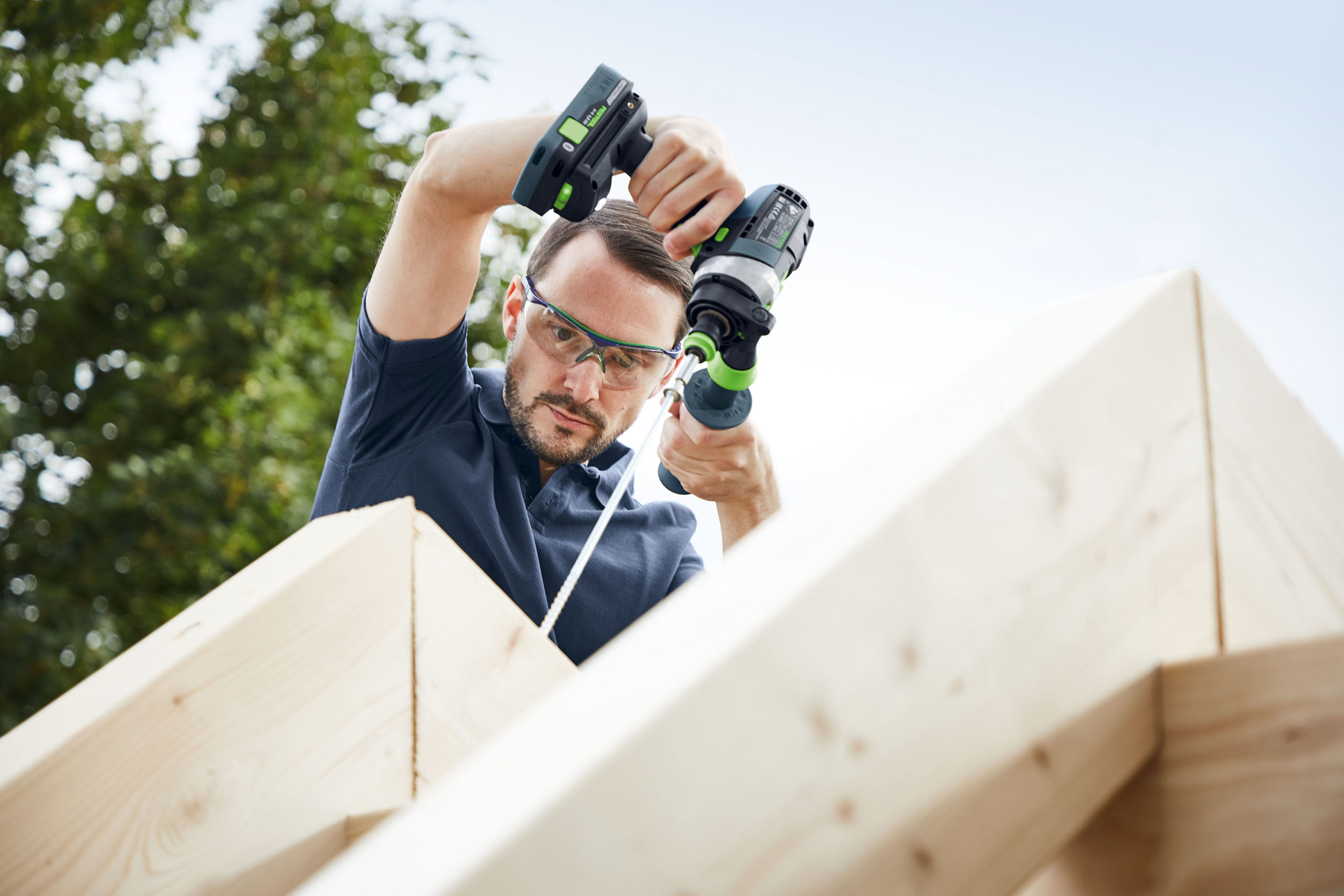
Which screwdriver is best suited to the different tasks and applications? One with two or maybe even four speeds? 10.8V or 18 V batteries? An impact screwdriver, a percussion drill or a drill? A specialist tool or one for all applications? The variety of cordless screwdrivers can seem overwhelming. But one thing is clear: The only way to achieve the best result is to work with a tool that is precisely matched to the application.
The torque setting and selection of the right speed are the two most important factors for achieving a perfect screwdriving result, since they precisely adjust the screwdriving process to the screw properties, screw diameter and, most importantly, the material.
