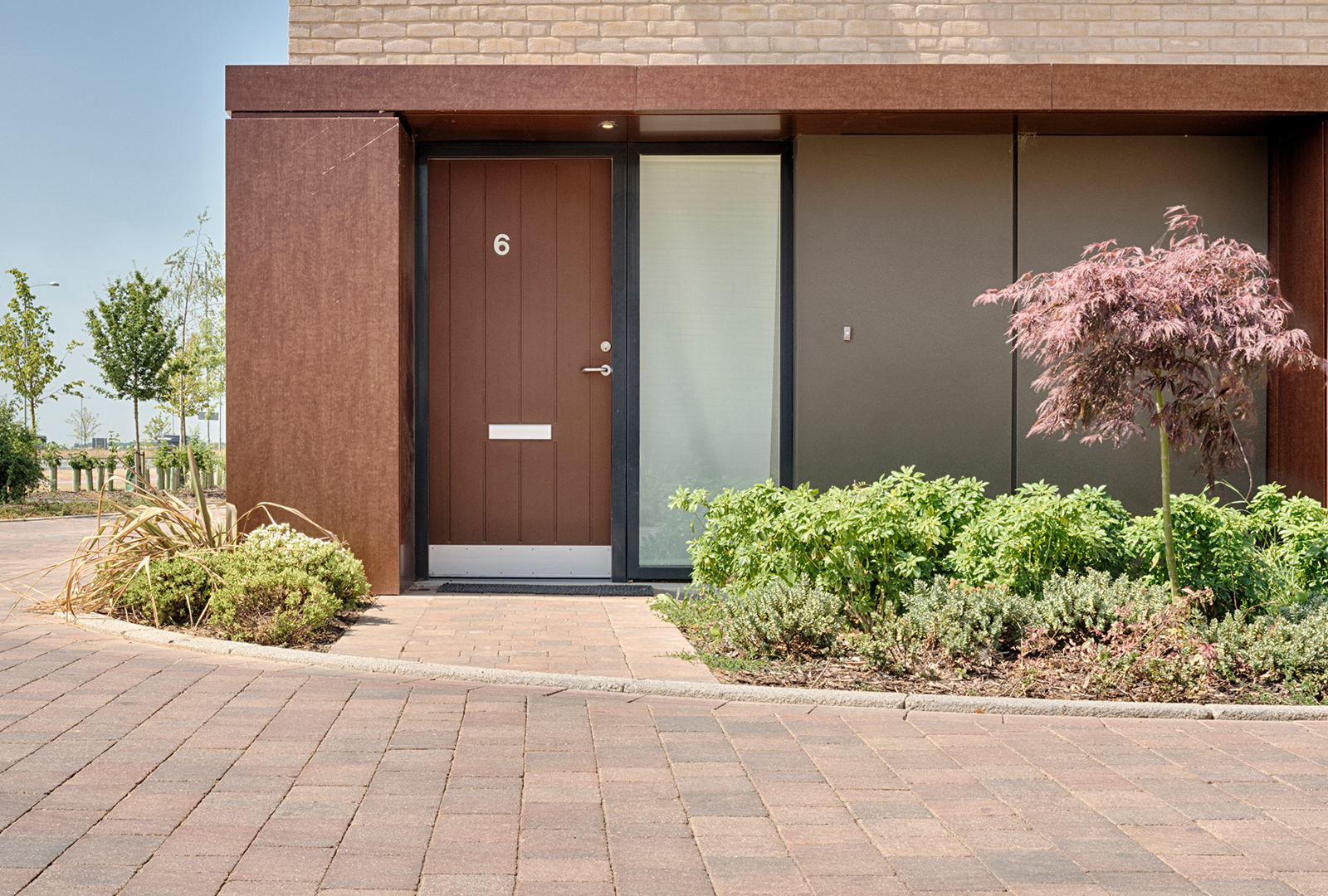
Marshalls explains how you can drive the cost out of home exterior projects.
