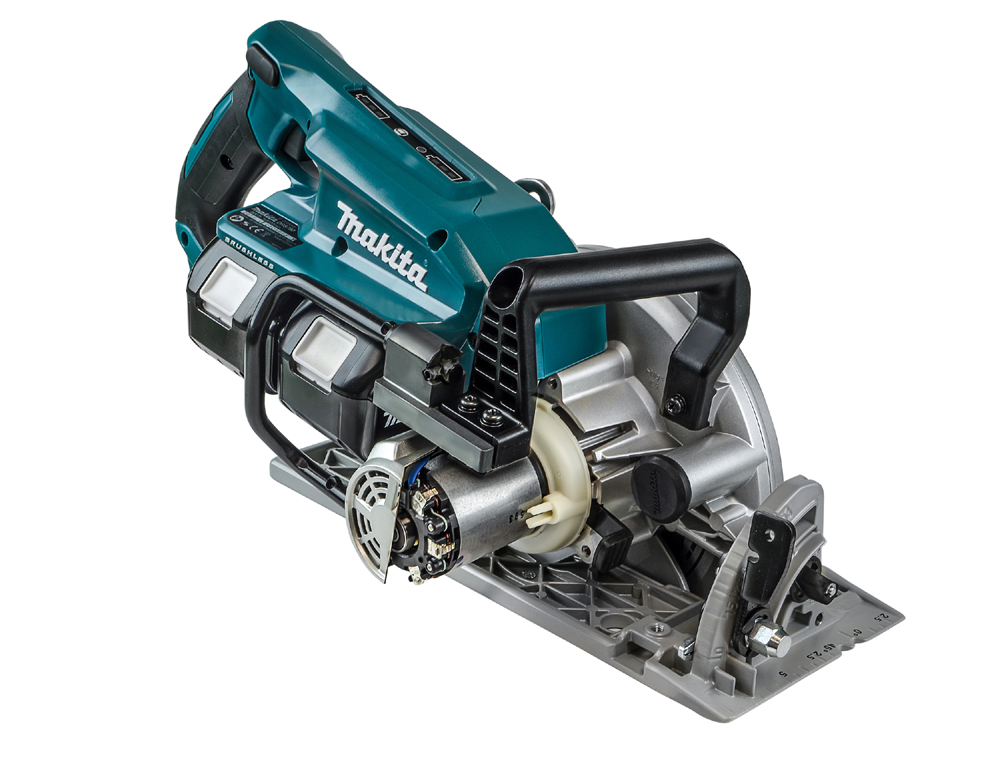
In our Tech Talk new series, the Makita team will discuss some of the most innovative tool technologies available on the market, and look at how they can benefit tradespeople. In the first instalment, Tony Coleman, technical manager at Makita explains what brushless motors are and how they can benefit tradespeople.
You’ve no doubt come across the term ‘brushless motor’ by now, when looking for a new power tool – but what does that actually mean? Looking at a traditional brushed motor first, it has four basic parts: carbon blocks (the brushes), a ring of magnets (the stator), an armature (the rotor), and a rotary electrical switch (commutator). The magnets and brushes are stationary, while the armature and commutator rotate together on a motor shaft within the magnets.
The carbon blocks conduct a magnetic current between the stator and the rotor within the motor. By using positive and negative magnetic fields, the brushes turn the motor, which makes the tool work.
Although effective, brushed motors are more prone to suffer from wear and tear – this is because the brushes make contact with the commutator within the motor. This contact causes friction, which ultimately results in the brushes having to be replaced regularly during the lifetime of the tool, incurring an ongoing maintenance cost.
Alternatively, brushless motors don’t have carbon brushes or a commutator, but instead utilise an on-board electric circuit and the motor works on electric currents. The locations of the magnets and windings are also reversed: the magnets (the stator) are on the conventional motor shaft and the copper windings of the armature (the rotor) are fixed and surround the shaft.
To operate, the on-board electronic circuit sends electronic currents towards the stator coils. When the stator coils receive the electric currents, they become electromagnet and the position of the north and south poles within the motor changes. This pulls or resists the rotor’s magnet and makes the rotor rotate continuously.
The omission of brushes makes brushless motors incredibly efficient – as there is no friction created, and the tool does not waste energy through heat production. Even in hard industrial applications where the tool is in use for extended periods of time, brushless motors produce considerably less heat at the housing surface compared to brushed alternatives. This ultimately increases productivity, as operators can continue to work without concerns of the tool overheating. Subsequently, this also means that brushless motors have longer run times – in some cases up to 30 per cent more.
Without brushes applying friction within the motor, a brushless motor can also produce more torque per weight – this is because torque is not affected by friction and heat production. This means that less power is required to use the tool – again, improving efficiency and extending the lifespan of the tool as it requires less maintenance.
As brushless motors include fewer moving parts, they can also benefit from a more compact design compared to tools that include brushed motors. This means that the tools themselves can be smaller and lighter – major benefits for tradespeople who use the tools for extended periods of time, as muscle fatigue can be reduced.
Brushless tools are certainly worth a look – especially for tools that will be used regularly for extended periods of time. For example, Makita’s new DRS780Z 18Vx2 185mm brushless circular saw includes the precision engineered Makita brushless motor, which has been designed to be up to 50 per cent more efficient compared to alternative models.
The DRS780Z also benefits from the inclusion of a 36V motor, which is powered by two 18V Lithium-Ion batteries. A pair of fully charged 18V Lithium-Ion batteries from Makita will last almost twice as long as a tool that is run on a standard motor. This significantly improves on-site productivity as, not only can the tool be used for longer, but Makita’s 18V Lithium-Ion batteries also charge within just 22 minutes (3Ah) and 55 minutes (6Ah) – meaning tradespeople can get back to work quickly.
Power tools that utilise a brushless motor can be incredibly beneficial. Makita’s brushless motors are more efficient compared to brushed alternatives and result in fewer maintenance costs due to reduced friction inside the motor. Reduced friction also keeps the temperature of the tool more consistent, preventing the tool from overheating and subsequently increasing on-site productivity.