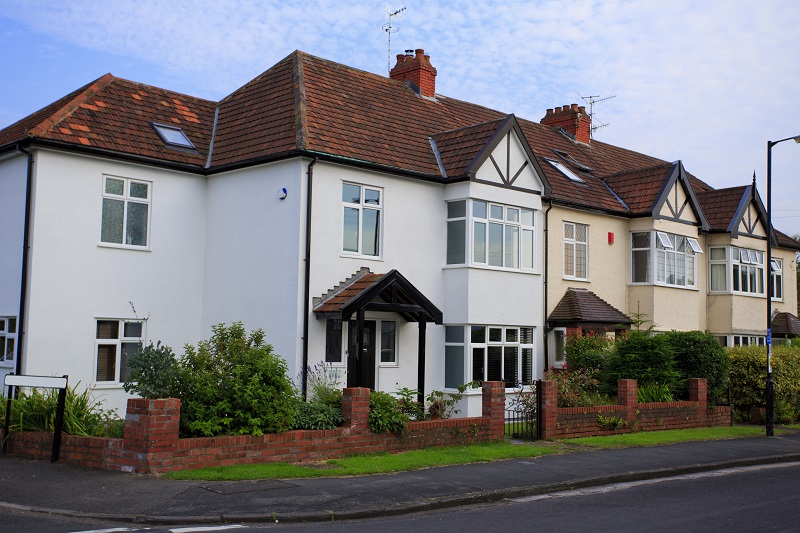
In the second of our series, Hudson Lambert of Safeguard looks at houses built in the interwar years – 1918 to 1939 – and describes some of the construction details that can give rise to damp and other problems nowadays.
War is always a time of great transformational change, whereby – among all the death and destruction – human knowledge, understanding and technology comes on leaps and bounds.
The First World War was no different – indeed, more ‘transformational’ than many before or since. Housebuilding techniques and detailing too evolved in the immediate post-war period, especially given the huge drive to provide ‘homes fit for heroes’ for thousands of returning combatants; and the explosion in then-new ‘social’ housing.
The Housing Act of 1919 resulted in the completion of over 200,000 homes in the few years after the war – a huge number given the population then, and a number we apparently could do with annually now. And councils themselves built 1.1 million homes in this interwar period.
Among the new building techniques deployed were three that would have an immediate impact on damp problems; but also store up problems for the future.
First was the widespread adoption of cavity walls. Not only did these improve the thermal performance of housing, they would also help mitigate the issues arising from penetrating damp caused by heavy, wind-driven rain.
Second, it became standard to incorporate a damp-proof course (DPC) into wall construction, reducing the likelihood of rising damp.
And finally, builders started to use concrete strip footings – rather than purely brickwork – and slabs at ground level. This helped improve masonry resilience against ground movement.
Window shape, design and materials also changed in this period, reducing – but not eliminating – the potential for brickwork cracking owing to building movement and the general lack of lintels. So far so good: so what could possibly go wrong in buildings of this age?
First is DPC failure. Older DPCs tend to be bitumen based and deteriorate with age – allowing ground-water to rise through as bricks and mortar. Likewise, the concrete slab is unlikely to be separated from the structure by a damp-proof membrane, and so damp problems can result in masonry and timber floor elements.
With rising damp closely associated with hygroscopic damp – caused by the introduction of ground salts into a wall, decorative spoiling is likely alongside the other negative features of rising damp such as reduced thermal performance and dilapidation of the building fabric.
The introduction of new DPCs – using treatments such as Safeguard’s Dryrod – to prevent further dampness rising from the ground is now straightforward; and new salt-resistant plasters take care of any issues associated with plasters contaminated as a result of hygroscopic damp.
If the DPC has to be installed above suspended timber floors, a brush-applied damp-proof membrane, such as Safeguard’s Drybase DPM, could be applied in the floor voids – after removing and/or treating any vulnerable timber. If that is not possible, then treat the timber as far as possible and add ventilation where appropriate.
Cavity wall problems depend on a few factors: Is the external masonry and mortar in poor condition si.e. cracked or lost, thus permitting more ingress of rainwater? Is cavity wall insulation (CWI) installed and are wall ties galvanized or not?
Wall tie replacement is beyond the scope of this article, yet concerns regarding CWI need addressing.
CWI can be an effective way to save energy. However, when installed into unsuitable walls (such as those in exposed areas with porous brickwork), it is at risk of failure owing to penetrating damp, causing dampness to appear inside the walls and a reduction in its insulating qualities.
If it is completely sodden and has slumped to the bottom of the cavity, the only feasible option is removal.
However, if it isn’t overly saturated a breathable masonry protection cream treatment, such as Safeguard Europe’s Stormdry, applied to the outside face of the wall will allow it to dry whilst blocking out any further moisture.
You will also need to re-point any badly degraded, eroded or cracked mortar first. By allowing water vapour to escape whilst preventing moisture, such as penetrating rain or excess surface water, from seeping in Stormdry ensures that walls continue to dry out after they have been treated.
Other problems are the same as in the pre-1918 houses discussed last month. Suspended timber floors are at risk of decaying joists etc as a result of compromised ventilation; and masonry cracking around window reveals as a result of building movement.

Make sure that new works do not interfere with sub-floor ventilation and, where previous works have, ensure that it is reinstated.
Where masonry has cracked, a crack-stitching system – such as BrickFix – can be used to reinforce the existing mortar beds. If you suspect the cracking is linked to subsidence rather than the natural building movement you should always enlist a specialist.
Next week we’ll look at houses built after WW2 and the issues that can arise with them, again as a result of the evolution of house-building techniques in a post-war environment.
For further information on Safeguard Europe click here.