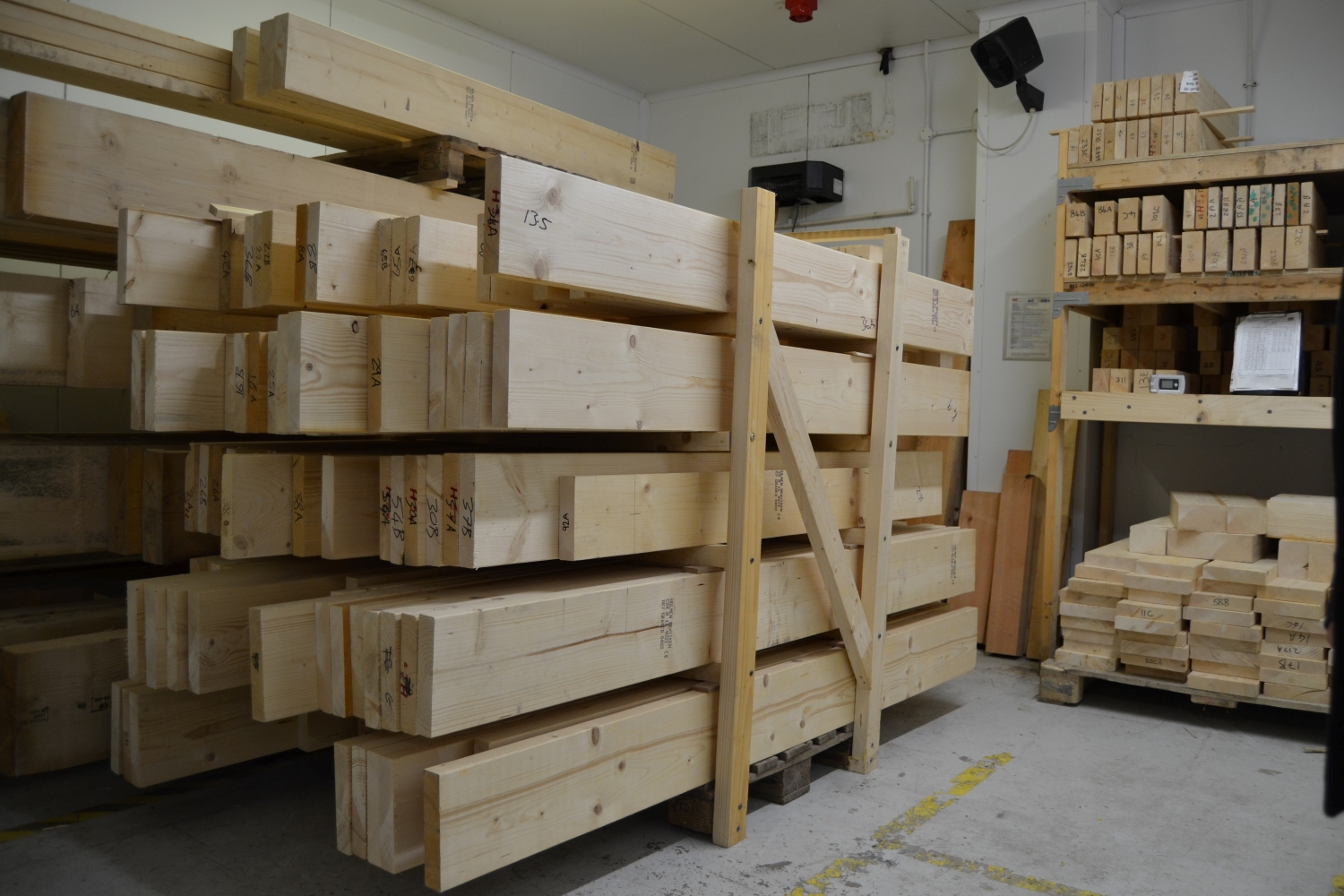
Once back at the Tamworth facility, the wood is stored in environment chambers which are monitored daily by UKAS calibrated instruments, a process governed by another standard to ensure timbers are conditioned appropriately before use. The correct level of moisture content needs to be achieved before any further testing can be undertaken and some materials – such as oak – can take years of conditioning before they’re ready. Even softwoods of a decent thickness can be held in the chamber for over 12 months, with strict adherence to a regime of daily monitoring.
