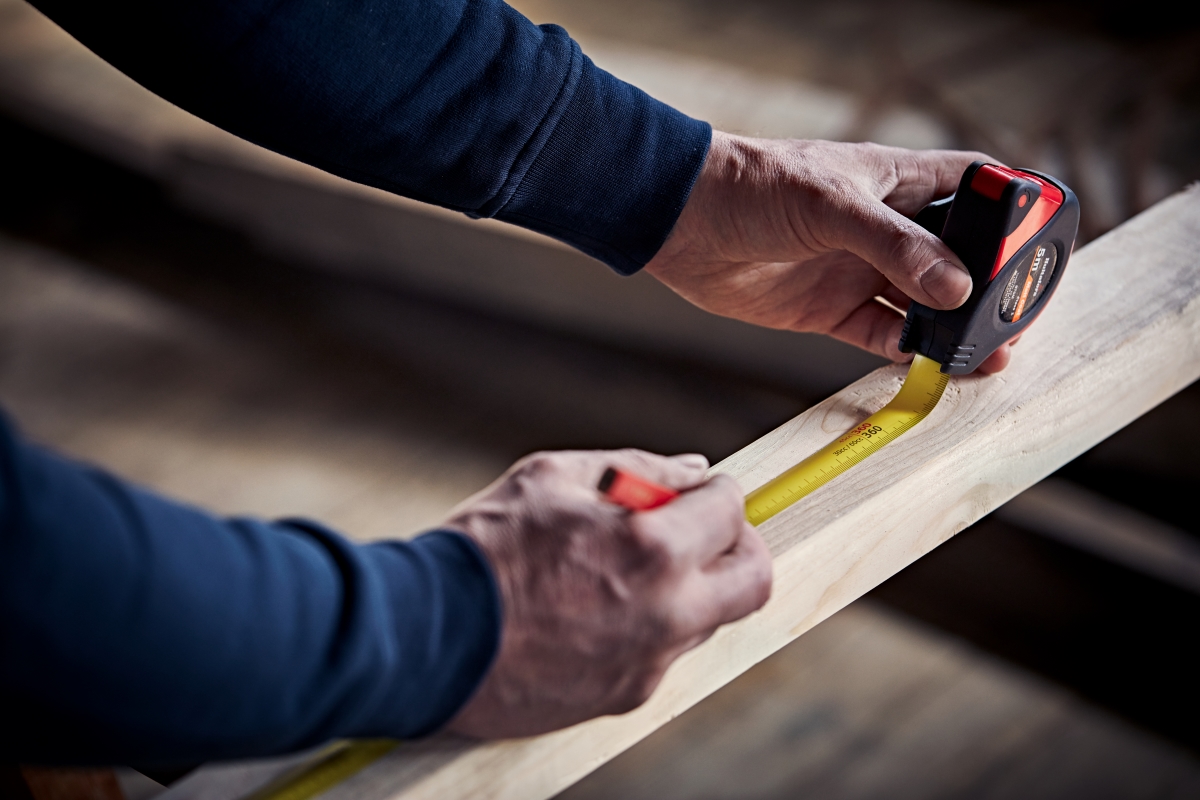
Professional Builder visits the Hultafors Group’s former Fisco tape measure factory for a fascinating insight into just what it takes to produce a precision product
If you’ve ever bought a tape measure from a DIY outlet, you’ve probably instinctively known that it’s not going to last. It just doesn’t sit right in the hand and there’s a flimsiness that feels very quickly like a false economy. There’s an old saying that you should measure twice and cut once but that only holds true if you can be confident of the accuracy and durability of your tape. It’s here that the meticulously engineered Hultafors range is the builder’s friend and what goes into making sure that these products measure up for the trades is very revealing.
Established by Leo Fisher in 1941 to produce radio valves for the war effort, Fisco can point to a proud history of tape measure manufacture since 1946 and has been part of the Hultafors Group since 2008. Every part of the brand’s tapes are fabricated from high specification raw materials at its Rayliegh factory, guaranteeing the company’s complete ownership of the production process. That includes ABS plastic injection moulding for the casing and any other components in plastic, as well as the rubber protection, and patented shock absorbency.
