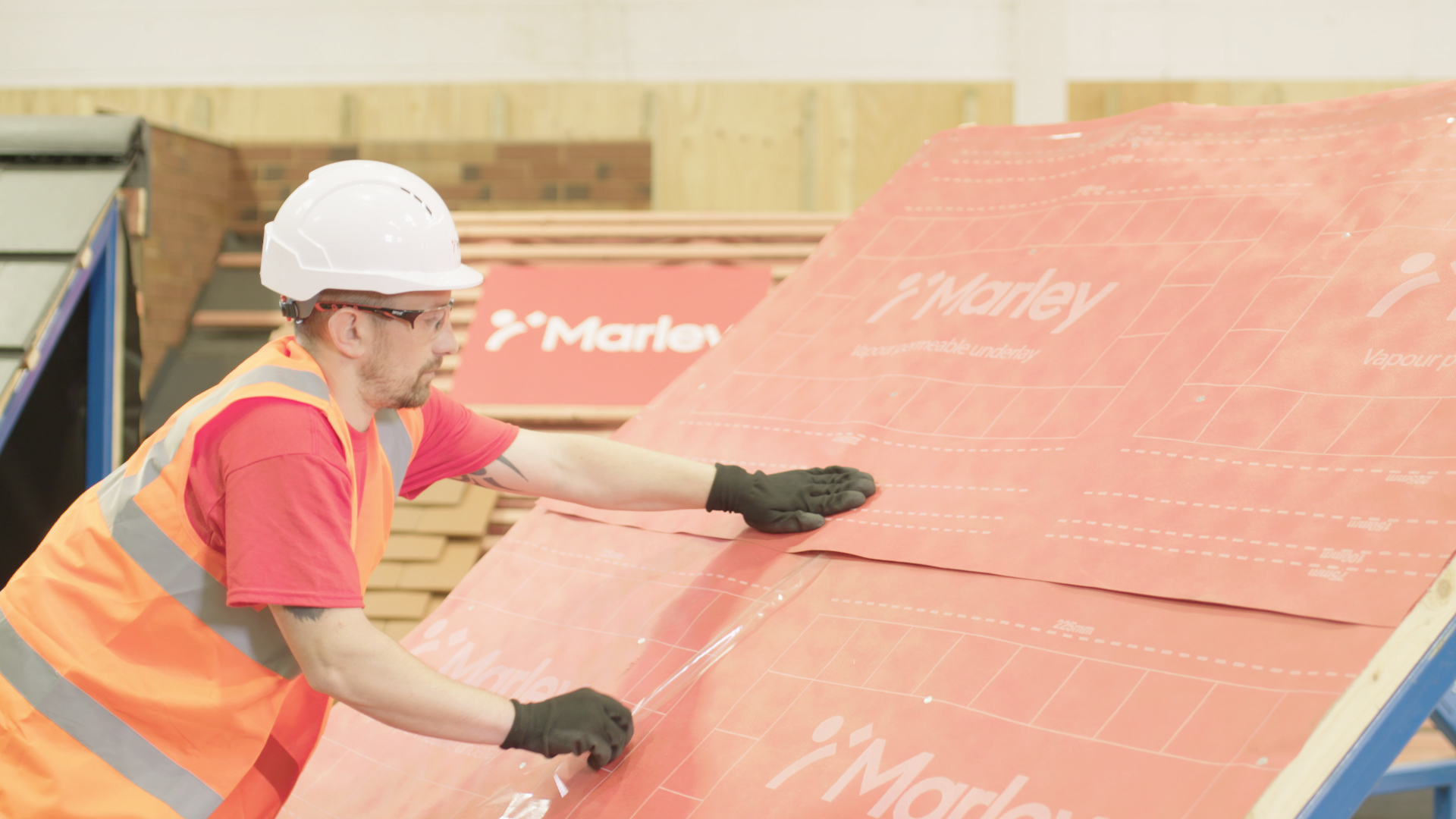
Stuart Nicholson, Director of Roof Systems at Marley, looks at the steps contractors can take to ensure roof ventilation is fit for purpose.
Moisture in the form of condensation can develop on the underside of roof tiles and slates, as well as the roof underlay, causing droplets to form in the batten void and roof space. This can cause damage to timber battens, rafters, fixings, and insulation, not to mention any possessions left in the loft. In the worst cases, the build-up of condensation and moisture can be so severe that it penetrates the ceiling, causing damage to the rooms below.
If condensation is not dealt with, it can lead to damp and mould which not only has the potential to affect health but can also cause significant and expensive damage to a property.
By assessing five key points to ensure roofs are ventilated adequately, contractors will be able to tackle the issue of condensation and prevent future issues.
- Adhere to Standards. Always comply with BS 5250:2011+A1:2016 ‘Code of practice for control of condensation in buildings’ and BS 9250:2007 ‘Code of practice for design of the air tightness of ceilings in pitched roofs’. This means that a cold roof should have a minimum of 10mm continuous ventilation at the eaves and 5mm continuous ventilation at the ridge. A breathable or non-breathable underlay can be used, but make sure there is the right amount of high- and low-level ventilation to prevent condensation. This can be achieved using an array of solutions, including eaves ventilation, ventilated dry ridge systems, ridge vents or multiple tile vents.
- Understand ventilation. The most frequent ventilation problem is caused by relying purely upon a breathable membrane for ventilation. The term ‘breathable’ underlay is often misunderstood because it suggests that ventilation is not required. However, the British Standard BS 5250, ‘Code of practice for the control of condensation in buildings’, does not consider the situation where it is proposed to provide no ventilation to the roof void. As such, roofs will always require some form of supplementary low- and high-level ventilation in accordance with BS 5250. This is also a tried and tested approach which avoids placing the heavy long-term burden of effective roof ventilation on one single element.
- Specify correctly. Ventilation is the sum of all its parts and should not be dependent on one single product or method. Like establishing a fixing specification for every project, it is advisable to do the same with ventilation. Marley offers a range of specification services including the appropriate choice of underlay and ventilation systems to ensure secure pitched roof fitting and the lowest possible risk of interstitial condensation.
- Check insulation levels. When increasing the loft insulation as part of a refurb project, check that ventilation has not been compromised as this can produce a condensation problem. If there is eaves ventilation, then it is important that the effective air path is not blocked. Where insulation at ceiling level is more than 300mm deep, then Marley offers the Universal Eaves Vent Plus system, which has a wider rafter roll and ensures airflow.
- Full pitched roof systems. Marley’s full roof system includes a wide choice of roof tiles or slates, as well as battens, underlay, ventilation, dry fix systems and fixings, backed up with a 15-year system warranty. This ensures the right level of ventilation and a guarantee of the quality and compatibility of all roof elements.
For further information on Marley visit marley.co.uk/