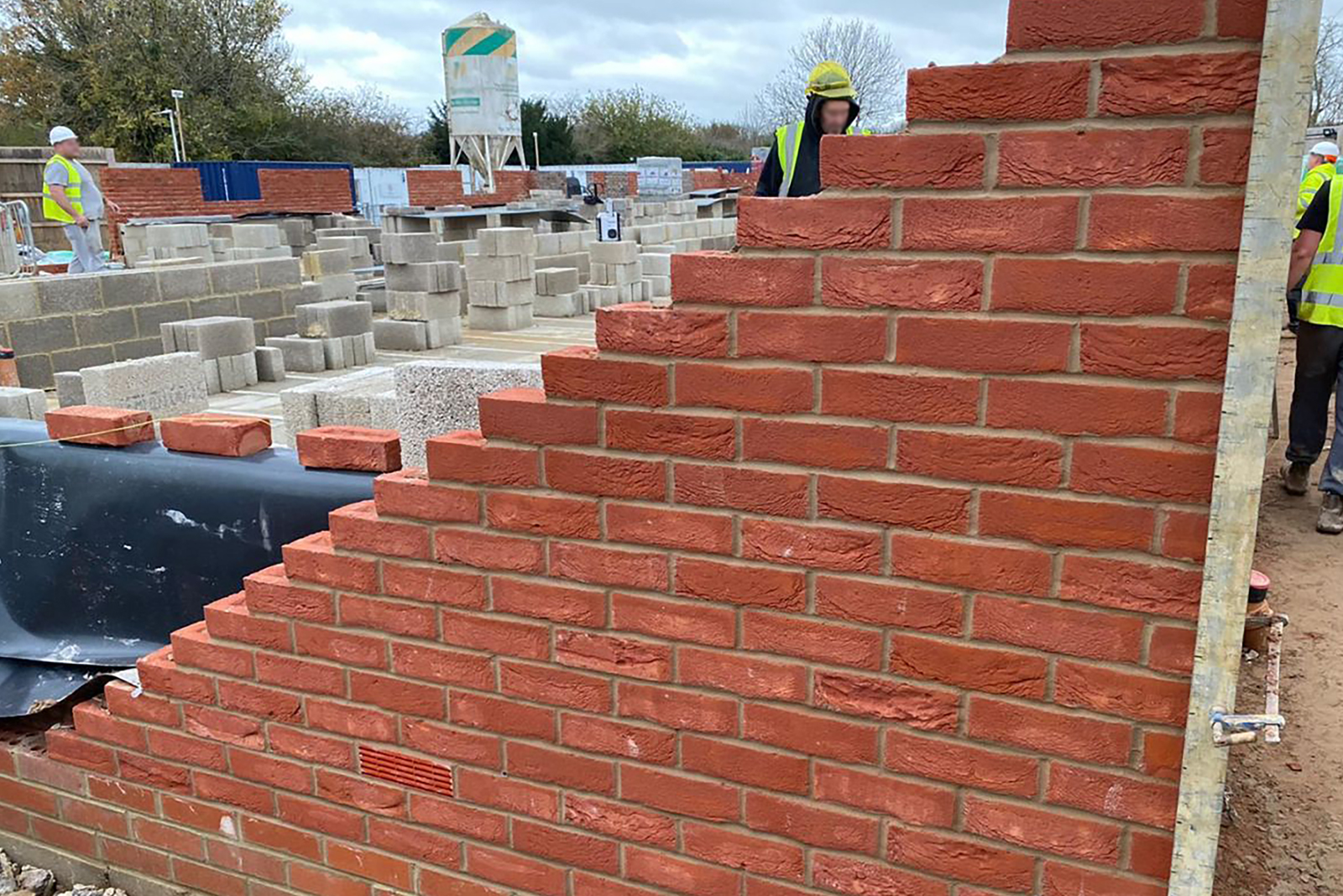
Sean Wilkins, Technical Manager at the Brick Development Association, looks at the differences between clay and concrete bricks.
The UK has a long history of using bricks and mortar in housing, since the process of firing clay was first introduced by the Roman Empire. Almost 80 per cent of new homes built in the UK are made from bricks and they provide a reassuring sense of security, beauty, and durability for the inhabitants. To most people a brick is a brick but look a bit deeper and the huge variety of colours and textures becomes clear. Historically bricks would have been made on, or very close to the construction site. Even in the modern-day, bricks average less than 70 miles from the manufacturing location to the site. Over 90 per cent of bricks manufactured in the UK are made from clay, which is shaped, dried, and fired in a kiln to create a hard and durable product. The small remaining section of the market includes bricks made from other materials, the largest of which is concrete bricks.
Concrete bricks are made from sand and aggregates, that are mixed with pigments and cement to harden into a concrete block. Concrete bricks usually imitate the appearance of classic clay bricks, which can cause issues because some of their behaviour is quite different.
It is important that designers and builders are fully aware whether they are using a clay or concrete brick for the following reasons:
Movement
The requirement for movement joints in concrete brickwork is 6m, compared to 12m in clay brickwork. This is especially important for low rise residential construction as the use of concrete bricks will almost certainly require a movement joint, where none would be required for clay. Concrete bricks tend to shrink in the long term and if there is no allowance for this movement then it can lead to cracking.
Speed of construction
Concrete bricks tend to have lower water absorption and higher denser than clay bricks. These characteristics are important because it can limit the number of bricks that can be laid in one day. Generally, the labour cost to lay bricks is the larger part of the total cost, compared to material costs. Site trials have shown that concrete bricks are around 30 per cent slower to lay because fewer courses can be completed in a single day, before mortar starts squeezing from the lower joints. The increased labour time can lead to a higher-than-expected overall cost with concrete brick.
Longevity and value
Clay brick has been used in the UK for thousands of years so there is a large body of evidence to show that clay brickwork will last for a minimum of 150 years, with many clay bricks lasting considerably longer. Concrete bricks are a more recent product and there many examples from the 1980s and 90s where the pigments have leached from the brick, resulting in a dull grey concrete appearance. One of the reasons that clay brick property retains value is that they tend to weather and age in an attractive way, making it easier to secure lending and insurance decades after construction.
Conclusion
When looking in a bit more detail it becomes easier to see the visual differences between clay (right) and concrete (left) bricks. The colour in concrete bricks come from pigment added to concrete mix, rather than an inherent property of the raw clay material, so they tend to have the appearance of coloured concrete.
It is easier to differentiate clay and concrete bricks when they are of a single colour because the surface texture is more obvious. However, it can be difficult to identify concrete bricks when they have had secondary processes applied during manufacturing. Secondary processes can include ‘rumbling’ to round the edges, which replicates the effect of moulded clay stock bricks. Also, dyes can be applied to concrete brick surface to mimic the dark spots and patches that are created on clay bricks during firing in the kiln.
The only way to be certain of which type of brick you are buying is to ask to see the data sheet attached to the brick. All clay bricks sold in the UK must carry a CE (soon to be UKCA) mark, which means they are assessed against the product standard BS 771-1. Concrete bricks tend to be assessed against the concrete block standard BS 771-3, which has different requirements for the declaration of performance.
To ensure that you maximise the benefits that we associate with historic brickwork it is important to look a bit deeper and not to assume that a ‘brick is a brick’.
For further information on the Brick Development Association visit https://www.brick.org.uk/