All of the products are either ultrasonic welded or screwed together in an automated process that’s fast, consistent and highly accurate. This is how the popular belt clip on the 5m/6ft Class 1 Big T – a tool that is renowned for its robustness – is constructed, where the holster stays on your belt and the tape measure clips in and out. That same product benefits from a nylon end hook over-moulded with rubber for improved grip and no slipping.
“There’s a lot going on inside our cases,” reveals managing director, Gary Beadon, “and it’s the attention to detail in our finished product that makes it stand out from its competitors. Many of the tape measures sold in the UK have a very fast return action, for example. By contrast, we include a carefully tuned spring in our tapes to allow for a balanced return, placing less stress on the components. The brake lever is also made from a self lubricating plastic, which facilitates better brake control and holding power.”
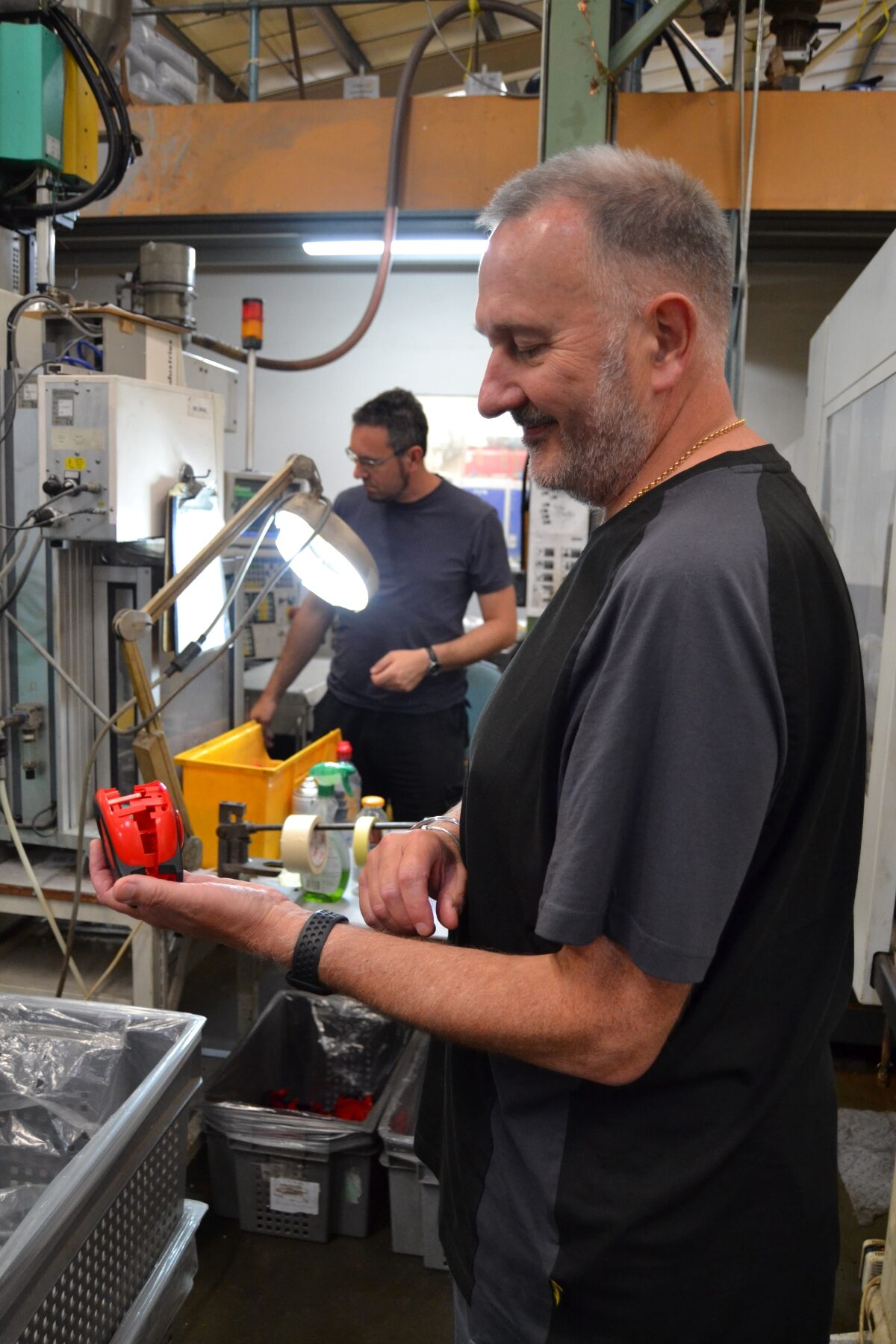
Hultafors tapes are also rigorously tested at its extensive Essex production facility. The tapes are expected to last for at least 10,000 extensions and reversals, are dropped from an 8metre height, whilst the hardness of the material itself is scrutinised. As Gary can testify some of that testing can often be extreme: “When we switched from the steel can construction of our closed case long tapes in 2014 to an ABS plastic case there was initially some scepticism from end users. We demonstrated that the latter product was so much stronger by running it over with a two-tonne forklift. The plastic unit was still intact, whilst the steel one was destroyed.”
