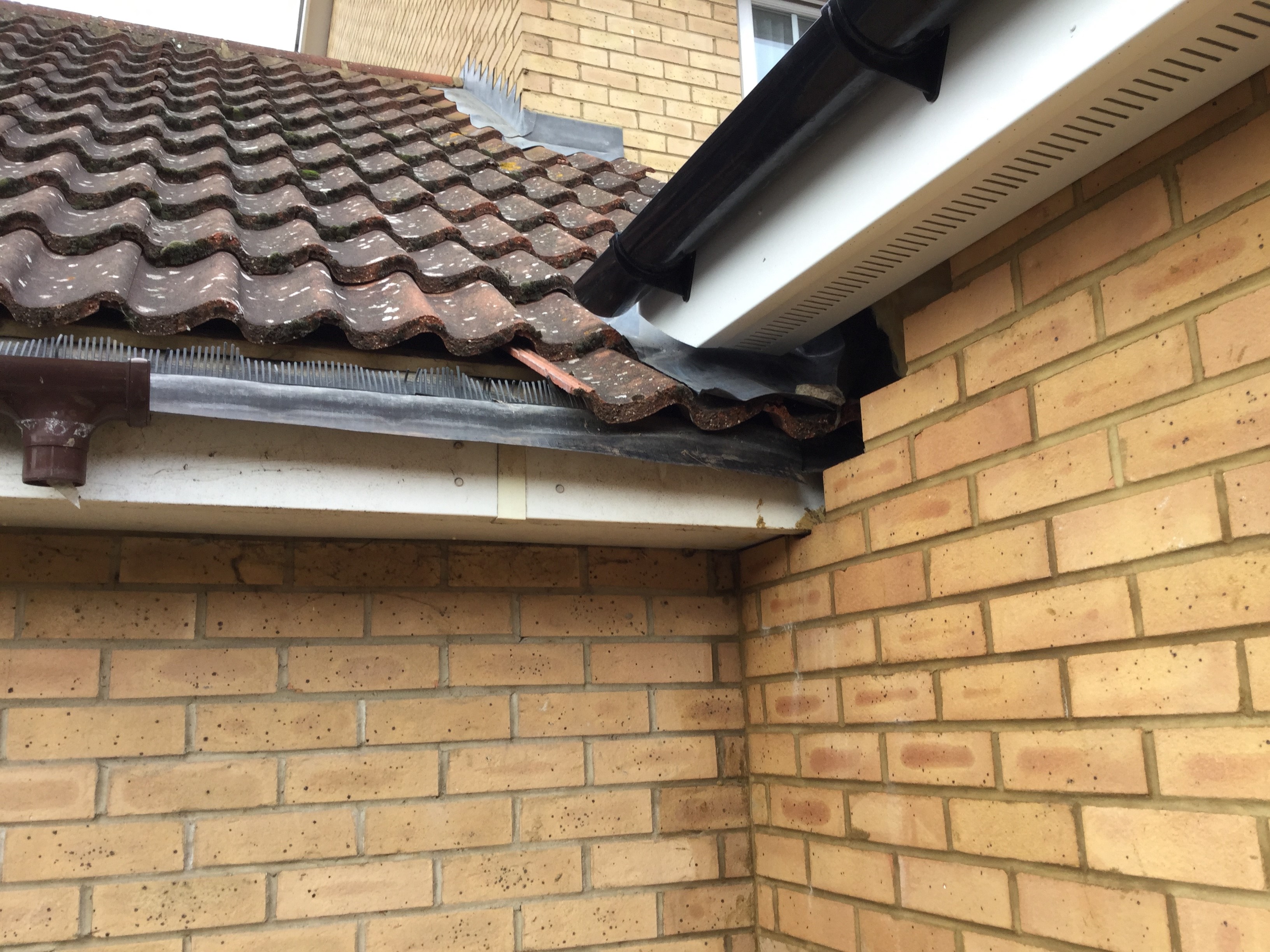
Our regular series, from a building inspector, reflects on some of the more unusual jobs (and scams) they see.
One of the many perks of working as a Local Authority building control surveyor is the often amusing and occasionally disturbing scams and construction defects that we come across from time to time when carrying out site inspections. Sometimes there are deliberate attempts to mislead us and other times we get well-meaning but inexperienced ‘builders’ who misuse their initiative to come up with new and unorthodox techniques for putting buildings together.
We are obliged to intervene when glaring safety hazards present themselves, and on more than one occasion I have had cause to serve a dangerous structures notice when temporary propping is holding out only by the grace of God. Several times I have persuaded groundworkers to come out of deep unstable trenches and remember a particular incident when the side of one collapsed literally seconds afterwards. The simple fellow seemed to find this quite amusing – perhaps I should have let natural selection take its course!
There are many funny tales of dodgy drain tests. The common scam is the double bung whereby the pressurised section is only a few centimetres long. A more inventive method witnessed by a colleague was when a builder put flaked rice into the water filled pipework in an attempt to seal up leaks in a soil and vent system. Well it worked for his car radiator!
I don’t doubt that over 39 years I was probably caught out by other more sophisticated ruses. It is often groundwork that’s involved and I remember a case as a trainee in St. Albans when a homeowner was carrying out a full underpin to his house foundation and thought it a good idea to dig a deep trench around the entire perimeter of the property to give working space prior to digging out individual bases. Not such a surprise when the undermined external walls collapsed into the trench and wrote off the house.
In another part of the country a colleague came across a chap who had taken recycling to an extreme by cutting up shopping trollies to use as reinforcement in a concrete raft foundation. Well, at least the local canal had a good clear out. If you want to see a great piece of video showing one catastrophic result of construction incompetence then google ‘LABC Chimney Collapse’. I hear that phrase ‘that won’t go anywhere’ a lot but sometimes it does.
Firestopping defects are quite common, and even the better builders seem to think that the pink foam is the universal fire resistant remedy for filling holes of all shapes and sizes and in all materials. In fact, most are only suitable for narrow linear gaps, and that’s only when faced up with an intumescent mastic.
Some of this stuff burns really well – as I have sometimes demonstrated to surprised customers – so I’d suggest you only use products from respected brands, and read the instructions for use. Another common error is the use of solvent-based grab adhesives to attach plasterboard cladding to structural steelwork. Very little chance that the 30 minutes fire resistance that the building regs look for would be achieved.
I could go on but space is limited. I hope you agree that these tales show the importance of LABC’s robust ‘boots on the ground’ inspection service rather than the ‘cyber inspection by photograph’ methods adopted by less professional outfits. By the way, if any of you want to tell me (anonymously) of some of those cleverer scams that might have caught me out then feel free to write in.
If you want to get in touch with the Building Introspector, or ask him a question, then you can contact him at pb@hamerville.co.uk