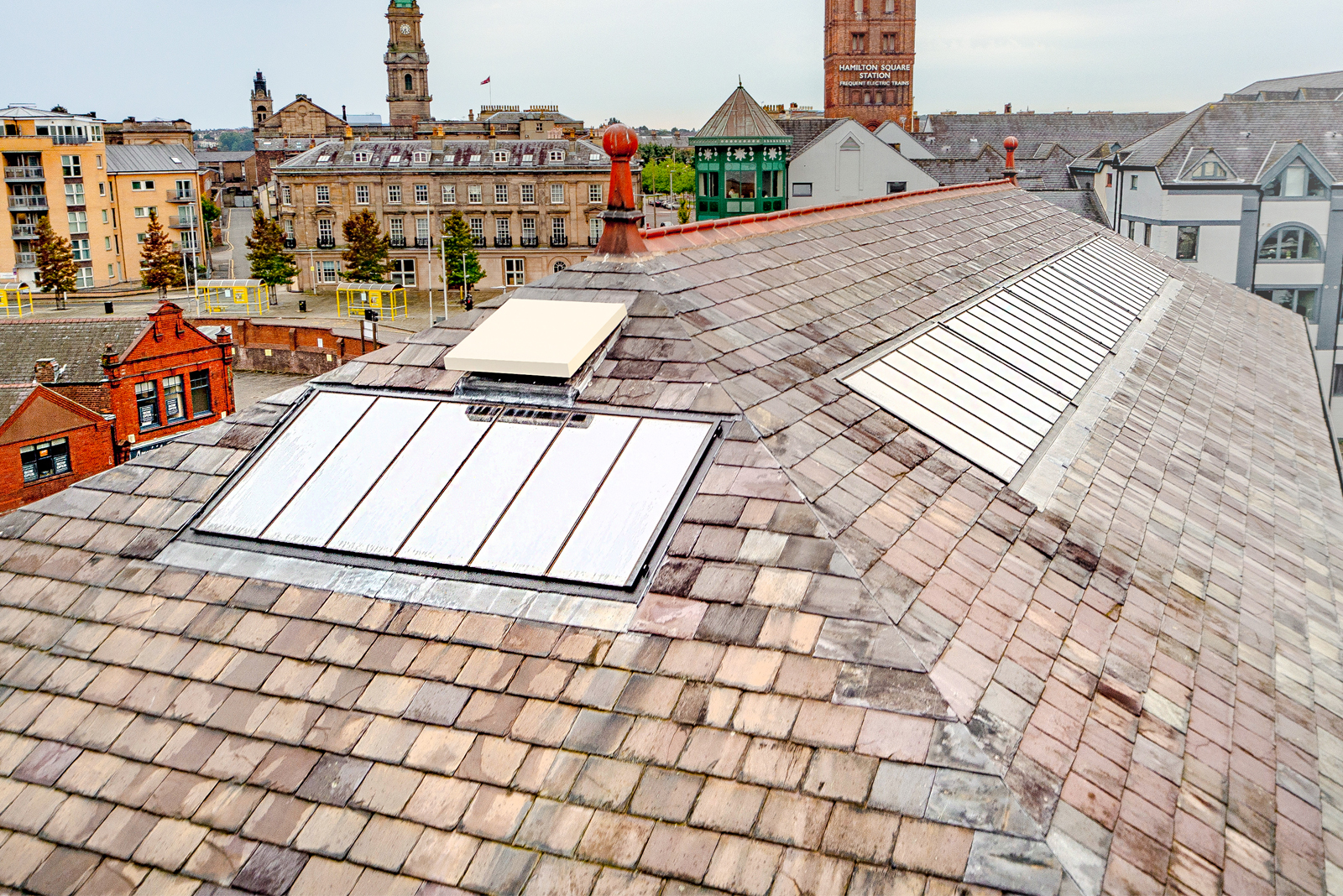
Paul Trace from Stella Rooflight discusses the practicalities involved in specifying large rooflights.
In recent years we have noticed a trend towards larger rooflights, with sizes regularly exceeding 2,500mm in width, height or both. While Stella can certainly accommodate these, one has to appreciate the practicalities of weight, transportation and cost.
