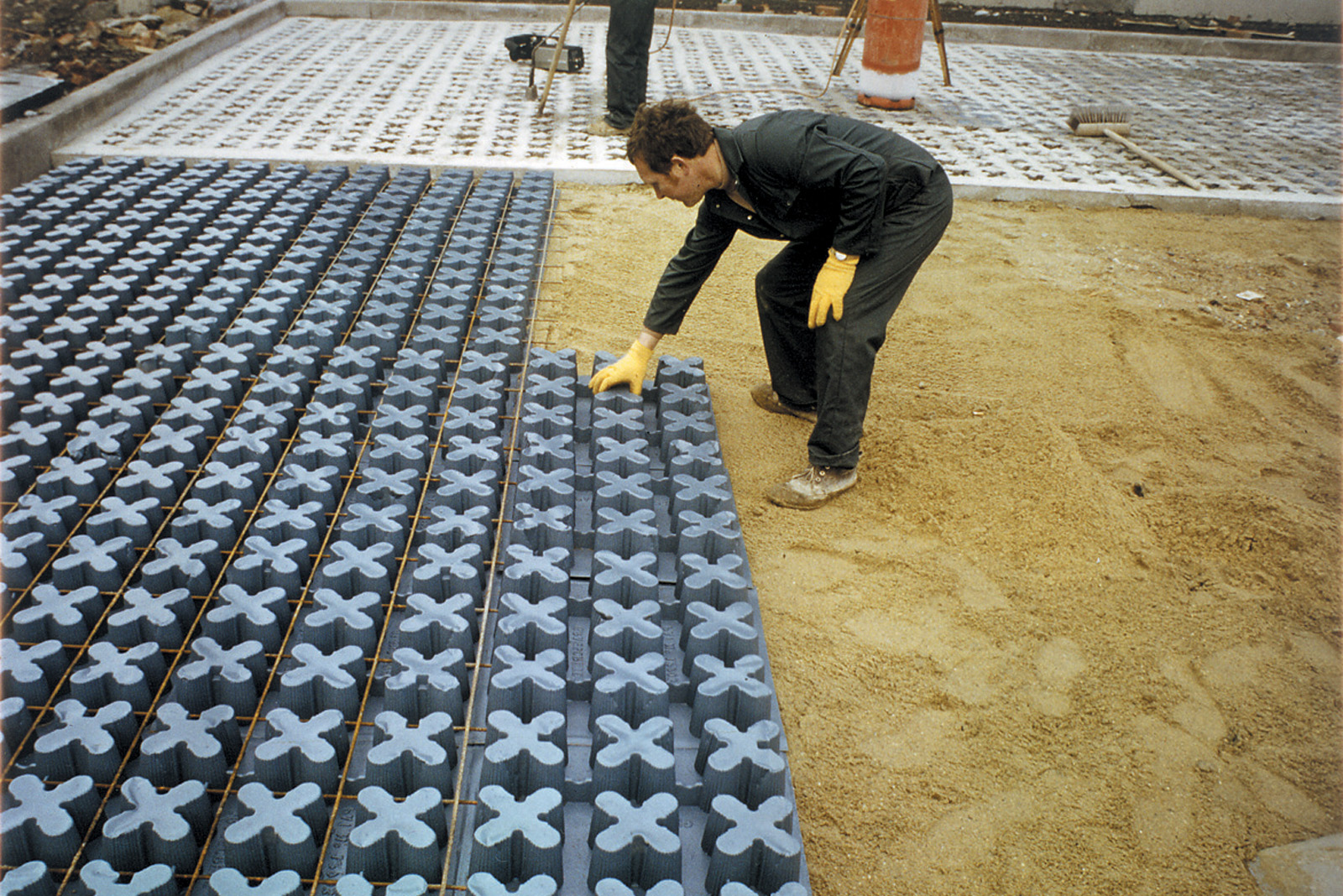
With Grass Concrete marking 50 years as a ‘growing’ concern, Professional Builder’s Lee Jones examines the company’s unique contribution to sustainability.
