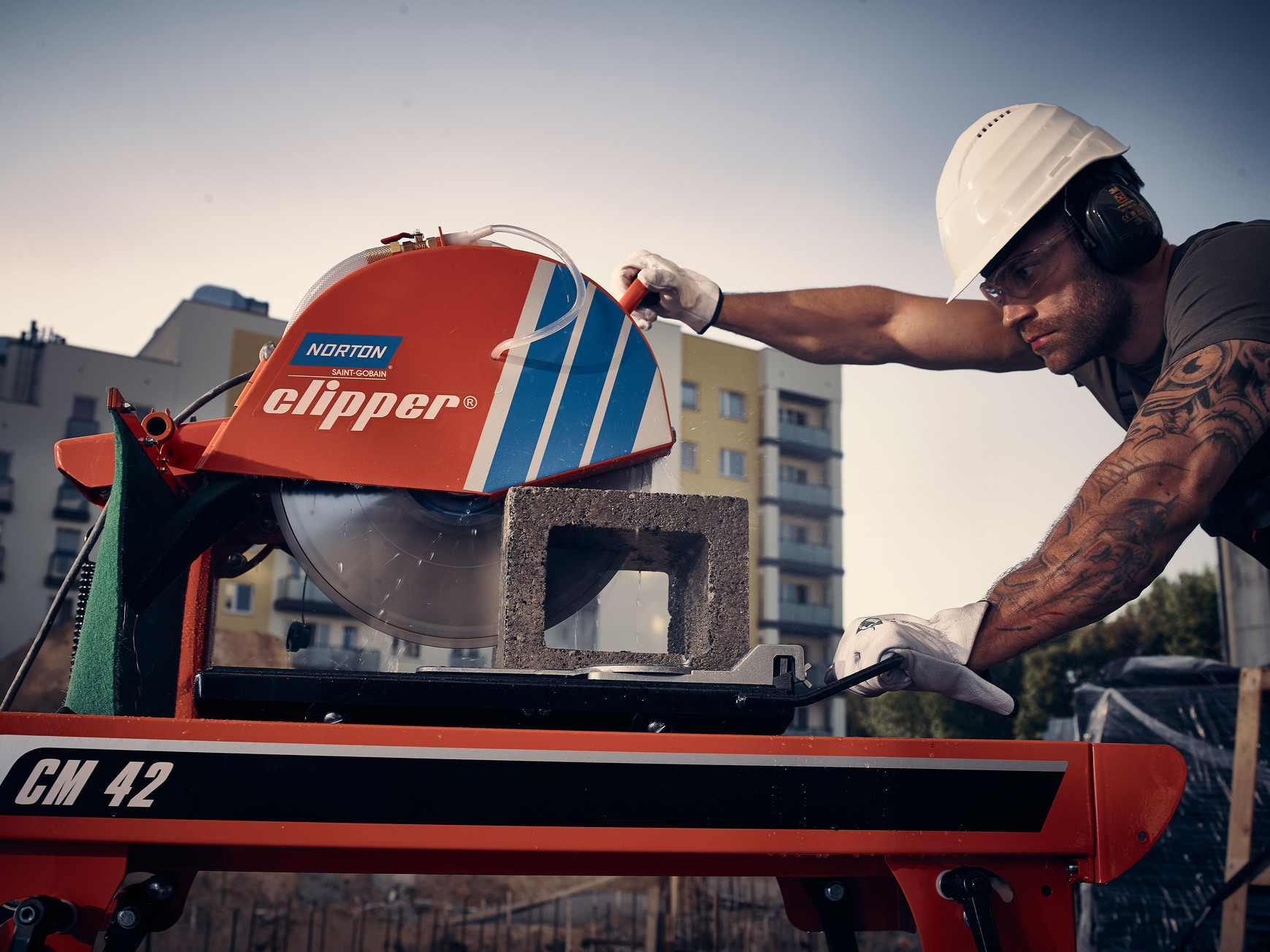
Dom Waring, Technical Manager for Hire, Machines and CP Engineering at Norton Clipper, discusses how contractors can make the most of their equipment
Research has found that over 70 per cent of construction companies have experienced decreased turnover in recent years, with 80 per cent having to postpone or cancel upcoming work. As the cost of raw materials saw a 40-year high in 2021 and is set to treble in 2022, profits may continue to strain.
Construction workers could not do their job without tools and machinery. Big or small, there is some equipment that a contractor can never enter a site without, and others that are only used occasionally but are essential to the delivery of a job.
There are only two options to choose from when acquiring construction equipment – hiring or buying. Each has its cost and time-saving benefits, but it’s essential for construction companies and tradespeople to think about their own individual circumstances to truly get the best value.
First, let’s look at buying. The main reason businesses will choose to invest in construction tools and machinery is when they know workers will get plenty of use from them on the majority of jobs. In this case, purchasing is more cost-effective in the long term and saves the hassle of repeatedly arranging rental from hire merchants.
Once equipment has been purchased, availability is pretty much guaranteed as and when needed, providing all upcoming projects and workforce numbers have been taken into account. High demand, particularly in peak periods such as springtime, and machine maintenance can mean that some equipment may be hard to get hold of when hiring.
Having brand new, unused equipment is also one of the big benefits of purchasing tools and machinery. The owner has complete control over how equipment is looked after and maintained.
But while buying might seem like the logical choice, there are equal arguments to suggest that hiring is the best option in many cases. Most prominently is if the equipment is only needed for a short period or for one specific job. From both a financial and a sustainability point of view, it can be unnecessary to spend a lot of money on equipment that is used only once or infrequently.
Hiring can even be the only feasible option if businesses are short on cash flow and unable to purchase the machine upfront. This also provides the option to ‘try before you buy’, allowing operators to test the performance of machinery and whether it’s suitable for the business’ needs.
While one of the pros of buying is that owners have complete control over the upkeep of machinery, some labourers actually prefer not to have that responsibility. Renting equipment allows businesses to leave this in the capable hands of the hire merchant. Hire merchants will perform thorough maintenance and checks and assist in rare cases of rented products experiencing issues or breakdowns.
Similarly, construction companies also often choose to hire so that they don’t need to spend time and money on servicing and sourcing replacement parts. Less equipment also means less storage required, and therefore any additional costs to rent or buy storage space can be cut as well.
Similar to when buying new equipment, there are considerations to bear in mind when hiring to ensure operators are getting value for money:
- How old the equipment is, and how long the merchant has had it
- The reliability and range
- Whether the machine needs access to a water source permanently or if it has a water tank
- The features and benefits, such as whether it has vibration dampening technology
- Whether the machine is simple and easy to use
- Whether a smaller alternative machine can be used instead to achieve the same result
- The overall cost
With cost savings to be had on both sides, businesses and trades must think about which method is best for them. Overall, construction machinery hire can become expensive and labour intensive in the long-term. However, it does take away the ongoing maintenance, storage and transport costs involved in owning equipment. When deciding which option is best, businesses should balance the cost-effectiveness of buying versus hiring for the required length of time.
Norton Clipper want to ensure its construction equipment is available to both buy and hire from local merchants to give operators as much choice as possible.
For further information on the Norton Clipper range visit https://www.nortonabrasives.com/en-gb