Cordless impact screwdrivers are taking tradespeople by storm. Those seeking a solution only for screwdriving – with optimum performance and endurance and no strength-sapping back torque – will benefit most from the TID 18 impact screwdriver. This tool enables screwdriving over long periods without tiring. Cordless impact screwdrivers are significantly lighter, more compact and enable working more comfortably – especially for repetitive screwdriving tasks. The essential feature here is the extremely low back torque, made possible by the tangential hammer mechanism which minimises impact on the wrist during screwdriving.
Georg von dem Bussche, Festool trainer and master carpenter, explains: “The smart T-mode is an especially practical feature of the TID 18 cordless impact screwdriver. When fitting sheet metal to wood with self-tapping screws, the tool detects the transition between the different materials and automatically adapts the speed. To drill into the sheet metal as effectively as possible, the tool starts off driving in the screw with a high speed, low torque and without impact loading. Once the torque increases due to the commencing screwdriving process in the wood, the machine independently reduces the speed and only then begins impact loading.”
The range of applications that are possible with the QUADRIVE TDC cordless drill and QUADRIVE TPC 18/4 cordless percussion drill with four-speed gearbox is extremely versatile. The four-speed powerhouses are ideal both for screwdriving tasks involving high torques and large diameters as well as quick and powerful drilling. As a rule of thumb, the larger the drilling diameter is, the lower speed needs to be.
Festool has developed a clever solution for switching between speeds, with both tools allowing users to switch from one gear straight to any other. Fixed stops ensure clear engaging, saving you time and guaranteeing full control while screwdriving. KickbackStop protects the wrist Both the QUADRIVE TDC and TPC ensure that your hand twisting dangerously if the tool suddenly jams is a thing of the past. The intelligent KickbackStop minimises the risk of this happening. How does it achieve that? A sensor detects a tool jam and stops the drive within a fraction of a second – before the force can be transferred to your wrist.
Drilling or screwdriving? That is not a question you have to ask with cordless drills, which is why the all-rounder tools in the 18 V class are so popular. The T 18+3 cordless drill and the C 18 cordless drill in the ergonomic C-shape are also equipped with fully electronic torque setting, the Centrotec quick-change system and special attachments, a brushless motor and high-performance battery packs. That makes them a universal solution for most screwdriving and drilling applications.
Many tradespeople often use maximum torque for screwdriving. With the T 18+3 and C 18 cordless drills, you can switch from maximum torque to a lower torque setting simply by pressing a button. “Our cordless drills feature fully electronic torque setting and shut-off. This is particularly useful for screwdriving, since it allows for a very precise adjustment of force and speed. And that is exactly what many tradespeople value, as they prefer screwdriving with high precision,” explains von dem Bussche, and adds: “If screws are overtightened or screw heads are even shorn off, this is usually due to mistakenly using maximum torque for screwdriving. This damages both the screw and drill bit.”
“Precise screwdriving requires an ideal torque, a high-quality bit and a tool chuck that can be changed quickly. The bits are very important for the power transfer, which is why they need to be of a high quality. Magnetic bits and bit holders are particularly useful. Professionals appreciate it when bits, drills and attachments can be changed quickly. That is why we have combined chuck and bit holder in one with our unique Centrotec tool chuck: It is half the size and 80% lighter than comparable chucks. It fits all cordless drills from Festool with FastFix interface and enables users to change tools in a matter of seconds, which has proven to be a very popular feature in practice,” confirms von dem Bussche.
The EX-UNI eccentric attachment is recommended for screwdriving close to the edge. The angle can be adjusted simply by turning the ring. The same principle is used for adjusting the angle on the AN-UNI angle attachment. You no longer need to remove the attachment from the tool first. The DC UNI FF depth stop is perfect for achieving reproducible screw fittings in façade cladding or patio flooring. The rubberised protective ring prevents undesirable, visible impressions in the surface. The DD-DC depth stop is perfect for fitting drywall panels, since it allows many screws to be placed with a uniform screwdriving depth and offers an optimal view of the screwdriving site thanks to its narrow design.
To watch an explanatory animated video on the Festool TPC 18 hammer mechanism https://www.youtube.com/watch?v=En-wjv6_ad8
To watch a video on the TPC / TDC Quadrive cordless drill driver https://www.youtube.com/watch?v=hEXm8zLd5o0
For an explanation of the TID 18 hammer mechanism visit https://www.youtube.com/watch?v=qWHUGX9rzlk