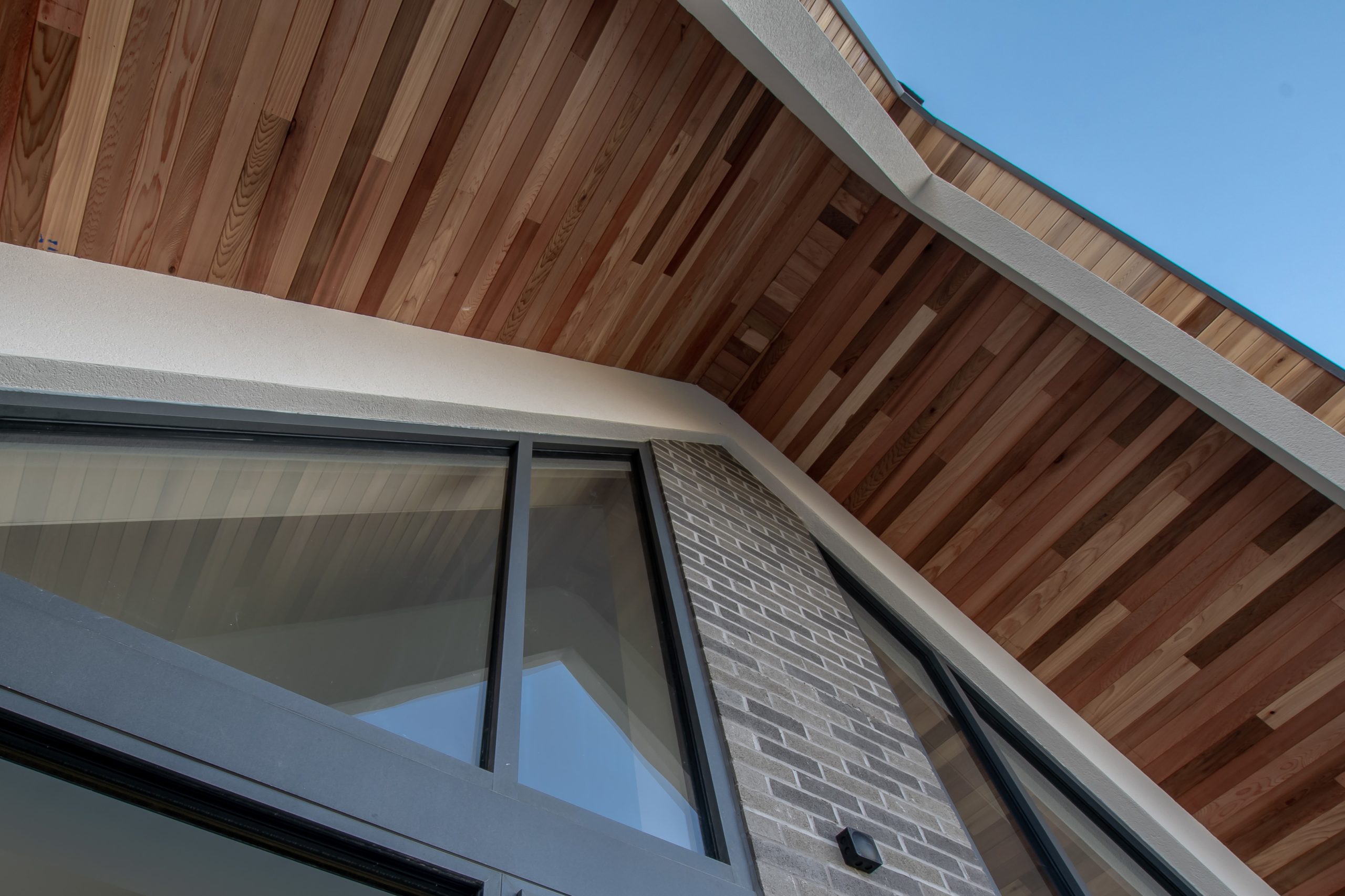
Chris Griffiths, Head of Product Sustainability at Marshalls plc, gives some advice on creating sustainable homes.