As any builder will know a job that will stand the test of time needs the best materials and it’s no different with the tools used. In a single month the factory will consume over 35,000kg of steel, all supplied as large cartwheels. Hultafors utilises SK5 steel for its measuring blades, which has an 85% carbon content – and SK4 for the spring material, with 95% carbon – both of which exhibit enhanced hardness and strength. This prevents the tape from curving and deflecting when extended at any distance, whilst the manufacturing tolerances are microscopically tight, with blade thicknesses not allowed to vary between a -/+ 0.005mm range.
Painting the blade is equally painstaking with the first stage a degreasing with a heated liquid vapour. Next – and in a process that again sets Hultafors apart as a premium product – an iron phosphate is applied to prevent rust, before the steel is applied with the yellow paint that the UK market demands. All this is carried out with carefully controlled levels of viscosity and thickness – and a thorough testing regime. The coating is subjected to a British Standard pencil hardness test, which determines at what point the paint is scratched. The crosshatch test, also a British Standard, cuts through the material in diamond shapes, with a special adhesive tape then applied. If any of the surface coating is removed that represents a failure, whilst salt baths test for corrosion.
The measuring scale ink jet printing is undertaken in another temperature controlled environment where precision and repeatability is an absolute prerequisite. The tape is fed through a machine that exposes it to an intense plasma. This prepares the surface for the ink, allowing that ink to then adhere more readily. The material is then passed through two sets of print heads, which print the upper and underside of the blade, and is then UV cured almost instantaneously. Incredibly, and in another demonstration of Hultafors’s absolute commitment to maintaining its command over the whole production process, these hi-tech ink jet printing machines are designed and built in-house and are unique to the manufacturer.
The journey doesn’t end there because, once printed, there’s a further protective layer applied. A nylon additive coating would be the standard, whilst Hultafors’s long tapes benefit from a more durable ‘Tough Coat’ nylon. Blade accuracy and surface imperfections are scrutinised at the assembly stage. At Hultafors the concave in short tape blades is achieved in a cold concave process, where many other manufacturers will heat the blade to achieve that distinctive curve, which can introduce accuracy issues.

Perhaps most impressive is the accuracy that a 30-metre-long test bed for the finished Class I product can achieve. The tape is put under force to its maximum length and examined along random points by a laser interferometer. Temperature and atmospheric pressure is accounted for, and it can test to within a fraction of a human hair at 0.0005mm.
So, when you’re next looking at buying a tape measure bear in mind that that they are by no means created equal. Indeed, if you want your tool to go the distance, then get the measure of Hultafors.
As the only UK manufacturer of measuring tapes, Fisco Tools is product to be a member of Made in Britain. It’s high-tech manufacturing facility covers over 60,000 square feet and produces over 1,500 high quality measuring instruments every hour. For further information on the Made in Britain organisation visit Fisco Tools Ltd – Made in Britain.
For further information on the Hultafors range of tapes visit Long and short tape measures.