Most of the products we take for granted in the building industry have been developed as a reaction to prevailing trends, but there are those very few that emerge way ahead of their time, and Grasscrete certainly falls into the latter category. When Huddersfield architect, Jack Blackburn first developed this unique grass paving solution some fifty years ago issues of sustainability were at the periphery, whilst they now take centre stage. “We were actually publishing pamphlets on sustainable drainage management back in the ‘70s,” explains Grass Concrete MD, Bob Howden, “and in the early days it was perceived as occupying a particular niche. Today, Grasscrete is more relevant than ever, and pitches at a much wider marketplace.”
When the first green shoots of Grasscrete emerged from the drawing board of its inventor all that was available at that time were pre-cast concrete blocks. Their shape is largely determined by the fact that they have to be removed from a mould during manufacture, providing a form that doesn’t make them particularly conducive to growing grass, or to permeability. By contrast, the Grass Concrete solution is a cast-in-situ, reinforced product with inherently improved grass growth and hydrology.
Indeed, Grasscrete now sets the benchmark in its field and can boast both flood alleviation and prevention credentials. It can permeate at up to 90 per cent of the flow of natural grass and, thanks to a uniform percolation, will slow that flow of water and manage drainage much more effectively in the process. It is a property which is as equally effective on large flood storage areas, designed to prevent downstream inundation, as it is in the humble domestic driveway.
Unlike impermeable block paving surfaces, the system will replenish the ground in a very natural way, optimising the drainage capability, and easing the pressure on rainwater infrastructure during heavy rainfall. Add to that a robust construction that can comfortably accommodate heavyweight vehicles, a surface that can absorb CO2, and the aesthetic appeal of a grass covering, and you have a product that is set to quite literally grow and grow.
So just how does it work? All of the products that make up the Grasscrete concept are manufactured in the UK, in sites that include Buxton and Shrewsbury. Moreover, in order to ensure an expert installation every time, Grass Concrete has its own contracting division. In a testament to the robustness of the system, the company reports that examples of its grass paving on specific project are going strong some fifty years on, with some significant structural advantages over the alternatives.
The components that make up this sustainable paving solution begin with a sub-base material, a 10-20mm sand layer, 600x600mm formers laid side by side, and steel mesh positioned between the up-stands of those formers. It’s then time to pour the self-compacting, flowing concrete, which is levelled to the top of the formers. When the concrete is cured, it is the formers that create voids that are then filled with topsoil, seeded and watered. Bob Howden outlines the benefits: “Sustainable Urban Drainage Systems (SuDS) has become the catch all term for anyone looking to mitigate the effects of surface water run-off, but they can have their problems, especially if they’re transporting water to one particular area or hole in the ground. Grasscrete is designed to operate as a natural solution rather than an engineered one, with the added benefit of an aesthetic appeal.”
“We work closely with developers in delivering the system on driveways,” he enthuses, “and with many developments now including a surface water storage pond we are often called in to line the side and slopes of these, or construct an access road. Again, it’s the kind of application which can offer a natural look to the finished project.”
The product range itself has also evolved, with grass roofs, retaining walls and variations on the grass paving theme, all introduced over the last five decades, as Bob recounts: “From the success of Grasscrete it was evident that there was a market gap that couldn’t be filled with that product alone so the next step was the launch of the pre-cast concrete Grassblock.” The latter provides a safer walking platform and a lower level of traffic vibration than is often associated with studded blocks. Furthermore, the interconnecting lugs help to form a tight interaction with neighbouring blocks to limit movement, whilst a continuous concrete surround to each soil pocket makes this solution ideal for slope protection in helping to prevent soil from being washed down the slope.
Elsewhere, its Grassroad plastic pavers originally hail from the USA, with Grass Concrete now owning the exclusive European licence. The company has also acquired the British rights to the dry build, concrete and modular Betoconcept retaining wall system. Most of that range is plantable and includes the low height Betoflor interlooking block walling, right up to the 22m Betotitan and a number of options in between.
In the modern world, almost every company is at pains to promote its green credentials, but Grass Concrete is an enterprise that has held that ethos dear since its inception. It is a principle that is reflected in the raw materials of the Grasscrete system, where its void formers have always and continue to be manufactured from recycled plastic, and where recycled fill materials are used in sub-bases wherever possible. With a product range that scores not just in terms of sustainable drainage, but equally through carbon sequestration and a reduction in the urban heat island effect, the company will continue to be a green giant in ground engineering.
For further information on the range of products available from Grass Concrete visit www.grasscrete.com/