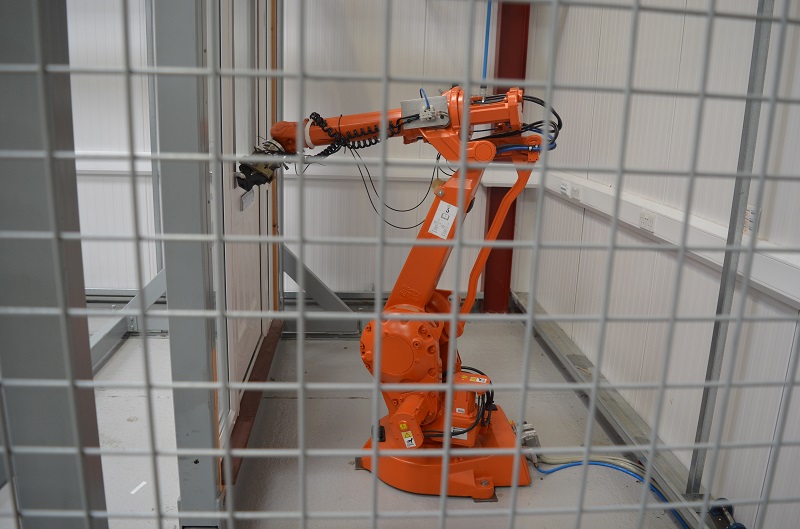
Professional Builder’s Kieran Nee visits BSI’s testing laboratory in Hemel Hempstead to what goes on behind the scenes to ensure the products you use are safe and secure.
Founded in 1901 by the designer of Tower Bridge, the British Standard Institution (BSI) has been producing standards for products longer than any other institution, and thus carries with it a great deal of respect. The institution, which acts as the UK’s official National Standards Body, provides CE certification as well as the nationally revered Kitemark certification.
CE marking, derived from the French for European Conformity, is, as Grahame Wackett, Construction Products Manager at BSI’s Hemel Hempstead laboratory, explains to me, a safety mark. It ensures that a product meets the minimum safety requirements to be sold in EU countries. The Kitemark, on the other hand, denotes long-lasting quality, and is extremely thorough in its testing.
“To retain Kitemark certification,” explains Floyd Merrison, Laboratory Operations Manager, “we do repeated, periodic assessments of the factory and repeated periodic testing of the product, to check compliance.
“It could be typically, once a year we’ll ask for a representative sample from the production line and we’ll do some critical tests on it – one perhaps the most likely to reveal any weaknesses in the product, and we maintain quality. We do factory visits to check how they continue to make the product.
“We don’t just look at one golden sample this way and then say ‘fantastic, you can forevermore produce that product.’”
After seeing the work being done in the laboratory at Hemel Hempstead, it’s fairly safe to say that the products being tested are truly put through their paces.
The most common items tested are windows and doors, and various contraptions tower over you clamping the products, preparing to subject them to a multitude of tests designed to replicate different environmental conditions. One such test I saw being carried out was in an apparatus called a Gusting Rig.
This essentially subjects the product to a forceful simulation of wind and rain, after which the rig is opened and the window checked for ingress.
The double glazing itself is also tested separately in a large modified oven, which regulates the temperature from -18° to +58° and maintains it at those temperatures for extended periods of time to ensure the units are fit for a wide range of climates.
The humidity inside the oven, Floyd tells me, is a whopping 95 per cent. The scientists in the lab then check the double glazing’s cavities for moisture and the egress of the gases contained within, using various complicated machines.
One of the more extreme tests doors and windows are put through involves a man with a tool bag attempting to break through the window – the point being to determine whether the window holds up well enough when faced with a burglar using easily obtainable tools.
Two robotic arms, affectionately named Jeff and Jazz, are tasked with the laborious job of unlocking, opening, closing and relocking a door 50,000 times in a row (a million for commercial use doors). Working non-stop and to within 0.2mm accuracy, these robots replicate a lifetime of usage within seven days.
These are just a few elements of the thoroughness, inhuman precision and desire to go above and beyond a product’s normal specification that each product is subjected to at BSI’s lab. This is what you’re getting when you purchase a Kitemark certificated product – not just a sticker!
For more information visit www.bsigroup.com