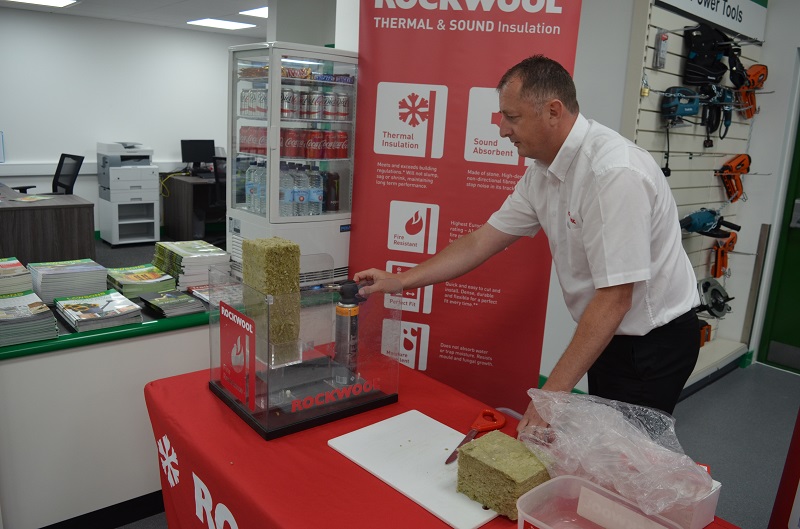
Rockwool’s Contractor Days are designed to educate tradesmen on the advantages of stone wool insulation. Professional Builder’s Lee Jones visits a south-west London builders’ merchants to find out more.
In almost any given street, one glance along the rooftops of our capital’s properties will tell you that the building industry is looking up.
Quite literally as it happens because, for the tradesmen of London, loft conversions remain a lucrative source of work, and it is Rockwool’s superior acoustic, thermal and fire-resisting properties that make it the perfect partner for these projects.
You might think, then, that hosting a day which is designed to extol the virtues of mineral wool insulation in a busy south London builders’ merchants would be preaching to the converted but, despite the fact that Rockwool has been with us as a material for more than 70 years, the manufacturer works hard to ensure that its trade customers are aware of just how many benefits there are to specifying and installing its product.
It is, of course, not just loft conversions where Rockwool will find its place because the range of applications, in everything from cavity walls to intermediate floors, is extensive – and growing.
“Most of the people we encounter who are unaware of Rockwool will assume that it’s made of glass, because that’s just what they think insulation has to be made of,” explains Chris Ludlow, one of the company’s Contractor Support Specialists, and our guide through the benefits of stone wool for the day.
Chris then proceeds to set up one of his key demonstrations – a blow torch with its flame directed at close range onto a sample piece of 50mm Rockwool – an exhibition of fire resistance which is a significant clue to its actual composition.
“Rockwool is a stone-based material and that’s what makes it virtually impervious to a flame that’s burning at nearly 1,200°C like this one,” he enthuses. “Compare that to a glass-based product and it would simply disintegrate in a few minutes.”
“That’s amazing!” declares John Fry, a local builder who – predictably enough – was working on a loft conversion in nearby Morden.
“We do use Rockwool, and I knew it about its fire resistance, but seeing it demonstrated like that does bring it home to you.” But that’s not the only feature that’s turning up the heat on its competitors, as our demonstrator’s boxes of tricks continues to reveal.
Rockwool is actually a combination of basalt, mined in Ireland, and slag, a by-product of the steel industry. Arranged in a furnace in alternate layers the melting point of both materials is achieved at around 1,500°C, at which point the molten substance is fed into a spinning machine which splits it into non-directional fibres.
Once cooled, and in order to achieve the required density, the slabs are then subjected to a series of compression rollers, all of which leaves a finished product with a significant resistance to sound waves.
As a society we are increasingly plagued by noise, and our domestic spaces are fast becoming a refuge from the relentless soundtrack of the modern world. Or indeed they are the chance to subject our ears to our racket of choice without the risk of incurring an ASBO.
In either instance it is Rockwool’s sound insulating properties which will come into its own. At this point Chris produces another of the tools of his promotional trade in the form of a device which emits 140 decibels of drum perforating din.
Place the offending article in a box lined with 70mm Rockwool Sound Slab insulation, however, and a blare which is a full 100 decibels above Part E sound transmission upper limits is rendered virtually mute.
As a stone-based insulation Sound Slab simply stops noise in its tracks, which makes it ideal for metal stud partition or timber stud walls, everywhere from bedrooms, bathrooms and home offices, to TV and games rooms, whilst those aforementioned rooms in the roof will be far more liveable spaces with Sound Slab in the intermediate floors.
Of course, insulation is first and foremost specified for its thermal properties and here again Rockwool is the solid performer amongst its peers, but it also has the advantage of being water repellent. In addition, the material actually breathes, which means it won’t trap moisture and will resist rot and mould, making it perfect for cavity walls.
All of the products in the Rockwool Thermal & Sound Insulation range are made of the same mineral wool material but each fabricated for its particular application.
With the manufacturer’s Thermal Roll, for instance, the clue as to its shape is very much in the name, whilst in cavity insulation Rockwool Cavity Batt for brick and block is 455mm wide – a size that corresponds to the spacing of wall ties.
Similarly, insulation for stud work is 400 and 600mm wide, all of which should eliminate any unnecessary cutting. In fact, if everything is set out correctly the only material that should need trimming is for the internal corners, in which case any simple serrated knife will suffice.
The same principle extends to the company’s sound insulation, where a 1,200mm length of material can be positioned into intermediate floors or stud walls.
Sound Slab features a choice of 50, 70 and 100mm, with the 50 and 70mm sizes recommended for walls. If you are installing into 75mm walls, for instance, the manufacturer advises that 50mm insulation is used in order to maintain a slight air gap. The 100mm thickness tends to be used for floor/ceiling separation.
“Any builder who’s stripped out glass-based insulation from a loft will tell you that it’s one of the worst jobs you’re faced with on site,” explains Wandsworth builder Phil Draper, “but with Rockwool there’s none of that. Indeed, as the Rockwool roadshow ably demonstrates it could well be time to hit the wool.
For further information on the Rockwool Thermal & Sound Insulation range click here.