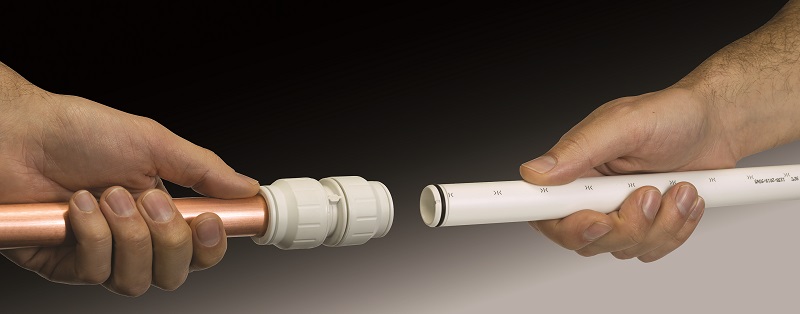
Lee Flood, Director of Quality at JG Speedfit and Nigel Sanger, Technical Manager at JG Speedfit, look at the rigorous testing that should be conducted on plastic pipes and fittings.
There are two primary quality tests that can be performed on pipes and fittings. The first thing we assess with every batch of fittings that comes off our production line, is how much pressure the fitting can withstand before bursting.
This is an important indication of the strength of the fitting, even when installed in extreme environments. JG Speedfit fittings typically achieve in excess of 50 bar. This ensures that fittings supplied to builders offer the required high standard of leak-proof durability.
The second test you would expect to see performed is a dedicated pressure test, which JG Speedfit bases upon the British Kitemark standard BS7291.
This test helps us to guarantee the life of a fitting for 25 years following installation, and measures the strength of a fitting according to time, temperature, and stress. To calculate this, a typical 15mm push-fit fitting is exposed to pressures of up to 44 bar for an hour.
This indicates how effectively the fitting can hold a joint under the typical conditions that you would expect from a standard first fix plumbing site, this test is altered according to the size of the fitting we produce.
These tests are necessary to guarantee Kitemark performance, but JG Speedfit goes one step further and adds a third test, based upon the international standard ISO21003 for multi-layered pipes.
For example, this subjects a typical 15mm fitting to 12 bar of pressure for 22 hours at 95ºc, and is a recognised sign of quality for plumbers and installers globally.
These tests may seem comprehensive but the UK is generally good at carrying out quality assessments such as these, and they are key to ensuring reliable, leak-proof connections for plastic fittings.
Something builders need to be mindful of is the importance of onsite testing in addition to the stringent quality assurance measures employed by JG Speedfit and other manufacturers.
On site pressure testing has long been standardised for plumbers for commercial new-build projects but often in retrofit scenarios and domestic projects, this can be overlooked due to time pressures.
People often do not realise how much pressure can build up in a plumbing system, especially perhaps, when a boiler or component such as a pressure reducing valve malfunctions, which is why onsite pressure testing is so important.
JG Speedfit recommends that, in addition to carrying out mandatory first fix tests as outlined by legislation, installers test the pipework at two bar for 10 minutes, then ten bar (typically five times the average operating pressure) for a further 10 minutes to ensure that the pipes and fittings will be leak free following installation.
It is important not to skip the 2 bar test as this is the typical operating pressure and will be the most likely test to show up a leak caused by fine scratches on the surface of a pipe caused by poor handling or storage.
When initially filling the system up with water, join all the first fix pipework together using a manifold which will allow all of the pipework to be tested at the same time.
Unlike the quality tests that are carried out by JG Speedfit, onsite pressure testing is not always mandatory and often depends on the type of installation, and the time pressures facing the plumber or installer.
This is why JG Speedfit is committed to educating customers on best practice surrounding pressure testing.
Only with the right guidance from suppliers, manufacturers, and industry leaders, will the plumbing sector be able to ensure a leakproof connection in every project, without standards falling short under pressure.
For further information on JG Speedfit click here.