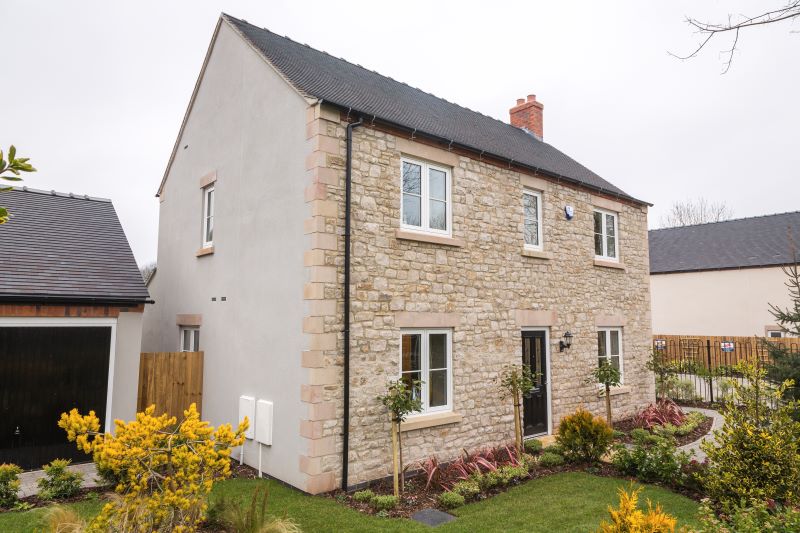
Martin Benn, Head of New Build at Eurocell, takes a look at how effective window and door solutions can help deliver the energy efficiency and sustainability enhancements that housebuilders are looking for – and consumers want – as the current regulatory landscape alters.
The Future Homes Standard (FHS) is set to be introduced in 2025 and, with it, a step change for all stakeholders charged with transforming the UK’s housing stock so it is more energy efficient, more sustainable and, ultimately, low carbon.
An immediate focus for housebuilders has been the introduction of changes to Part L 2021 of the Building Regulations, meaning many are now looking for the simplest and most cost-effective way to meet the new carbon reduction obligations.
To make significant contributions to energy efficiency and sustainability progress, housebuilders can be supported in additional ways alongside emerging renewable technology systems, such as with window and door solutions. At Eurocell, we already have our Modus system, which is Future Homes ready and continues to lead the market.
Removing the need for complex and expensive glazing specification, Modus, helps to lower the cost and impact of tackling the net zero carbon agenda for housebuilders and homeowners.
Crucial in the journey to achieving net zero is a holistic approach from inception to completion, and forward thinking planning for how the end user will use the space. This means window and door solutions that not only meet the Future Homes Standard, but also exceed the usage requirements of the house buyers for years to come.
Key benefits from using effective window and door solutions to deliver energy efficiency include:
Use of energy efficient materials
From manufacturing right through to installation, effective window and door products require less energy and provide opportunity for recycled material use.
All Modus main profiles feature a minimum of 36%* post-consumer recycled PVC-U as standard. This helps to achieve a lower carbon footprint compared to products made or containing recycled material sourced from outside of the UK. The system deploys cutting-edge dual material extrusion technology (DMET) which layers post-consumer recycled and ‘virgin’ material simultaneously with high precision. The recycled material is concentrated in the central core of the profiles, where it is completely invisible in an installed window or door.
Reduced air leakage
Designing with better insulation materials and techniques can reduce heat and air leakage, resulting in less energy required to heat or cool the building. Modus is proven to deliver thermal insulation excellence, as well as air tightness and noise reduction benefits due to the uniquely designed 75mm six-chamber profile system which can achieve very low U-values with triple-glazed units.
This improves the energy efficiency of a building as a whole because energy is being stored appropriately throughout the seasons, thus reducing the need for constant heating and cooling management. Altogether making the decision to install energy efficient window and door solutions particularly appealing for house buyers.
Durability and longevity
When products are designed to be more durable, this increased lifespan extends the benefits of lower energy consumption to also reduce the need and cost of labour for replacement.
A key consideration when creating durable, long-lasting products is visual appeal to reduce product lifecycle when tastes or modern functionalities change. Creating timeless but contemporary designs are vital to allow the sector to build the homes people want to purchase and live in.
For more information, please email newbuild@eurocell.co.uk or visit our website eurocell.co.uk
*Average % recycled material of main profiles content varies by component from 36% to 72%