It stands to reason that the larger the rooflight, the thicker the glass will need to be. Therefore, as rooflight sizes get bigger, their weight can increase exponentially. In context, our double glazed units comprising of 4mm thick glass weigh 20kgs per square metre and those using 6mm are 30kgs per square metre. Triple glazed units are 30kgs and 45kgs respectively. Add the stainless steel frames and hardwood liners into the equation and you can start to see how even a modest sized rooflight can weigh something akin to a small elephant! Indeed it’s not uncommon for us to produce rooflights weighing in excess of 200kg.
It is important to consider how the rooflight is going to be lifted from the ground to roof level, and what the weight implications might be for the structure. Stella can weld stainless eyelets to the rooflight frame to aid the lifting process, and we would suggest doing this on frames which weigh in excess of 100kg, which is the point where we expect a crane might be required. However, does the site have suitable access for any specialist lifting equipment, and has this additional cost been budgeted for?
stThe weight of an opening rooflight will also determine whether it is manually operated or requires electric actuation. We would suggest that our largest manually operated rooflight be around 1,000mm wide or 1,400mm high. Anything over this size will generally require electric actuation to lift the weight and, in the case of wider casements, to provide a tight seal. Manual operating casements are less expensive than electric, so there is a cost element that also needs to be considered when specifying larger opening rooflights. There is no maximum size in terms of what is possible to manufacture, although it is worth keeping in mind that a single piece of glass with an area over 5m2 becomes significantly more expensive.
Fortunately, there are alternatives to using large expensive single panes of glazing, such as introducing glazing bars to reduce the unit sizes, linking frames, and having more than one casement. This not only makes the rooflights easier to transport, lift and install, but can also reduce the price.
Another area for consideration should be the safety of large areas of glazing situated high up in a roof structure. Regardless of size your rooflight should meet the BS 5516-2: 2004 patent glazing and sloping glazing for buildings standard. This code of practice for sloping glazing defines that inner panes must always be laminated wherever rooflights are more than 5 metres above floor level (increased to 13 metres for panes less than 3 square metres) or are located over water (e.g. swimming pools). The Standard permits the use of toughened inner panes in other applications (for example where rooflights are less than 5 metres from floor level), but only where a stringent risk assessment for the particular application has been completed and has concluded that the use of toughened glass does not give any additional risk to those below the rooflight.
No glass is impervious to breakage so it is important to remember that roof glazing can and often does sit high above common areas in a home or office, so there will always be an element of concern if a unit were to break.
Certain industry bodies are calling for all rooflight glazing to include a laminated inner pane to provide greater security in the event that the glass breaks. There can be no dispute that laminated glass is safer because it forms a net when broken, which remains in one piece, whereas toughened glass breaks into little cubes and will fall down onto whatever is below.
However, laminating rooflight glass creates its own unique set of problems, as annealed laminate is prone to thermal fracture and heat stress.
This risk can be reduced by polishing edges. However, the low-e coating is not practical for polished edges as there is a risk of damaging the coating. Swapping the low-e coating for a laminated glass with treated edges is likely to have a negative impact on the thermal performance of the unit. Using products such as SGG Cool-Lite on the outer pane can help as this has both solar reflective and thermal coatings, but these do not have a self-clean coating, which is an important consideration for pitched rooflights as they are usually positioned out of reach.
Thermal Stress is created when one area of a glass pane gets hotter than an adjacent area. If the stress is too great, then the glass will crack. The stress level at which the glass will break is governed by several factors. Toughened glass is very resilient and not prone to failing due to thermal stress. Laminated glass and annealed glass behave in a similar way and the thicker the glass the less tolerant it becomes, which is an important factor for larger rooflights.
Solar control glass either reflects energy or absorbs it to reradiate the heat outwards. By its nature it gets hotter than clear glass and glass that is designed for thermal efficiency alone. Whilst the majority of installations are within the operating tolerance, in some cases fluctuation in heat can put the stress beyond the limits. Laminated glass is also heavier which needs to be remembered when planning lifting schedules and structural requirements.
In summary, while there is a growing trend for projects to include more and larger rooflights, it is not as straightforward as just adding them to the plans. Clearly there is so much more to specifying large rooflights than meets the eye and while your rooflight manufacturer will be able to provide recommendations, ultimately having a better understanding of what glazing is required and involving a qualified structural engineer in the early phases will resolve any issues you may have further down the line.
For further information on the Stella Rooflight range visit https://www.stellarooflight.co.uk/