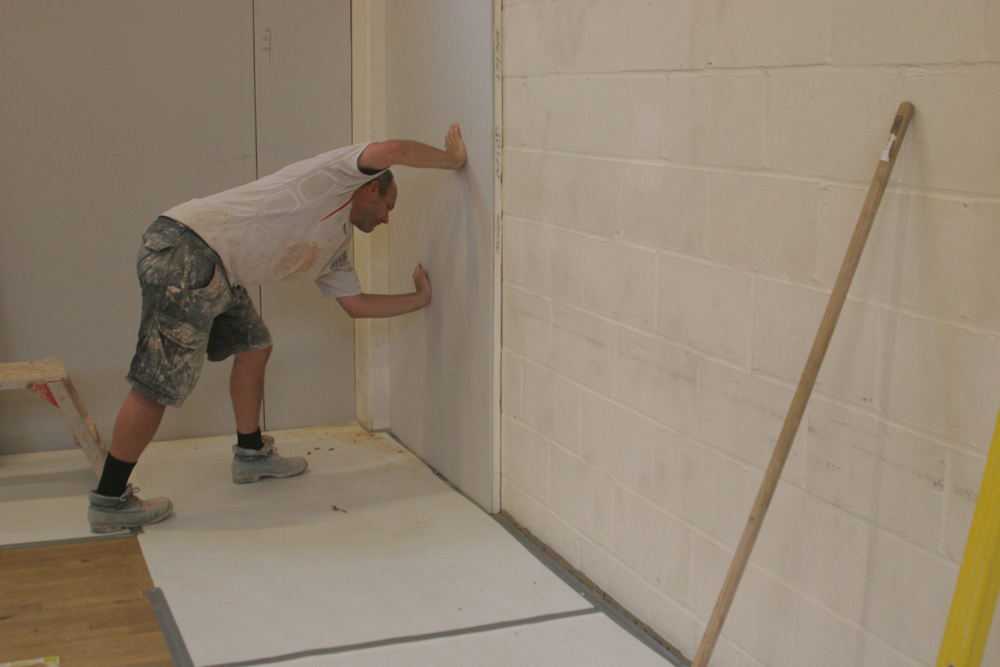
Roger Bisby takes a look at plasterboard and wonders how it got so complicated.
When I started in the building industry there was only one type of plasterboard which made it fairly easy to select the right one. Now we have square edged and tapered boards up to 10 feet long, moisture resistant board, fire resistant board, vapour check and acoustic board. You can also get GRP reinforced board for impact resistance, Glasroc sheathing board for up to six months’ weather protection and Habito board which takes a screw directly without plugs or anchors. There are also now specialist tilebacker boards based on gypsum, cement and foam core.
The problem for the jobbing builder is that once you get your head around what is available, you’ll find that a great many of these boards are special order only and if you order them you need to order a pallet load. So even though the theoretical choice is wider than ever the practical choice in most merchants is between white, pink, blue and green, foil backed vapour resistant and thermal laminates. That is still a lot to choose from and a lot for the merchant to stock and, for the most part, it is enough for builders to complete an extension or a loft conversion while complying with the building regs.
Back in the day we had another way around the problem of no choice which was simply to upgrade the standard board. For example if you need a kitchen wall to take fixings for cabinets sheath out with OSB first and then clad it with 9mm plasterboard. This also works very well if you need impact resistance.
If you want vapour check you can use a polythene vapour barrier before you put the boards on. If you want fire resistance you can double tack with staggered joints and a skim coat. If you want moisture resistant board you can apply a paint-on membrane or tanking kit. All these option comply with the Building regs under the catch all phrase “or by other means no less effective”.
The other problem that appeared seemingly out of nowhere is getting rid of plasterboard. Although gypsum on its own is harmless, when you mix it with methane from organic waste it sets off a reaction that produces hydrogen sulphide gas which is poisonous, corrosive and flammable. As a gas you don’t want in landfill, this ticks all the boxes and it means that all plasterboard sent to landfill needs to be segregated from the organic waste. If you dump it in your skip then the skip company will charge you extra, if you try to get rid of it yourself you will find very few waste transfer stations that will take it. At my local tip they charge £7.00 for a small polythene sack. One trick I see done a lot these days is to dump the offcuts inside the stud walls but this is only good for small amounts. On larger sites the plasterboard manufacturers provide skips to recycle the board. The good news is that plasterboard is 100 per cent recyclable, all we need to do is work out an economic way of getting it from site to factory. In the end, as with so many things in life it is really just a question of who pays.