According to research, it takes potential homebuyers less than eight seconds to decide whether or not they like a home, which means that investing in the exterior is vital for developers and homeowners looking to sell. Similarly, with a rise in electric vehicles and people spending more time at home, there has also been an increase in people investing their savings in transforming an existing front garden into a driveway.
But, it can be hard to know where to focus the majority of the budget when it comes to outdoor home projects. Is it worth spending money on expensive materials? Or should you scrimp on the finish in favour of the groundwork? Knowing where you can afford to cut costs and where you can’t can be less than straightforward when it comes to hard landscaping, but in this article, Marshalls offer some advice to get you started and help you explain the cost to customers.
Introducing the 80/20 rule
When it comes to choosing materials, it’s well worth knowing that surfacing materials frequently cost as little as 20 per cent of the installed cost of a pavement, driveway or road. The remaining 80 per cent of the cost of paving is below the surface. Getting the groundwork right is critical to the long-term success of an outdoor project; it affects both the look of it over time and the functionality. The 80/20 rule is easy to understand and can help you explain the finer project details to a customer too and give them the information they need to make decisions on the surfacing materials. A few pounds per square metre on blocks or flags makes little difference to the overall cost of the project, so it’s worth pricing up the products they love as well as lower budget options.
If you’re working on a new build project with multiple plots, you can use the 80/20 rule to calculate the benefit of a slight upgrade on the finish and the increased sale value that could bring. For example, on an average site, the difference between a standard paving product versus a premium one could cost as little as £40 per plot – whereas the overall benefit of the kerb appeal is much more significant when it comes to house prices.
Talk to suppliers early
Suppose you engage with manufacturers during the planning stage of a large project. In that case, you’ll receive expert, warrantied product and design advice, and you could drive significant cost out of the build and potential repair work caused by improperly installed paving. Doing this can free up budget for architects and designers to be just as creative on the outside as they are on the home’s interior, helping you with those all-important first impressions.
Save money with sub-base design
All external works (such as access roads or driveways) have a function. Primarily they’re there to do something; to provide durable, hardwearing surfaces that support heavy loads, withstand collisions and stay looking good for years to come. As explained by the 80/20 rule, the majority of the cost of hard landscaping is frequently hidden beneath the surface; the structural layers that provide the functional robustness of the installed system.
Making sure your sub-structure is engineered correctly can bring far more significant financial gains than cutting corners on the surfacing material, and this is where supplier advice can be worth its weight in gold. Enlisting expert advice, or taking the time to understand it entirely yourself, pays dividends when it comes to understanding what is needed and where value engineering can make a real difference. Value engineering is used to solve problems, identify and eliminate unwanted costs and improve function and quality and it’s key to driving the cost out of your sub-base. Ensure that the sub-structure at the core of your external works serves its purpose without being over-specified, and you’ll be creating a project that looks and stays beautiful.
Benefits of Sub-Base Design
- Environmental: Less energy and carbon used in excavation, less waste to dispose of, and less aggregate all add up to reduce the carbon footprint of your project.
- Practical: In areas where excavation is limited (to avoid services, for example), designs frequently make a block paved surface a realistic option where it wasn’t before.
- Repairs: A properly designed paving structure is much less likely to fail under loading pressure or become waterlogged in heavy rain.
- Financial: Crucially, design models combined with rationalised sub-base designs drive cost out of the project; from installing correctly engineered sub structures drive cost out of the project by reducing materials labour, machinery, transport and energy costs; making block paving a more cost-effective option than ever before.
All areas of the construction sector are being subjected to ever-increasing levels of financial pressure, and housing developments, extensions, and improvements are no different, so you must stay on top of costs. By taking the time to research and consider the specifics of the project you’re working on and say yes to supplier advice, you can increase profits and potentially pass on savings to customers too.
For more information about the products and advice offered by Marshalls, visit https://www.marshalls.co.uk/builders