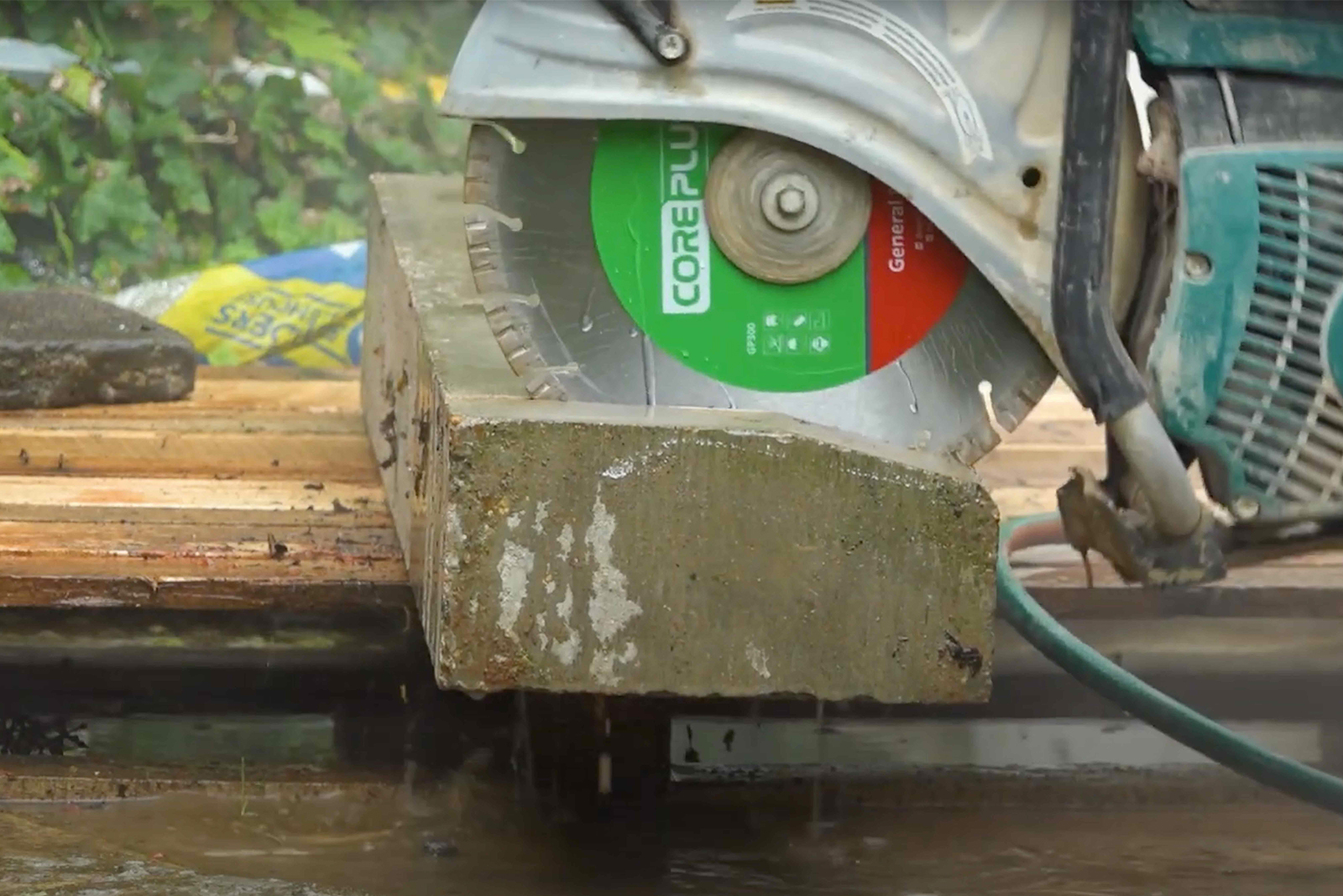
Brian Trevaskiss, Marketing Manager of CorePlus explains how to choose the right diamond blade for the job.
Selecting the right diamond cutting tool can be confusing. Products that look the same with overly complicated naming can mean you choose the wrong tool for the job, wasting time and money. However, there are some basics to understand when it comes to choosing the correct product which are worth knowing. For instance, correctly identifying the material you’re going to cut is the most important factor in choosing a blade.
Blades for cutting hard, dense (less abrasive) material such as tile, hard brick, stone or hard-cured concrete require a softer metal matrix bond – these wear faster, replacing worn-out diamonds fast enough for the blade to keep cutting.
Blades for cutting soft, abrasive materials such as block, green concrete or asphalt require a hard metal matrix bond to resist abrasion and hold the diamonds longer. As a general rule, determine the material that will be cut most often, or the material for which top blade performance is most important.
Before you get started also decide which is most important to you – the initial price of the blade, or the cost per cut. For smaller jobs, or occasional use, a low-priced blade may be preferable. For longer jobs, or regular use, a higher priced blade will actually be less expensive to use because it will deliver the lowest cost per cut. For really big jobs, the lowest possible sawing cost (cost per meter) is usually much more important than the initial price.
There are advantages and disadvantages to both wet and dry cutting. Wet cutting will keep the blade cooler and will significantly extend the blade life. Wet cutting is the most cost-effective method but is not always safe or practical. When using an electrical power hand saw, it is not safe to use water without an appointed safety rated accessory system.
The advantages of dry cutting are that no water supply is needed and does not require specialist equipment such as water spray systems and cutting can be done near electrical equipment. Also, there is no water damage to the environment.
The disadvantages are that dry cutting can only do short shallow cuts to keep blade cool. A large amount of dust generated, causing a premature wear of equipment and generally it leads to a shorter blade life and slower overall cutting speeds.
Clear packaging
When we developed the CorePlus range, we recognised that choosing a Diamond Cutting Blade should be made a lot simpler. The range has specially designed packaging that makes it easy to match the right diamond blade to the job in hand and therefore making it easier to choose at the trade counter. Trade users need simply look at the packaging and it clearly shows them the type of jobs it will do and blade life they can expect. The simple star rating displayed on the back of each blade pack clearly indicates how the blade will perform. For extra simplicity, when long blade life is the key selection criteria the ‘Elite Endurance’ mark provides the maximum number of cuts for your spend.
Essentially, CorePlus matches user-friendly, no-nonsense packaging with high quality diamond technology which we believe will make the range a success for tradespeople.
Safety
Impressive safety and quality standards are integral to the range and the products are manufactured with state-of-the-art production technology. All our diamond cutting blades are manufactured to EN 13236 and our Elite Endurance range meets the additional certification standards required by oSa the German Organization for Safety of Abrasives.
Whilst quality and concentration of diamonds is an important factor in cut precision, the bond matrix that delivers the diamond is just as crucial. Our bond technology has been developed by the metallurgist professor at the University of Sheffield here in the UK and is specially formulated for different substrates.
For more details on the CorePlus range visit https://core-plus.co.uk