When the timbers have completed first stage conditioning they can then be assembled with Simpson Strong Tie products and, after second stage conditioning is complete, are ready for testing – a process that can take a few weeks to several months depending on the size of the timber elements. When fully conditioned the testing can begin, and the forces involved are huge. Joist hangers are an effective long term solution to connect supported elements (joists) of a structure to supporting members by providing a strong connection fitting, and their strength can’t be in doubt. We witnessed a Simpson Strong-Tie SAE Joist Hanger undergoing a ten-minute compression test. In this instance, one hanger withstood 37kN of compressive force before failure, which is around 3.7tonne of load, and more than the gross vehicle weight of the largest Ford Transit. The same test is undertaken at least five times. Evaluations are made in different orientations – typically in download, uplift, and laterally – with all the materials that an SAE joist hanger has been designed to work with, and with every available size.
If that’s not enough then the joist hanger is analysed not only for load but also for deflection, this test’s standard requirement called for all tests to be taken to at least 15mm differential deflection between the supported (joist) and supporting member. If it’s a new product the whole painstaking process can take several months to complete.
A further set-up calculates the energy required to pull a standard 5x50mm CSA Connector Screw from a material and the time it takes to withdraw from the timber sample. To ensure the integrity of the test the fixing needs to be inserted into the material as close to 90° as possible, and it should achieve a max force before failure force of anything up to 3kN for between 3 and 7 minutes.
