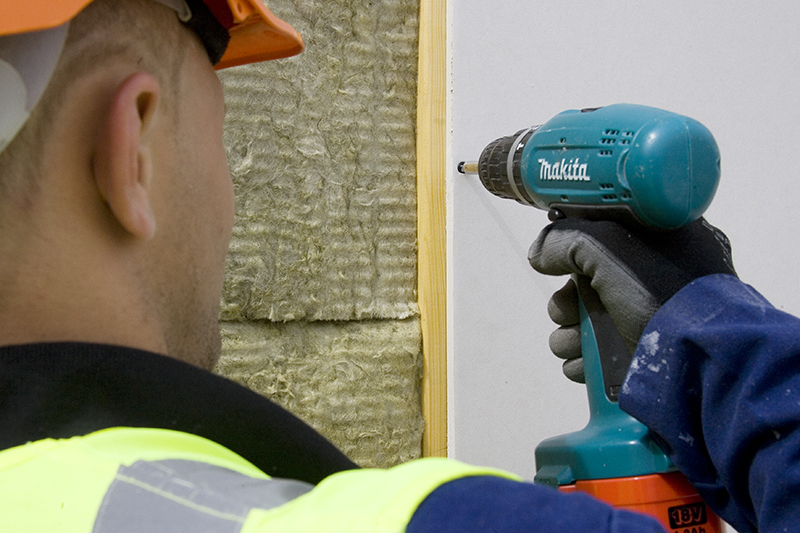
Every type of insulation needs to be fitted correctly to work effectively. We speak to the Rockwool technical team to discover the installation issues that often result in profit-draining call-backs for builders.
Cold bridging
The most common example of insulation issues that we come across is when builders have forgotten about cold bridging at key junctions. Taking a bit more time to review areas where cold spots may occur, such as window junctions or junctions between wall and floor or wall and roof – will save you time and money in the long run.
It doesn’t take long for homeowners to notice the cold and if you don’t nip it in the bud early, these junctions are where damp can get in.
Planning for thermal bridging involves thinking beyond the job in hand and taking note of the whole home. Second nature to a seasoned builder, you might think, but always worth double-checking if, for example, the apprentice or someone less experienced has worked on the loft.
Have they remembered to insulate over the rafters, before the storage boards go down? It seems obvious as the rafters give a direct flow for cold bridging into and across the building. Up to a third of heat escapes through the roof, so a small oversight from someone less experienced can have a big impact on the home.
Seal the edges
Perimeter edges around ground floors, especially those connected to external walls, and junctions around window frames are common areas where cold spots can occur. Adding some edge insulation around ground floors and ensuring cavity closers are used around lintels, sills and jams will go a long way to solving this issue. Installing the correct thermal insulation, like Rockfloor and Rockclose, can help to reduce cold bridges at these points and prevent damp which can occur where warm air and cold surfaces meet.
Ground temperature
Double-check the ground floors too, again, especially ones that link to external walls. We often see call-backs relating to cold ingress at these points. Ground temperature and the internal house temperature can vary dramatically, offering another path where the perfect storm of hot and cold collide and damp can get in. Having high thermal density insulation, such as, Rockfloor, at this point is critical.
Mind the gap
Small gaps in the insulation can also cause issues. Not ventilation spaces, but those small gaps where the insulation cut is uneven or too short. These gaps, no matter how small and inconvenient they may seem, allow for cold air to get through the building fabric.
It’s an easy fix with Rockwool. Take small pieces and plug or fill the space, before you cover it up with membrane or plasterboard. As a general rule of thumb, when working with Rockwool, it is best to slightly oversize your cut. The flexibility of the product and its patented ‘flexi-edge’ design means it will give you a secure ‘friction-fit’ to hold itself in place, with no need for secondary fixings. However, cut it too small, and there is not enough product to hold itself in place within the the timber or steel frame.
Let it breathe
We often see sites without adequate ventilation in a loft, or, even worse, areas where DIYers don’t understand the importance of ventilation and block it up! This can cause significant damage to the building fabric, and no one wants the headache of a loft-related, structural call-back.
Spread the knowledge
If your customer asks you to fit their insulation in the loft but you think they’re planning to board it over themselves later, then offer them some free advice.
Sometimes it’s just a case of reminding them that if they do choose to fit the boards themselves, they must not cover the ventilation gaps nor should they uncover the rafters. Remind them that they should get the right risers to support the boards, so they don’t compress the insulation which will restrict its thermal performance.
Giving free advice might seem counter-productive but you don’t want the call back if they let damp get in and have no ventilation. Plus, if you detail the issues and the potential pitfalls, they might reconsider the effort involved and ask you to complete the job for them.
Support is at hand
We always recommend keeping up to date by using the Accredited Construction Details from the Planning Portal. They offer a fantastic source of clear, easy to follow information to help you explain the complex nature of your job to your customer.
Also, to support you further, Rockwool has a suite of technical tools online to help you work out everything from the quantity of insulation required to U-Value calculation.