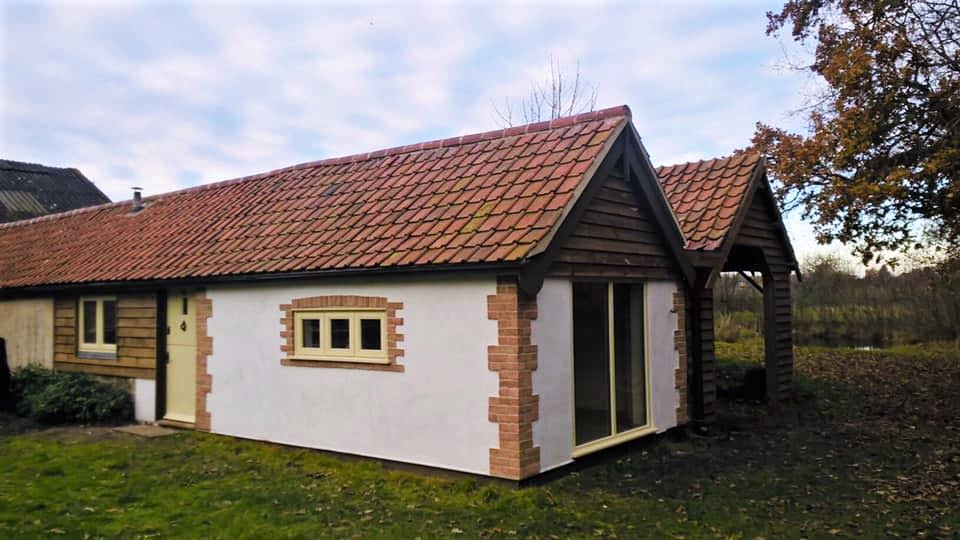
It is rare that a genuine industry first emerges, but Professional Builder’s Lee Jones talks to a manufacturer who believes he has developed just that – meet Jo Blox.
If you’re asked to devise a building system that requires no specialist skills, is quicker to install, better and cheaper than anything currently on the market, you might conclude that it would be a brief you’re unlikely to meet, but not so for Joe Orsi and his team at Roman Products.
As a historic buildings consultant, Joe is already an established authority in the demanding conservation sector and his company, Roman Products has since diversified into researching, developing, and bringing its own products to that market. It is all that experience that has been brought to bear in the development of the Jo Blox Structural Insulated Blocks. The Jo Blox journey began some five years ago, when Joe and his Norfolk-based team were approached with a project with ambitions to help the government hit its sustainability targets.
“We were asked by Sheffield Hallam University and UK Innovate to come up with a system that was better than carbon neutral,” he recalls. “Our starting position in our research was to look at Structural Insulated Panel Systems (SIPS), which are effective but do have their limitations. The units can be cumbersome to transport and crane into place, for example, whilst adapting them after installation is problematic.”
The quest to overcome these constrains would see a new concept emerge from the Roman Products drawing board – the Structural Insulated Block (SIB). “It’s one of those paradoxical situations where smaller units add up to quicker installation times,” enthuses Joe. “With individual blocks weighing as little as 5kg, they can be assembled quicker than a panel. It is a completely dry system, requiring no mortar, with pegs and screws used to fix the units into place. Airtightness is then provided by a vapour open polyurethane foam applied at the joints.
“The building industry’s skills crisis is now well-documented, and part of the original brief was to provide a solution that any of the trades, or a general builder, would be comfortable with, and that is exactly what we have delivered. In fact, from our own calculations, we found that a team of four could construct an average-sized bungalow in one day.”
Launched in March of 2020, the Jo Blox SIB is made of hemp, bound up with polyurethane foam, sandwiched between an inner and outer skin. The board material varies depending on application, and there are four broad types, with many more bespoke solutions on offer to suit customer requirements. For enhanced fire resistance, for instance, the Fire Assure block features an internal MagPly Structural Board, an insulating hemp resin core, and an external MagPly Fire Board. If you are looking to apply a lime render then choose Jo-Blox Multi Finish, constructed with an internal structural ply board, that same hemp core, and an external wood-wool carrier board. The whole system allows the building to breathe, which means that any renders applied need to be either Fibrelime or other premixed approved renders rated as breathable.
Of course, for any contractor the proof is in performance, and not only is it easier to install but in terms of carbon footprint, thermal performance, and compressive strength it outdoes any brick and block alternative. Hemp is a grown product, which locks up CO2 in its lifecycle, more than offsetting any other carbon emissions in the manufacture of the other materials included, whilst it’s sustainability credentials in the finished build are equally impeccable, as Joe explains. “We believe that this is the first system on the market that is totally decoupled, with not one single cold bridge to be found through a fixing or timber. As a consequence, U-Values and acoustic characteristics are superior and, having been tested up to 142kN without failure, its structural performance is phenomenal.
“The design brief we took up was about as tough as it got,” admits Joe, “and that’s why it took five years to deliver, but the next five and beyond are going to be very exciting. Since its launch we have been inundated with enquiries and we are in talks with a very major investor in the industry in order to significantly increase production. The blocks can be used in new build construction and are particularly well suited for extensions on historic buildings. On the latter projects, because they are so light, in many ground conditions foundations would not be required – only compaction. We’ve also had enquiries from holiday parks, for crisis homes and garden buildings and offices.”
For further information on Jo Blox from Roman Products, and if you’d like to watch a video of the product being installed, visit youtube.com/watch?v=65TXWyVJhH8&t=4s