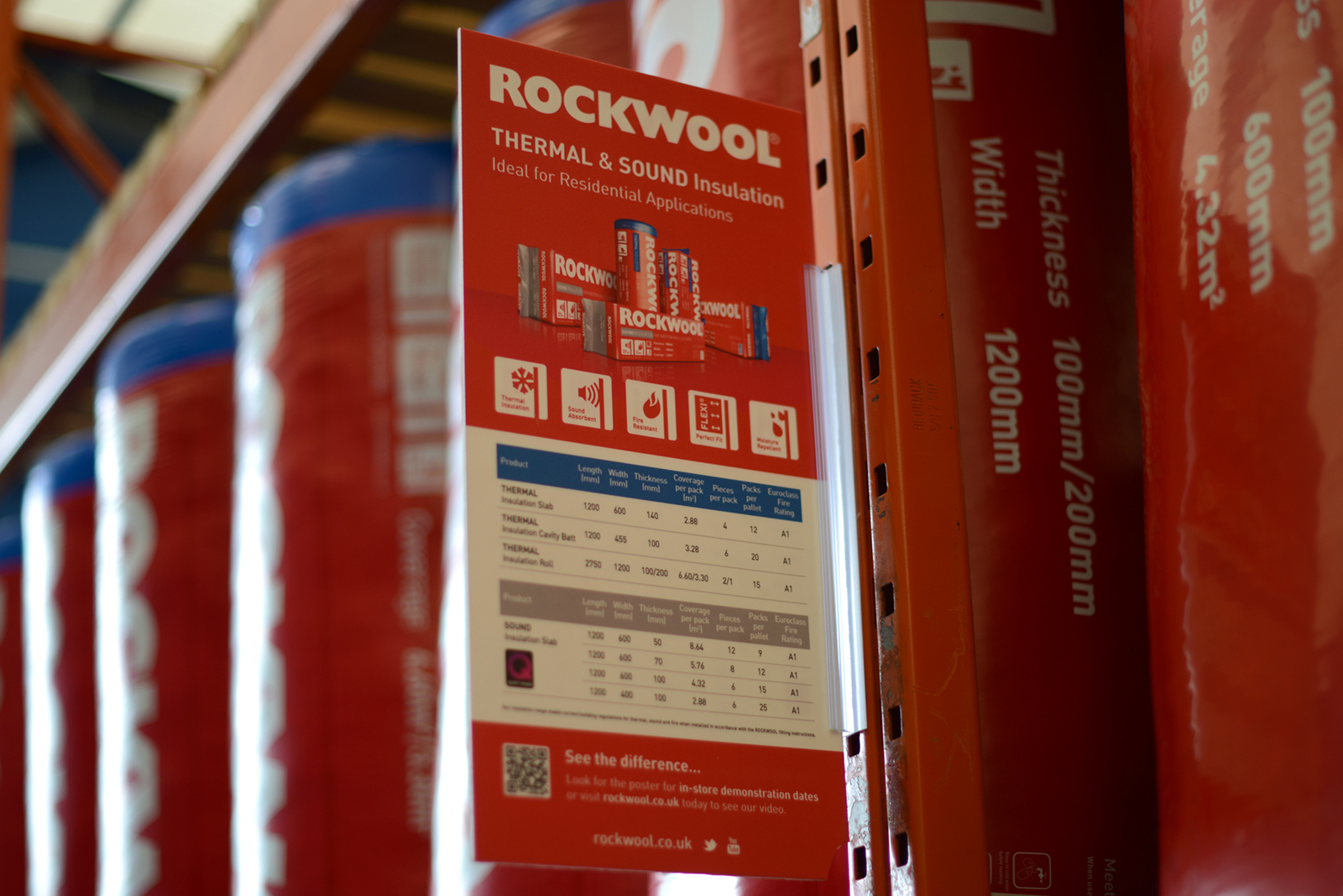
Paul Barrett, Head of Product Management at Rockwool, advises on the major changes to Approved Document L which will come into force in England later this year.
