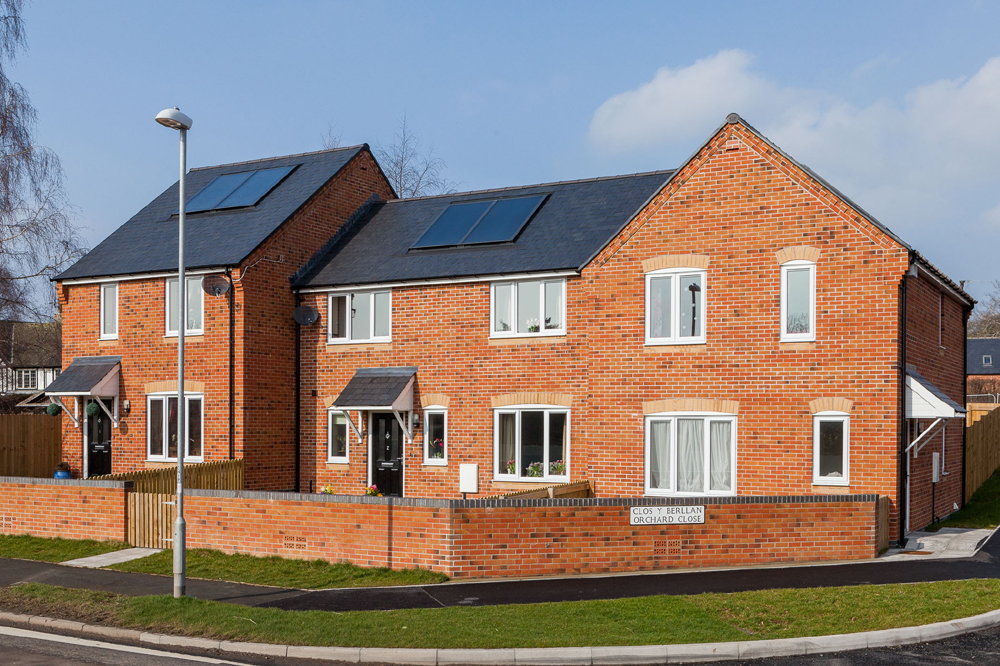
Chris Stanley, housing manager, at the Concrete Block Association examines how we can improve the energy efficiency of our homes.
The ‘digital revolution’ is a term which has recently gathered much traction across all aspects of society, particularly in the construction industry. Nowhere is this more apparent than within the housebuilding sector.
Over the last decade, we’ve seen the introduction of smart homes, which include gadgets such as smart meters. Likewise, low-carbon energy is no longer uncommon in a domestic setting. But these are far from the only development in energy use in the home. As recently highlighted by the Energy Saving Trust, the transformation in the last century has been huge.
An earlier survey, Connecting with homeowners: making energy efficiency relevant (2016) showed that public awareness of energy efficiency is growing. To put this into perspective, 90 per cent of those polled had completed a home improvement that included an energy efficiency upgrade.
Although the possibilities of tech are exciting and inspiring, we need to consider the impact of the building materials first. Before getting ahead of ourselves with futuristic gadgets, it’s essential we first understand the importance of the fabric of the building and the way materials are specified. A robust understanding of energy efficiency enables builders to select the most appropriate materials available for a particular build.
The built environment is one of the most significant contributors to CO2 emissions globally, and residential buildings have a larger impact than all other buildings put together. In the UK structures are responsible for around 40 per cent of the country’s total carbon footprint, with heating alone making up about 10 per cent.
Consequently, energy efficiency has become an essential consideration for builders. Not only do we need to reduce energy consumption for the sake of the environment; energy efficiency affects everything from personal wellbeing to utility bill levels. We need to deliver homes that enhance the way we live in the long term, and the CBA is offering the industry guidance to achieve that.
Pushing the envelope
The first port of call when reducing a building’s reliance on heating or cooling is always a high-performing building envelope. Anyone involved in the trade will know what a difference appropriate insulation, glazing and windows, as well as airtight construction and minimisation of thermal bridges all make. Although the shape and orientation of a house plays a role, being flexible with these is rarely straightforward, especially with small-scale projects.
Even so, balance is everything and you need a certain air change rate. An overly airtight home will result in poor air quality and lack of moisture control. We have to consider natural energy gains from people, appliances and the sun to rule out overheating, as the Energy Savings Trust piece concedes.
Next in line to be addressed is ventilation. High-performance controlled ventilation or mechanical heat recovery ventilation (MHRV) helps reduce energy thrown away with extracted air, therefore minimising energy wastage. The future will also see the introduction of smart ventilation controls to manage our systems of high performance controlled ventilation.
Crossing the thermal bridge
Over the last 25 years, our new build housing stock has witnessed a sea change in terms of quality. Successive changes to Approved Document Part L, have made this possible, yet there is more room for improvement. Even with the leaps made in airtightness and insulation, thermal bridging remains a problem.
Thermal bridges occur along the lines of intersection between different building elements. The two most common instances are a break in insulation or an area where an element with a higher thermal conductivity penetrates the insulation.
A significant 30 per cent of a building’s heat loss can be caused by a thermal bridge. What’s more, the negative impact is heightened the better the insulation is elsewhere in the structure. Therefore, we must pay greater attention to this during the planning stage of a build if we are to build homes that serve us far into the future.
Naturally both client and builder will want to find the most cost-efficient way to comply with Part L. To help builders find the most economical way to deliver a project, many of our CBA members provide thermal bridging details and guidance.
Thermal bridging Ψ (Psi) values have to be calculated for specific details. Armed with an understanding of this, builders will be able to select the right product. The details and corresponding independently-calculated Ψ values for masonry construction are available on the CBA website.
The crucial values
So how do you ensure the building envelope is high-performance and a house energy efficient? Finding the appropriate U-value (or thermal transmittance) is fundamental, and so is knowing how this can be achieved.
The necessary calculation is complex, however we have provided a tool to help: a simple, free-to-use online U-value calculator. We created this especially to assist those unfamiliar with how this crucial number can be identified. It’s highly accurate, and even if more detailed calculations become essential, this is the perfect place to start.
At the CBA, we’re always researching to find new solutions and tools to benefit builders and the wider construction industry. Our U-value calculator and thermal bridging details are just a few examples of our efforts to meet the ever-increasing demands on the trade across the UK.