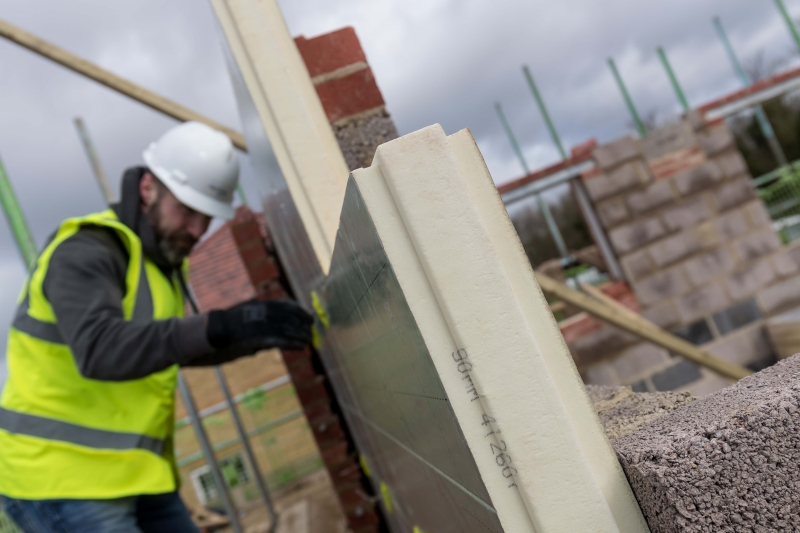
With the increasing focus on sustainability and reduced energy consumption, accurate U-value calculations have emerged as a vital factor for stakeholders including product distributors and builder’s merchants.
A U-value, also known as thermal transmittance, measures the rate at which heat transfers through building elements such as walls, roofs, windows, and doors. It quantifies the insulation performance of these elements and is typically expressed in watts per metres squared kelvin (W/m²K). A lower U-value indicates better overall elemental performance and reduced heat loss, with the insulation having a significant influence on its performance.
Additional Specification Considerations
For product distributors and builder’s merchants, accurate U-value calculations are crucial for recommending appropriate thickness of insulation products to their customers. By understanding the U-value requirements of specific building elements they can offer suitable materials that meet the desired energy efficiency standards. This ensures customers make informed decisions, leading to optimal thermal performance in their buildings.
However, thermal performance may not be the only product characteristic a designer has to consider when specifying materials to achieve building compliance. Thermal performance, moisture resistance, compressive strength, fire performance and a product’s environmental credentials may also be significant characteristics needing consideration during design.
Questions Arising from Product Substitution
When certain materials including insulation are substituted or ‘swapped out’ for often cheaper but inferior alternatives, compliance can be compromised. Therefore, it is crucial a designer is engaged throughout the reselection process. This is because product substitution poses some serious questions. For example, if the swapping out process leads to a substantial design change, will this mean an increase in insulation thickness? Furthermore, does the replacement product’s key characteristics, such as its testing and certification data, match the original material? Are the substitutions acceptable and the materials comparable?
Accommodating design changes with appropriately specified insulation materials is not only necessary for creating safe, comfortable, compliant homes, it could impact the UK’s net zero ambitions. Government statistics show that 35% of all greenhouse gas emissions originate from domestic buildings. It could be said, therefore, that accurate product selection in relation to a building’s redesign has a role to play in mitigating the effects of climate change.
Having asserted that U-values are not the be-all-and-end-all to appropriate product selection, their importance to achieving desired thermal outcomes should not be underestimated. Well-insulated homes minimise heat loss and assist in reducing heat gains in hotter months, resulting in reduced energy consumption and lower heating or cooling costs. Indeed, by adequately insulating their home, the Energy Saving Trust estimates a typical UK household can save up to £270 per year. Moreover, property owners can be satisfied that by achieving or exceeding required energy standards, they are safeguarding the long-term value of their investment and reducing the requirement for costly and disruptive retrospective property upgrade.
But it must be remembered that as valuable as they are to energy compliance, U-values are not the sole reason for specifying insulation that fits the needs of a particular building project.