A 1.4mm thick, 15mm wide piece of carbon fibre – a sample of a material that’s used to reinforce and repair concrete in the Simpson Strong-Tie FRP solution – is subject to some equally brutal treatment. With one of the best strength-to-weight ratios available, it’s time to bring in the heavy mob with a machine with a 300kN or 30 tonne capacity. In testing, it demonstrates the tensile strength to achieve 70kN, or 7 tonnes, which is the equivalent of suspending four mid-size cars or one average African elephant from this unassumingly flimsy strip.
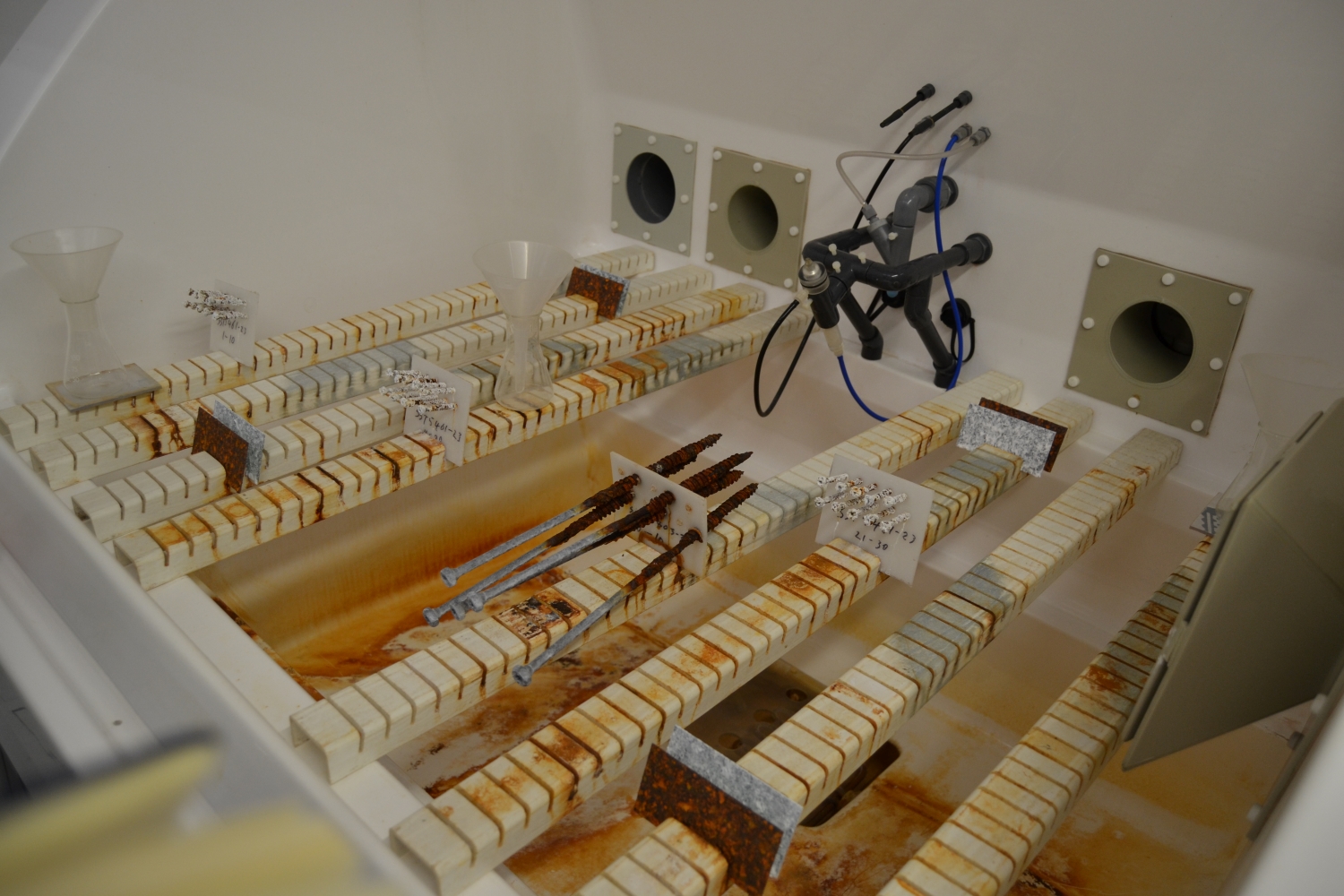
Every stress that fixings and wood connectors will need to resist is calculated and that includes corrosion. It is here that enclosed machines can subject screws to harsh environmental conditions, including incessant salt spray, heat and airflow, with cycles of varying humidity into the bargain. Over just a few months, years of exposure of coastal like environments can be replicated, alongside more conventional and real-world climatic conditions.
Some types of screw will, in fact, undergo at least 10 individual test methods. The hardness of an individual fixing at 50microns from its edge is evaluated, with a diamond indenter compressing into a cross section. The torque required to screw into different
types of pre-conditioned timbers is examined, with a separate test for pulling out a fixing. An X-ray machine measures the thickness of the zinc coating along the entire length of a screw down to the miniscule level of single-figure microns, as well as its chemical composition, and the geometry of a screw is measured to determine conformance to manufacturing specification tolerances.
