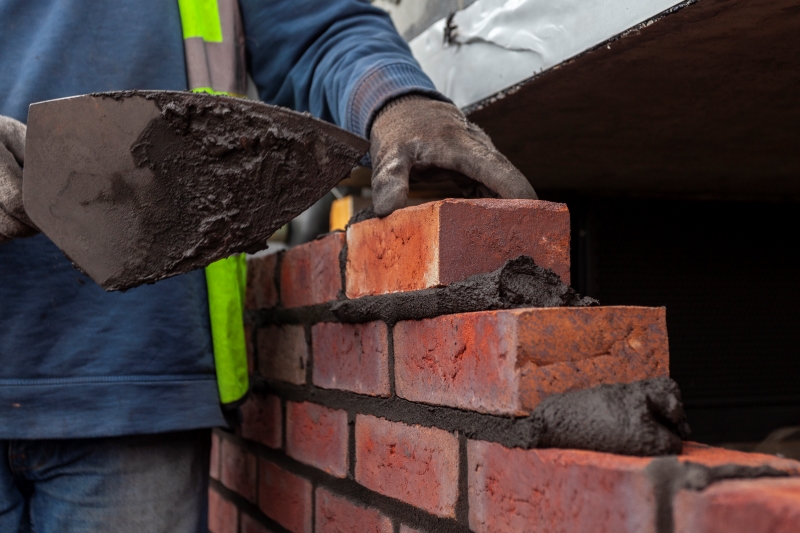
Victoria Elliott, National Commercial Manager, Cemex, offers some top tips on how to tackle and take advantage of lower-carbon concrete and cement …
Recent changes to product standards have meant that cement manufacturers are now able to supply a broader range of lower carbon cements in place of their traditional products. Amongst all the additional noise this has created, when it comes to helping builders make more practical and informed choices on all things lower-carbon cement, mortar and concrete, we’re keen to join the scrum with some straight-talking advice.
At Cemex, we know a thing or two about cement. In the Midlands, Rugby is synonymous with cement, as well as scrums. With a wonderfully rich UK heritage, cement has been produced onsite at Rugby since the middle of the 19th century. Under our careful watch, Rugby Cement has a comprehensive range of products which carry all the hallmarks of a trusted cement brand. The current Rugby plant is one of the largest in the UK producing 1.5 million tonnes of cement per annum.
Anyone who has attended our popular Rugby Heritage Open Days will know just how passionate we are about our industrial legacy and how it has evolved. Today, the development and introduction of our lower-carbon products in this innovative new space demonstrates our commitment to the cause – and plays a central role in the ongoing story of Rugby Cement in the 21st century and beyond.
Tackling Lower-Carbon Cement
In the UK, there are several types of cement available, but commonly you will find most bagged cement used by tradespeople are factory-produced composite cements (sometimes referred to by their technical classifications of ‘CEMII or CEMIII’) consisting of finely ground clinker mixed with other materials (additions) that often impart additional properties to the cement such as improved workability and enhanced resistance to chemical attack, for example from salts used for road de-icing and sulfates in certain ground conditions.
As a key component of cement powder clinker requires a lot of heat and electrical energy to produce and a lot of carbon dioxide from the limestone that makes up a large proportion of the clinker is released when the high temperatures needed to produce clinker are achieved.
The three most common additions used in cement manufacture and also sometimes in concrete are Ground-Granulated Furnace Slag (S) which is a by-product of iron, Limestone (L or LL), an abundant rock from the Earth’s crust and Siliceous Fly Ash (V), a residue from burning hard coal. Reducing the amount of carbon intensive clinker in the finished product by using additions to manufacture factory-produced composite cements reduces the overall carbon dioxide (CO2) attributed to the cement.
Vertua For Net-Zero Goals
We manufacture high-quality British cements using locally quarried materials and additions, in order to offer a wide range of bagged cement and cementitious products through our national network of Builders’ Merchants. We also supply customers with cement so they can serve the trade with a national supply of ready-mix concrete and precast concrete products.
In 2020 Cemex Readymix launched Cemex’s first-ever net-zero CO2 concrete, Vertua. This is now part of an extensive family of products that includes lower carbon cements, concrete, as well as aggregates, admixtures and mortar products. The Vertua brand covers five sustainability attributes: lower carbon emissions, increasing energy efficiency, saving water, incorporating recycled materials and optimising design. Any products that bear the brand must meet requirements for at least one of these sustainable attributes, with the benefits clearly and transparently presented for customers on a fact label. Our top of the range, high quality Rugby Premium Cement carries the Vertua label to reflect its lower-carbon status in this category.
Vertua Cement products are split into three groups based on the amount of reduced carbon compared to traditional. To qualify under the brand, Rugby Cement products must reduce CO2 emissions by over 25% compared to traditional Portland cements CEM I. This is achieved using high quality additions in the manufacture of cement and also by reducing emissions through the manufacturing process. In our Portland Cements range, Vertua Plus offers 25% to 39% reduced carbon emissions, Vertua Ultra 40% to 55% and Vertua Supreme, over 55% reduced carbon emissions.
The outlook for lower-carbon cementitious solutions is clearly a bright one. With the move towards net-zero, the demand for lower-carbon concrete products is set to dramatically increase, so by delaying more environmentally conscious decisions today, we are only putting off tomorrow’s goals. Now is a really good time to try! Start looking at what is available near you – and think about how you might line up and take advantage on your next project.
For more information on the Virtua range of low carbon products from Cemex visit www.cemex.co.uk.