Creating a sustainable home is now a top priority for house builders, from locally sourced materials to energy efficiency measures. In a recent survey by Marshalls, 43.5% of people would pay more for a home built with sustainable materials – motivated mainly by doing their bit for the environment and saving or generating energy for their home.
Professionals and homeowners alike welcome the growth of sustainable material choices – but how easy is it to know what makes the most significant difference and what sets some materials apart from the rest? Many housebuilders are trying to achieve their sustainability goals through solar panels, improved insulation, more efficient white goods, alternative heating technologies and LED light fittings, which are all positive steps. But, can more materials be changed to unlock extra carbon savings and create more sustainable developments?
In this article, we will explore three innovative approaches that you may not have considered before to enhance the sustainability of your projects without compromising on style or design.
Concrete bricks
The manufacturing process of concrete bricks is partly what makes them a more sustainable option over traditional clay facing bricks. For clay bricks to harden they need to be fired in fossil-fuelled kilns, creating significant carbon emissions. Concrete facing bricks, on the other hand, harden naturally through an exothermic process, meaning that significantly less energy is needed in their curing.
In addition, concrete actually absorbs CO2 over its lifetime – a completely natural process referred to as carbonation or “sequestration”; bricks absorb CO2 from the atmosphere as they age and harden. Once the CO2 comes into contact with the concrete, a catalytic process permanently transforms it and locks it into the material, so even when the product is crushed at the end of its lifecycle the carbon will not escape. Marshalls concrete bricks, for instance, can absorb 4.2kg of CO2 per square metre over a 60-year lifespan, and the total lifetime reduction in CO2 compared to traditional clay facing bricks on the market has been calculated at 49.1%.
Did you know?
Innovative manufacturers have spotted an extra opportunity to lock even more carbon in concrete bricks using a process called carbon sequestration. Currently being used by Marshalls on its Fairway from Grove range, waste carbon is injected during the manufacturing process with no impact on the materials’ performance, durability or appearance.
Low or no cement
Cement is a crucial ingredient in many building materials, but although it accounts for around just 10% of the ingredients within a concrete mix, it can account for over 80% of the total carbon footprint. For building projects, concrete is a solid, durable, cost-effective material for which a suitable alternative has yet to be found So, how can you make better choices to lessen the impact on the environment but continue benefitting from this versatile and durable material?
As we’ve seen above, concrete has carbon absorbing benefits, and it’s the cement ingredient which can make it less sustainable. As manufacturers develop more sustainable materials, many are investing in low or no cement options, so ask your suppliers or merchants to point you in the right direction.
If you’re interested in the science behind the process, it’s helpful to know how it all works. Marshalls, for example, has collaborated with several suppliers to harness by-products from other industrial processes and waste materials. These materials exhibit properties comparable to cement-based systems when activated. Activators are composed of a blend of raw materials, which chemically react when combined with cement replacement materials to produce concrete with equivalent strength and durability to regular concrete.
Permeable outdoor spaces materials
When it comes to hard landscaping the outdoor spaces and communal areas of your developments, you should consider permeability as well as selecting British-made or quarried materials. Whatever the material of choice, it’s often harder for water to soak into the ground where it lands. This can lead to overwhelmed drains and flooding, so you should consider permeable paving or grass paving to get around this.
Permeable paving looks like regular block paving but features a specially engineered wide joint and carefully specified jointing material which allow water to seep through the joints and reach the ground rather than accumulating on the surface and running off into a drain. For driveways, you could also look at grass paving, which is a load-bearing grid system which allows grass to grow through the openings in the grid. As well as reducing surface water runoff this has the extra benefit of increasing biodiversity, creating a more attractive, natural finish, and potentially lowering the temperature around the properties on very hot days.
These examples show that revisiting simple material choices can help create more environmentally friendly homes and communities without compromising quality or aesthetics. With the demand for sustainable homes on the rise, embracing these practices aligns with environmental goals and positions builders at the forefront of the industry.
For more information on Marshall’s low carbon Fairway facing bricks, visit Fairway Facing Bricks | Sand Faced Bricks | Marshalls.