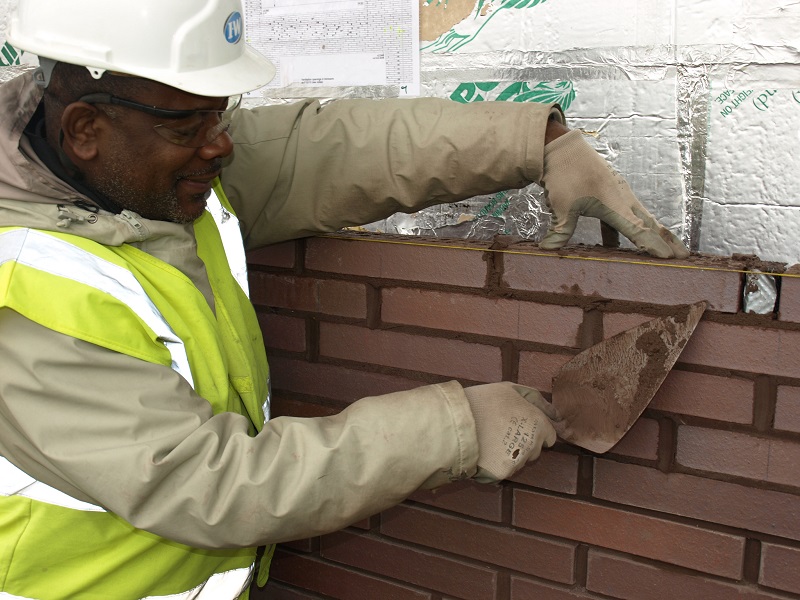
There are many things that a bricklayer must do to ensure that the job he is working on not only looks good but also meets industry standards. One of these tasks or competencies is the blending of brickwork. The Brick Development Association’s CEO, Andrew Eagles explains all.
Clay bricks and pavers have come a long way from basic creams and reds available in the 60’s and 70’s, to a diverse range of colours and textures manufactured in a very scientifically precise manner, through modern brick plants and machinery.
Due to these changes, successfully pulling off extensions in this kind of work can be a challenge, and projects can look unintentionally different from the original section of the building. Thankfully, there are ways around the potential pitfalls contractors can experience when blending brick.
Matching bricks can be complicated as there are several factors to account for: colour, size, texture and bond pattern. This task is best done in partnership with a brick manufacturer, who can help to select and supply the closest match, not just at the present time but also in future in the face of potentially difficult weather conditions for the brick.
When sourcing brick, it is usually better to use traditional handmade bricks over second-hand ones. Replicating the bonding pattern is often the best approach in this kind of construction work.
Older, solid walls were laid in the Flemish bond pattern, which showed the headers of the bricks. Currently, bricks are laid in what is known as stretcher bond, with two separate walls, each 4 inches thick, with a cavity in the middle. To replicate Flemish bond in a cavity wall, you will need to purchase ‘snapped headers’, or half bricks.
You must take into consideration when calculating brick numbers that bricks are now measured in metric units, rather than imperial, unlike their older counterparts. Standard bricks are now 215×102.5x65mm, compared with the slightly larger past bricks, which were 228x110x68mm.
It is also important to factor in a 10 per cent wastage margin, considering spacing for mortar joints, which should be 10mm for an average-sized stretcher bond.
When blending bricks, there are a few tips worth remembering. When handling the bricks on site, care should be taken to avoid chipping and damage.
When bricklaying is not in progress, bricks should be protected from external elements such as bad weather. Packs should only be opened with sharp band cutting tools. Use of a lump hammer and bolster to break the bands is not advisable as it can cause chipping, breakages and potential collapse of the pack.
When it is possible, when working on brick projects, you should take receipt of as many bricks as possible at an early stage to ensure maximum colour consistency throughout the build. The nature of fired clay is that the exact colour can fluctuate between different batches.
To avoid the colour banding or patching that can affect the final project, making sure the bricks are well blended is imperative.
It is important to ensure that bricks are blended well with other packs, preferably at least three. If possible, overlap between deliveries should be arranged to maximise variation, and minimise the possibility of colour separation or banding on the brickwork.
Different manufacturers will have factory specific opening instructions for optimum blending, and it is best to follow these as closely as you can.
Although brick manufacturers will carry out as much blending as possible at the factory, there is no substitute for blending on site. Using at least three packs is the best way to avoid any colour banding, especially by using batches from different deliveries to maximise diversity between bricks.
Additionally, changes in mortar need to be taken into consideration. The best approach is to copy the joints on the existing house.
A sample of the existing mortar should be taken to a local lime supplier and they will be able to give advice on the best match for the project.
If the original section of mortar is in need of repair, the whole building can be repointed. Although this sounds like an inconvenient option, it will ensure consistency across the project, where it is easy to make mistakes when trying to match the mortar to an original.
If the original section of building is in good condition, matching the mortar is a cost-effective option, and a good mortar specialist will guide you through and help to select the most suitable match for your project.
Careful blending and product knowledge will effectively reduce the need for rectification work. It is also a reflection of the saying about better tradesman – “know your tools, know your product!”
For more information click here.