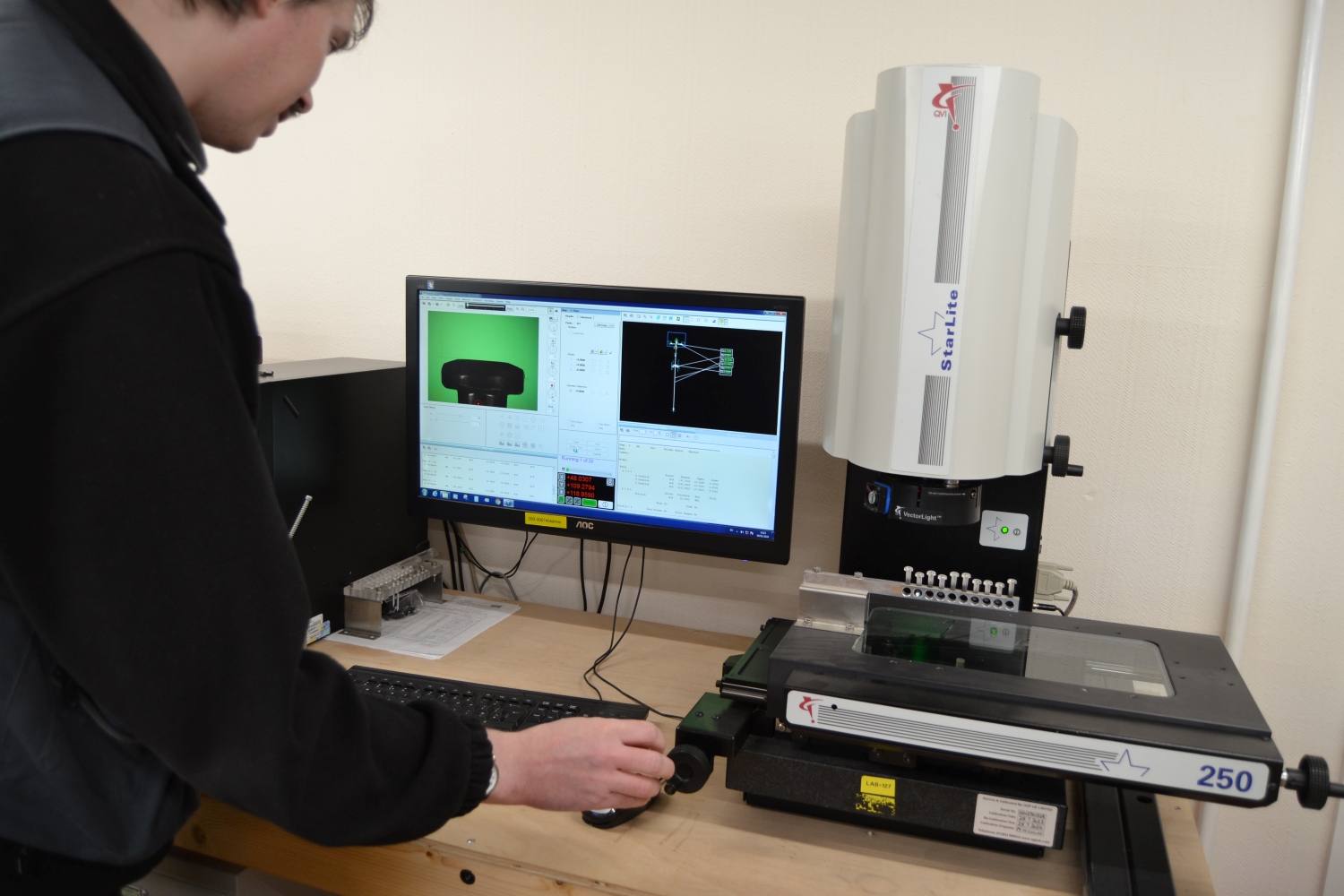
Every new product is subject to an entire battery of tests but existing Simpson Strong-Tie solutions running from the Tamworth production line are regularly analysed for quality control purposes. Changes in building techniques also demand new types of testing. The wood connector specialist is increasing its presence in the Cross Laminated Timber market, for example. CLT is a material that exhibits high levels of tensile and compressive strength and the fixings need perform to the same high standard.
There are over 100 pieces of UKAS calibrated equipment at Tamworth. In addition, the accreditation service undertakes a sampling audit of the testing centre’s work every year, including demonstrations of individual tests, staff training, and comparisons with other labs. All of that adds up to a considerable investment and ensures that Simpson Strong-Tie continues to have all the right connections.
For further information on Simpson Strong-Tie visit Simpson Strong-Tie (strongtie.co.uk).