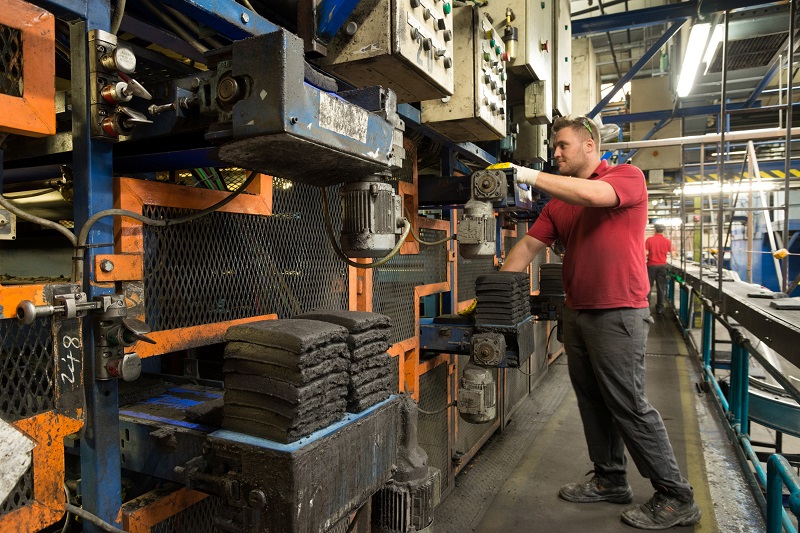
It’s concrete and clay tiles have been helping to keep a roof over our heads for the best part of one hundred years but as PB recently discovered, Redland is also making significant “material” gains in a lesser known sector of the roofing market.
Like its instantly recognisable logo, it’s reasonable to surmise that the Redland business has experienced its fair share of ups and downs during a century of trading but as they say, through adversity comes greatness!
In fact it was shortly after the end of the First World War, in 1919 that the Redhill Tile company took the name of its local town in Surrey and began trading in concrete tiles.
Business was brisk and in 1926 the company played an integral role in the construction of post-war Britain, supplying concrete tiles, desperately needed in the absence of coal fired clay tiles that were unavailable due to the general strike.
However, it was the conclusion of the Second World War and the introduction by the company of the “49” which quite literally laid down the marker for the internationally renowned Conglomerate we recognise today.
With the capital city blitzed beyond recognition, this first ever single lap concrete tile proved to be a real boon to installers and, with its attractive appearance and ready availability, quickly established itself as “the tile that reroofed London.”
This was quickly followed up by the Redland 50 Double Roman, the first variable head lap tile and the rapid expansion of the business was maintained through the sixties with new factories and acquisitions in both cement and clay.
A number of milestones for the industry were subsequently notched up including the first wind tunnel, the first dry verge system and the first dedicated training centre in South Cerney.
In the portfolio also sits another historic product – the widely known Rosemary Clay Classic – a tile with a longer pedigree than any other in the UK.
Having first been produced in 1838, the tile maker George Lewis was so delighted with the quality of the product he was making that he decided to name it after his daughter Rosemary.
Today the product is produced at Redland’s clay plant in the midlands and in many merchants you are still likely to hear roofers asking for a Rosemary when they want a plain clay tile.
Yet despite all the obvious success, the company was becoming increasingly aware that something was missing from its impressive portfolio – namely a slate offering.
Despite representing a small percentage of the overall UK roofing market, the building heritage of certain parts of the country guaranteed a steady demand for a slate product, both in new build and refurbishment projects.
More importantly, customers were prepared to pay the price for a premium product.
It was against this background that in the early eighties Redland set up an experimental facility in Rassau, 15 miles up the valley from Cwmbran – which gave Cambrian slate its name. Here they developed the industry’s first reconstituted interlocking slate tile.
With waste slate acquired from the quarries to the North, the painstaking business began of mixing raw product to a cocktail of resins, stone, glass fibre reinforcement and various binders to produce a dough like premix which could be moulded on an industrial scale to produce a credible alternative to a natural slate product.
Fundamental to this process was an innovative tile design which incorporated a separate channel to keep the interlock clear of the clip and allow impeded water to run off as well as weather bars to protect the head of the slate from driving rain.
Three pre-formed strategically placed nail holes with a raised section for protection against water ingress creates a tile that not only looks like the real thing, but can be laid and fixed considerably quicker than its counterpart.
As Plant Manager Helen Aldersley who has spent 30 years at Rassau recalls, “with such an ambitious undertaking there were bound to be a few frustrations along the way as we strove for that magic ingredient although the excitement in being the first to bring a product like this to market was tangible.
“There were a lot of people in white coats in those early days with pretty sophisticated chemistry sets, and everything including the moulds, machinery and holding silos had to developed from scratch.
“However, within a relatively short time span we were able to create five tile moulds to represent the most common natural welsh slate options and in 1985 the first Cambrian tiles rolled of the production line.”
Continues Helen “it was all very labour intensive then and we probably never imagined that 30 years later we would still be in Rassau but modern technology has enabled us to continually refine the process. with levels of efficiency amongst the best of any tile production process.
“Those early doubters should never have underestimated the company’s determination to add to its long list of firsts for the industry”, enthuses Helen; and it seems it wasn’t just the roofing industry that was sitting up and taking notice because in 1991 the Cambrian won the Queen’s Award for Technological Achievement.
Today, each Cambrian tile consists of over 60 per cent natural welsh slate, which equates to significant weight saving benefits both for the roofer and those structures where loading is already an issue.
Around 30,000 slates per day with just a handful of rejects, which themselves can be recycled, are currently being produced to meet demand but there is capacity to significantly beef this up in the future.
And that day is just around the corner, predicts Head of Marketing David Patrick, “reconstructed slate is still a niche market and represents a small fraction of the Braas Monier Building Group empire but we are confident the there is a wonderful opportunity to convert many more roofing companies to the benefits of Cambrian.
“Part of the education process for us is to get across to roofers the need to look at whole project costs rather than just the cost of a single tile.
“On that basis alone we make no bones about being more expensive but when you factor in speed of installation, amount of actual roof coverage and things like reduced weight over natural slate and fibre cement versions and material consistency, the reconstituted tile is a very attractive alternative to traditional slate options.
“We are also up front that the finished roof will take around 18 months to weather down to a natural slate appearance but this is actually a very small timescale for a product that is guaranteed for 60 years.
Continues David, “after that initial settling in period it would be impossible to tell the difference by the naked eye with the riven surface and dressed edges adding to the real effect.
“A number of very high profile projects including a new club house at the Celtic Manor resort for a recent Ryder Cup contest and superbly appointed lodges bear testament to this fact.
“We are also seeing the product increasingly specified by housebuilders to differentiate their more prestigious projects. At the same time we are also keen to extend its appeal in to the smaller reroofing and extension sectors. where again speed of installation is paramount.”
He adds, “the other benefit for the roofer is that Cambrian doesn’t need to be holed or graded on site and can perform down to 15 degrees. It comes with all of the necessary accessories such as vented ridges, hips and gullies in three colours, slate grey, heather and langdale green.
“Of course there are the considerable environmental benefits to be had from the recycling of heaps of waste created by quarrying natural slate.”
It may have taken the company the best part of its first seventy years to get into the reconstituted tile business but as it has subsequently kept proving its better to be “slate” than never.
Did you Know?
Since opening, Rassau has produced 180,000,000 Cambrian slates. With a standard size of 300 x 336mm, that’s 18,144,000m2 and enough to cover 2,835 full size football pitches. It would take 63,492 tiles to cover one average pitch.
For more information on Redland click here.