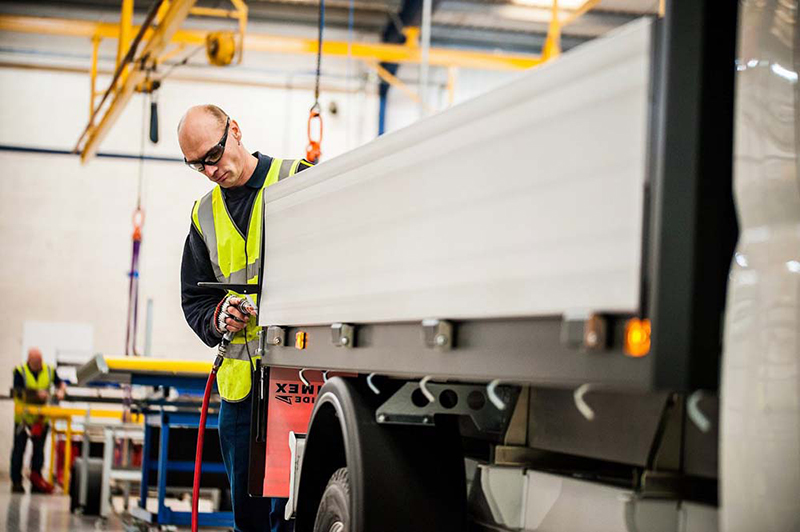
Professional Builder travels to Telford to meet Ingimex, the company behind Volkswagen’s tippers and dropside vans.
It might not quite do justice to the complexity behind Ingimex’s body conversions, but describing the process as ‘off-the-shelf’ is, in fact, a huge compliment. That’s how its seamless integration with Volkswagen’s Crafter and Transporter vans has been described, and it’s easy to see why.
It’s a testament to the logistics and engineering at play that customers purchasing a tipper or dropside van from a dealer may not even realise that a third party has played a role at all. The Engineered to Go initiative offers customers a selection of pre-defined bodywork options, which they can order directly at the dealership, seeing the price upfront alongside the usual specifications. The scheme offers an easy way for customers to get the conversions that they want, plus a single invoice, matching vehicle/conversion warranty and peace of mind.
Ingimex make their way through a phenomenal amount of vehicles, producing 3,000 bodies each year. Most of the components used by the firm are produced on site in Telford, a site which measures nearly seven acres. The company has invested £1.8m in the factory over the past year, which now includes manufacturing capabilities including 3D CAD product design, turret punching, laser cutting folding machines, MIG/TIG welded fabrications, CNC milling and punching with multi axis section bending and a hydraulic test rig with corrosion testing capabilities. The company plans to carry on investing around £500,000-£800,000 in its premises each year.
Volkswagen account for 24 per cent of Ingimex’s annual output, which is a mix of the core products they offer and more specialised offerings. The process is a simple one, with the average conversion taking only around 40 minutes. The van reverses from the yard into one of the three bays, where all the components and tools needed are neatly arranged. Part of the Ingimex philosophy is that as much as possible is bolted together rather than welded, meaning it can be put together more easily and, if any repairs need doing, can be more easily taken apart. This process enables the workers on the floor to get through 12 dropsides, eight tippers and seven Lutons a day.
Aluminium is the metal of choice. Although pricier, the material is a lot lighter and easier to handle than steel. Of course, you can’t do anything to reduce the strength of the bodies, and the design process is a careful balancing act between weight and strength.
Thanks to the likes of Ingimex and Volkswagen, the tipper truck is undergoing something of an image revamp. No longer the preserve of some less-than-savoury characters, tippers and dropsides are enjoying their moment in the sun as professionally minded builders wise up to their potential. The smart, modern finishes on Ingimex’s products certainly helps in this regard, and you can no doubt expect to see more of these conversions fly off the shelf in the coming years.
A look at the dropside…
Market leading payload
Powder coated aluminium corner posts extend above board height to form lateral stops.
Three level load lashing and a 400kg gantry capacity.
Board and lock assemblies tested to a burst load of 1.7 tonnes.
Platform is a one piece, 15mm thick, full birch non-slip deck, top fitted for easy replacement.
…and the tipper
Platform is made from high tensile steel and dip e-coated in a six stage process for long lasting finish
Double skinned aluminium sideboards used throughout
Strong and striking tailboard with side mounted locks to eliminate trapped fingers