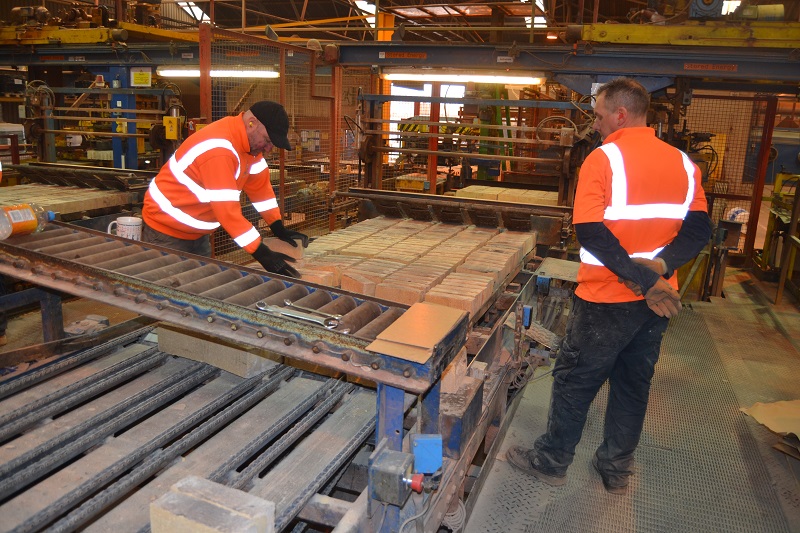
As Ibstock prepares to more than double its capacity at its Leicester brickworks, Professional Builder Lee Jones visits a manufacturing facility that has helped to build Britain since 1825
With over 80 per cent of all new houses in Britain built with it, the humble brick is such an integral part of our built environment that we are often in danger of taking the variety to be found in its colours and textures for granted.
If the material is a national treasure it is also an inherently local material. The variations in clays from region to region yield distinct shades and surface characteristics, which provides the buildings from which they are constructed with their local vernacular.
Ibstock’s Leicester site alone has a range of 23 different bricks, but add to that the increasingly popular blends produced, and the choice is virtually unlimited.
The nation’s largest brick manufacturer – currently supplying approximately 800 million bricks a year – also boasts the biggest range, at more than 450 across its 19 factories, but even that figure doesn’t include the company’s long bricks, or its glazed examples.
It is substantially increased demand from the building industry that is driving huge expansion, as the company’s Marketing Manager, Andrew Halstead Smith explains: “Ibstock Leicester is currently producing around 90 million bricks annually, but the significant investment in a new factory adjacent to our existing plant will see that capacity more than double, with a further 100 million leaving the gates by late 2017.
“UK brick production currently stands at a little less than 2 billion a year, whilst we import around 300 million, but the industry as a whole is presently in optimistic mood – these are exciting times for us and we expect that figure to rise in the years ahead.”
The Leicester Red Stock, which derives its distinctive colour from the local clay, is an iconic brick in the construction sector. The colour is dependent on a particular clay’s iron content, and the Ibstock pits are unique in that they will also yield cream and yellow bricks and, with more than a 100 years of clay reserves still available, there’s enough to keep the fires of industry burning for the foreseeable.
As the location that gives the company its name, the Leicester site is deeply embedded in the brick manufacturer’s DNA. Now the head office of Ibstock PLC, bricks have been made here since 1825, but the same ground also bore witness to a landmark of the industrial revolution. Even before the brick maker’s tenure, a colliery existed on the site, and one of the nation’s first railways was built to transport the coal.
It quickly became apparent, however, that the quality of the coal mined in the region could not justify continued production, but it was equally discovered that the harvesting of its clay shales and pits would yield a superior building material – and so Ibstock Brick and Tile was born.
Today, Ibstock Leicester is at the heart of a factory network that spans the length and breadth of the British Isles, from Swanage in Dorset up to Newcastle-upon-Tyne.
“Utilising clays from around the country is very good for us,” continues Andrew, “because it means we are not restricted to a narrow portfolio of colours or textures. We could sell a Throckley brick from the North East into a project in London, for instance, because it has a certain texture and colour that the builder or developer is looking for.
“Brick has an unparalleled ability to add detail and character to a building and it’s becoming increasingly fashionable to seek out unusual grey, black and metallic colours, and with the bespoke blends that we also provide you can actually create a very distinctive design without incurring much cost.”
The Ibstock website features a useful tool where those blends can be visualised and experimented with, whilst a staggering 150,000+ samples are distributed to customers each year.
Experts at the factory ensure that each sample is fully representative of what will be supplied, and if a customer submits an order to this completely free service before 2.30pm they will receive that sample the next day.
Dig it, burn it and sell it – that’s how brick makers have often characterised the simplicity of the process that produces their finished product, but that particular turn of phrase hardly does justice to the scale of the operation and range of product.
The stock brick is an ancient building material and the specials department makes use of centuries-old handmade techniques. The clay is ground with water and a plasticiser.
The material is then roughly shaped, rolled in sand and that lump, or ‘cloth of clay’ as it is more properly known, is
then thrown into a mould and cut to size.
In order to reduce the moisture content, brick laden carts are then loaded into a drier for three to five days. The bricks then spend up to a further three days in a kiln at 1,000°C+.
As a natural material clay has variations in its properties which makes brickmaking part science and part art. Every brick has a recipe, and a particular setting pattern of bricks on a kiln cart will alter the colour of the finished product.
Different clays will also burn differently, which means the temperature of the kiln has to be strictly controlled.
In the main production plant it is machines that take the place of these traditional techniques, but this totally automated process is essentially a mirror image of handmade brickmaking – but on a greatly increased scale.
Clay from the pits is feed to a huge miller, which utilises two steel rollers to grind a clay, water and clay conditioner mix ever finer, it is then roughly shaped, forced into a mould, and then subjected to the same drying and firing process.
Once newly made bricks have been shaped and fashioned by machine, the first human hands to touch the finished product will be the bricklayer, and with more than 23 million held in stock there’s certainly enough to satisfy their demands.