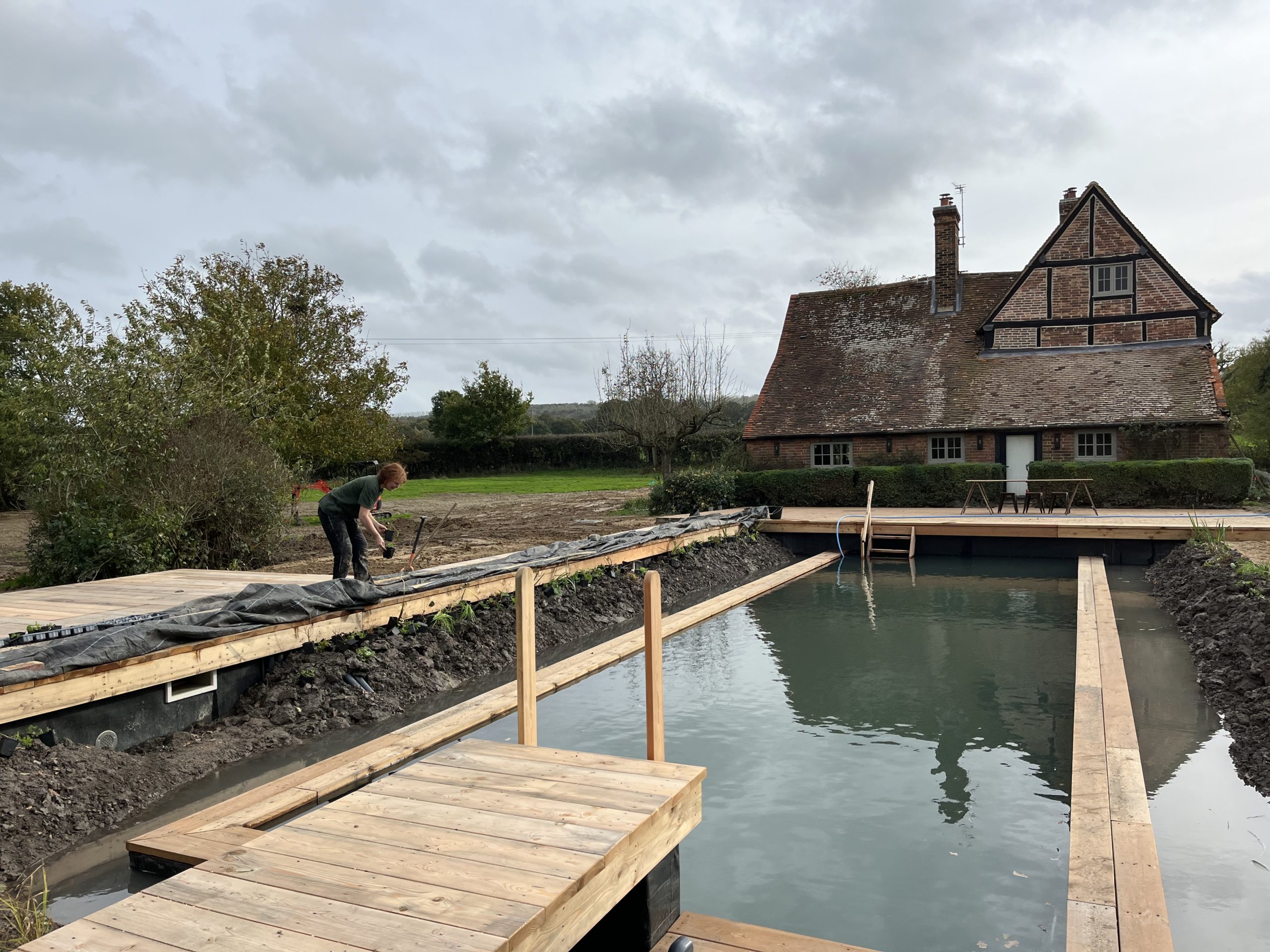
Anderton Concrete’s Stepoc concrete shuttering system has delivered the perfect finish for a natural pool construction
When award-winning natural swimming pool builders, Ellicar, required an efficient method of construction for an installation in the gardens of a listed property located on the outskirts of Kent, it turned to Anderton Concrete for the answer.
The natural pool’s design incorporated a swimming area separated from dedicated regeneration zones via low submerged walls, with each regeneration area containing water plants which help to naturally filter and purify the water, keeping it hygienically clean and crystal clear.
Having designed and installed natural pools for over 20 years, founder and owner, Sarah Murch, required a resilient solution that would not only deliver impressive longevity, but simultaneously meet her specific design requirements, whilst keeping to project timescales.
In order to successfully construct the reinforced concrete chamber for the 15metre long x 4metre wide x 1.8 metre deep swimming zone, Sarah specified Anderton Concrete’s unique concrete shuttering system following a recommendation from a structural engineer.
Consisting of precast concrete blocks that weigh less than 20kg each and can be both vertically and horizontally reinforced, the use of Stepoc enabled Sarah’s team to quickly and efficiently build the entire pool wall structure in just three days.
To streamline the installation process, Sarah partnered with the manufacturer’s technical team to tailor the structure’s design to the dimensions of each Stepoc block, working to a full course. Each block sits over a L shaped rebar which is cast into the concrete raft. Then as each course of the 900 concrete blocks was installed horizontal rebars were fitted to provide additional reinforcement. The finished walls were filled with one single concrete pour.
Speaking of the project, Sarah said: “With any natural pool build, it’s crucial that the structure provides not only a perfect, smooth finish for the pool’s flexible liner but also the exact finish for us to install the hard landscaping around the water’s edge including architectural stone paving, wooden decking and internal coping. Being able to tailor the design of the walls to the dimensions of each Stepoc block ensured we achieved this, streamlining the entire process.
“Having never used Stepoc before, myself and my team were extremely pleased, both with the initial installation process and the overall quality of the finished construction. So much so that we have already specified the system for another two upcoming projects and are modelling our pool construction designs accordingly.”
Once the concrete structure was built, Ellicar’s pool team lined the entire pool with a waterproof, flexible TPO liner, followed by special aggregates into which the water lilies, deep aquatics and marginal plants such as irises and watermint are encapsulated. In addition, the pool is fitted with Biotop’s biological filtration system. The pipework from the filters and pumps being brought through flanges in the walls, which were installed at wall construction stage. The filter chamber is covered with a wooden deck with access hatches.
Tim Fields, Structural Products Manager at Anderton Concrete, said: “Combining the ease of blockwork with the versatility of in-situ concrete, Stepoc maximises on-site safety and efficiency, whilst minimising installation costs.
“Whilst Stepoc has been specified on a range of swimming pool projects over the last two decades, this is the first time the system has been utilised to construct a natural pool structure and the results really do speak for themselves. It was fantastic to collaborate with the Ellicar team on this project and I look forward to working with them again on upcoming builds.”
A popular choice for a diverse range of single-skin retaining wall requirements, Stepoc has been proven to be one of the most cost-effective methods of construction. Following independent analysis, it has been proven to offer a substantial cost saving of over 30% when compared with in-situ concrete, whilst delivering an approximate saving of 20% against cavity block construction.
The innovative system has also been awarded the British Board of Agrément (BBA) Certificate 20/5774, evidencing Anderton Concrete’s first class engineering excellence and dedication to supporting industry professionals in achieving a world-class built environment.
For further information on Anderton Concrete visit https://www.andertonconcrete.co.uk/