Several changes to Approved Document L (ADL) are due to come into force in England in 2022. These updates are a stepping stone to the Future Homes Standard that aims to make sure all new build homes built from 2025 produce around 75 per cent less carbon emissions than those constructed under current regulations.
Through updates to ADL and Part F (ventilation) later this year, the Government wants to reduce emissions by 31 per cent as part of the journey to the higher target three years down the line. As, at the time of writing, no firm date for Part L changes has been announced, those currently designing new build projects, looking for land or working through planning, should have the amendments very much on their radar.
While housing developers who have submitted notice or deposit plans before June 2022 can build to current Part L standards if work has commenced by 2023, to build saleable, comfortable and efficient homes for the future, it is good practice to be working to higher standards now.
What’s changing?
One of the big changes builders will see in new Part L is a focus on closing the gap between specified and as-built performance, with greater scrutiny of build quality. In England, this will mean the introduction of Building Regulations Part L (BREL) reports for dwellings and the need for photographic evidence of compliance.
Photographs will need to be taken at various construction stages before elements are concealed to show build quality and that the designed details have been followed. When it comes to insulation, images should show evidence of the thermal continuity at foundations/structures, external walls, roofs and openings, pipes and ducts.
A good fit
The upcoming changes will mean installers need to achieve a tighter, continuous fit with insulation in the future. But what does this mean in practice?
In theory, this could mean more cutting on-site and/or taping at board joints with foil tape to achieve a seamless fit. But for the already busy fitter, this equals extra time on jobs that they don’t have. However, by choosing stone wool insulation versus other types of material on the market, there are easier ways to achieve the as-designed performance, without impacting on time and workload.
Stone wool insulation is highly pliable meaning it can be closely friction fitted to frames, without the need for impractical levels of precision cutting on a busy site. As it limits the need for cutting, there’s also less margin for error, making it easier to achieve reliable and effective thermal performance that reduces thermal bridging.
The pliability of stone wool also helps at abutments between insulation boards, another area that can be prone to thermal leakage. The composition of stone wool insulation allows individual slabs to knit together to create a seamless fit that helps deliver the designed U-values.
For the busy builder, the same stone wool product can also be used for multiple applications, such as loft, floors and walls – helping to minimise wastage and streamline material ordering and planning.
A lasting reputation
For builders and developers who pride themselves on building quality new build homes and thrive on a strong reputation, stone wool insulation is also a natural choice.
As well as making it easier to achieve thermal continuity at build stage, stone wool based insulation gives ongoing performance and advantages beyond thermal comfort that benefit developers and homeowners in equal measure.
Buildings do naturally expand and contract, and over time can lead to the formation of gaps and voids. Stone wool, however, has strong dimensional stability and when fitted under compression, can accommodate building movement, without a loss in thermal performance or sumping and sagging. In fact, it’s proven to provide consistent performance – shown by tests even after 55 years in use – without a drop in its thermal properties.
For developers, this gives confidence in the quality of a build well into the future and avoids timely and costly customer call backs.
With stone wool insulation, builders can also give potential buyers the added reassurance of fire safety, something that’s increasingly on the homeowner’s radar. As stone wool is naturally non-combustible, it does not contribute to fire spread and is capable of withstanding temperatures in excess of 1,000oC.
Likewise, because it is manufactured from naturally occurring volcanic rock that is continually replenished by the earth’s crust, stone wool is a sustainable choice, which again, is becoming more of a motivator for purchasers.
As the pressure to build more energy efficient homes increases, forward-thinking builders and developers can get ahead of the curve by designing and building homes to the upcoming standards and speccing solutions that make a seamless fit and ongoing performance that bit easier.
New Part L
– Focus on designed vs built performance
– New BREL report for homes
– Photo evidence taken at various construction stages
– Evidence of compliance needed by building control
Checklist for choosing insulation
– Does it require precision cutting or can it be flexed to fit?
– Is it easy to fit around services?
– How does each slab join? Is taping required or does it naturally knit together?
– Is it resilient to building movement over time?
– Does it provide fire, acoustic and thermal performance in one?
– What are its sustainability credentials?
For further information on the range of insulation solutions from Rockwool visit https://www.rockwool.com/uk/