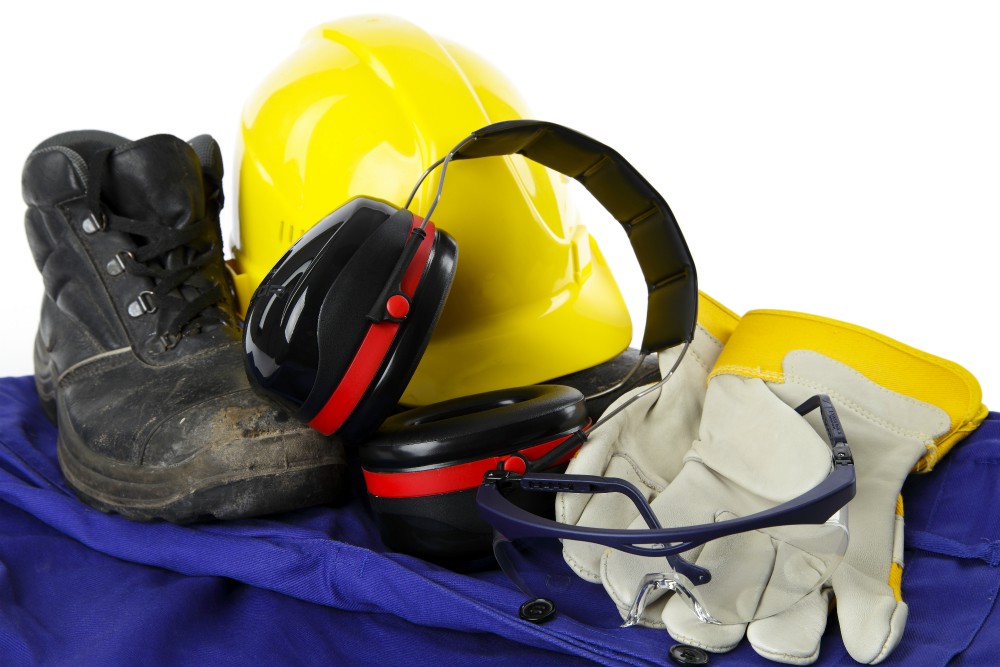
HBXL’s Joanna Mulgrew explores the management of health and safety.
‘Oh great! Health and safety paperwork,’ said no one ever… I admit this is a pretty dry topic but there’s nothing more important in construction. We all accept that ‘processes’ are a matter of course when it comes to payroll, personnel issues and finance – well managing health and safety should be no different.
So here goes. The Management of Health and Safety at Work Regulations 1999 require employers to put in place arrangements to control health and safety risks. As a minimum, you should have the processes and procedures required to meet the legal requirements, including:
- a written health and safety policy (if you employ five or more people);
- assessments of the risks to employees, contractors, customers, partners, and any other people who could be affected by your activities – and record the significant findings in writing (if you employ five or more people). Any risk assessment must be ‘suitable and sufficient’ (same applies for COSHH);
- arrangements for the effective planning, organisation, control, monitoring and review of the preventive and protective measures that come from risk assessment;
- access to competent health and safety advice, for example see the Occupational Safety and Health Consultants Register (OSHCR)
- providing employees with information about the risks in your workplace and how they are protected;
- instruction and training for employees in how to deal with the risks;
- ensuring there is adequate and appropriate supervision in place;
- consulting with employees about their risks at work and current preventive and protective measures.
Still with me? Handily, the HSE produced the ‘Managing for health and safety’ (HSG65) document. It’s now widely recognised as sound guidance on good practice for managing the health and safety of business and projects.
It features a ‘Plan, Do, Check, Act’ framework that identifies the key actions needed in each part of the project cycle and relates them back, where appropriate, to leadership, management, worker involvement and competence.
The key actions covered are:
- Determining your health and safety policy
- Planning how you will implement your policy
- Profiling your health and safety risks
- Organising for health and safety
- Implementing your Construction Phase Plan (simple or detailed depending on the project)
- Measuring performance
- Investigating accidents and incidents
- Reviewing performance
- Learning lessons ready for your next project
Even with the framework, selecting the relevant paperwork, let alone implementing it, takes time that no one has. Which is why organising the repeatable tasks and documents in the process makes sense. And the good news is there are various options that do this from simple templates to intuitive, intelligent software.
So at HBXL we’ve used the ‘Plan, Do, Check, Act’ approach as a checklist for users of Health & Safety Xpert 2018 software to identify which area of the process their documents sit under (as our infographic demonstrates). Once they’ve described the job, the software automatically selects the appropriate paperwork required for every stage. Not surprisingly it significantly cuts down the time it would normally take to complete the necessary documentation ready for review and implementation on site. And it’s easy to use too!
Created with leading experts, the software is regularly checked for changes in legislation and has everything needed for CDM 2015 compliance – which is another story…