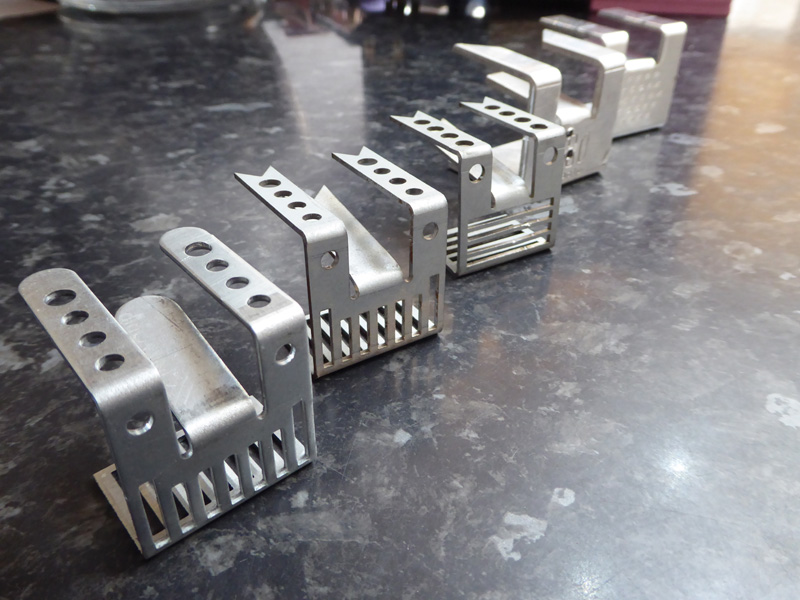
Professional Builder visits a builder who has come up with a solution to fireboarding an RSJ.
Over the years, it’s become apparent that the vast majority of inventions that come to a builder are the result of frustration. Perhaps after performing the same laborious task for the umpteenth time, you throw down your tool belt and say enough’s enough. With Mick Attwood, however, the last straw didn’t break his back, instead it was a plasterer working on the same job who had to bear that burden.
Mick says: “It was during the winter of 2016, and one of the plasterers has just finished fitting some fireboard around a steel girder. I remember he was having some trouble getting the timber noggins wedged into the steel and, although it was icy cold in the building, his blood was beginning to boil. He’d just finished and climbed back down the ladder when he turned to me and said those immortal words: “There’s got to be an easier way of doing this”. That sparked something in my mind, I must admit. It was quite strange, as I’d fireproofed hundreds of steel girders myself, and never thought to do anything about it. It was just one of those slow jobs that had to be done. It wasn’t until I stepped back and saw someone else doing it that I was able to get some perspective on it.”
So Christmas came, the time traditionally set aside for workers to relax and enjoy a break. Being a builder, however, the festive holiday for Mick meant fighting the urge to get stuck back into work. Sat by the fire, his mind kept turning back to his colleague’s fireproofing frustration and he knew he had to find an answer. Slightly more unorthordox than watching DVD boxsets all afternoon, perhaps, but by the end of the holiday Mick had produced the first prototype for GirdaGrips from his garden shed.
“There have been many incarnations of the design, minor improvements as we’ve gone along, but the principle hasn’t really changed – a clip to directly connect beam and board. Everything about the clip is functional, there’s nothing aesthetic about it at all. It will never be seen after all. The two end holes on the side that attaches to the beam are bigger so if you need to fireproof a wall you can fasten it to the wall instead. You can have the clips welded to the girder, as the clips come with weld holes.”
One aspect of the clip which has changed from its fireside drawing, is how the screws attach the board to the clips. Initially, the clip was made from aluminium and the screws could simply puncture the clip’s material. However Mick found it impossible to strike a balance between the metal being thick enough to add tensile strength and thin enough to allow the screw to puncture it. In the end, Mick switched to steel and came up with the clip’s most inventive aspect, a feature he is calling the ScrewCatcha slots. The thin slots that run down the side of each clip allow the screws being driven through the board to locate the gaps and grab hold of the clip with no chance of moving.
The main selling point of the GirdaGrip is that it greatly speeds up the fireboarding operation, and this is where Mick sees it taking off. He tells me: “The big housebuilders especially, they’re all about speed and they’ll go for anything that speeds up the job. If you think, each new build house has at least one steel girder in – that’s a huge potential. For each standard job, you can save about two and a half hours. I can have the job finished whilst a joiner is still getting his tools out of the van.”
But as quick and easy as the process of using the clip might be, the process behind its manufacture has been a little more toiling. “The past two years have actually been a bit of a slog. Luckily, the clip is good, so I believe in it and I know it will take off. However, it’s been an expensive process. My wife’s been very supportive, luckily, but there have been times when you wonder whether it’s worth it.”
Luckily, the simplicity and ingeniousness of the clip itself convinced the Sheffield builder to keep going, and after prospecting a number of metal workshops – ironically none of which were located in the traditional metalworking heartland of Sheffield itself, much to Mick’s disappointment – he managed to get the clip off the ground. And now it’s going, it doesn’t look like Mick has any plans of slowing down any time soon, as he revealed: “I asked the plant owner, ‘are you sure you have the capacity to produce 30,000 of these clips each week?’ he just smiled and pointed to the press and said they’d produce that amount each day, so it’s all systems go from here!”